Filter News
Area of Research
News Topics
- (-) 3-D Printing/Advanced Manufacturing (28)
- (-) Fusion (13)
- (-) Nanotechnology (17)
- Advanced Reactors (14)
- Artificial Intelligence (8)
- Big Data (11)
- Bioenergy (12)
- Biology (5)
- Biomedical (21)
- Biotechnology (2)
- Buildings (1)
- Chemical Sciences (5)
- Clean Water (2)
- Climate Change (10)
- Composites (1)
- Computer Science (39)
- Coronavirus (23)
- Critical Materials (2)
- Cybersecurity (4)
- Decarbonization (1)
- Energy Storage (21)
- Environment (29)
- Exascale Computing (3)
- Frontier (1)
- Grid (7)
- High-Performance Computing (3)
- Isotopes (8)
- Machine Learning (8)
- Materials (2)
- Materials Science (37)
- Mathematics (2)
- Mercury (1)
- Microscopy (8)
- Molten Salt (2)
- National Security (2)
- Neutron Science (30)
- Nuclear Energy (31)
- Physics (13)
- Polymers (7)
- Quantum Science (14)
- Security (3)
- Space Exploration (2)
- Summit (17)
- Sustainable Energy (24)
- Transformational Challenge Reactor (5)
- Transportation (15)
Media Contacts
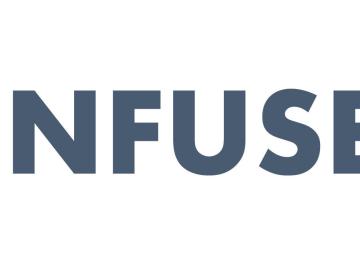
The Department of Energy announced awards for 10 projects with private industry that will allow for collaboration with DOE national laboratories in accelerating fusion energy development.
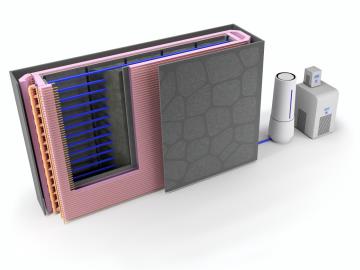
Oak Ridge National Laboratory researchers used additive manufacturing to build a first-of-its kind smart wall called EMPOWER.

The inside of future nuclear fusion energy reactors will be among the harshest environments ever produced on Earth. What’s strong enough to protect the inside of a fusion reactor from plasma-produced heat fluxes akin to space shuttles reentering Earth’s atmosphere?
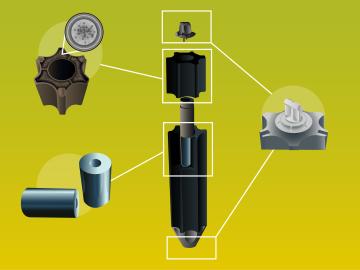
It’s a new type of nuclear reactor core. And the materials that will make it up are novel — products of Oak Ridge National Laboratory’s advanced materials and manufacturing technologies.
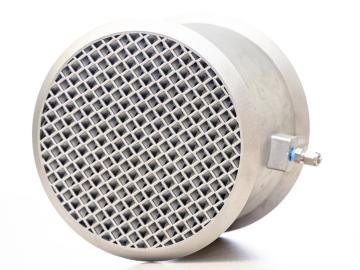
Oak Ridge National Laboratory researchers have designed and additively manufactured a first-of-its-kind aluminum device that enhances the capture of carbon dioxide emitted from fossil fuel plants and other industrial processes.
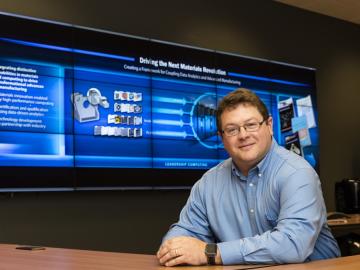
The Society of Manufacturing Engineers, known as SME, has named William Peter, director of Oak Ridge National Laboratory’s Manufacturing Demonstration Facility in the Energy and Environmental Sciences Directorate, among its 2020 College of SME Fellows.
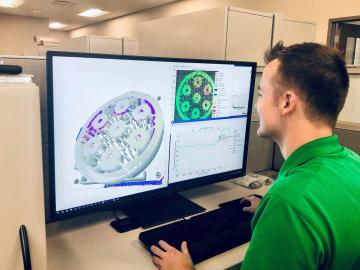
Oak Ridge National Laboratory researchers have developed artificial intelligence software for powder bed 3D printers that assesses the quality of parts in real time, without the need for expensive characterization equipment.
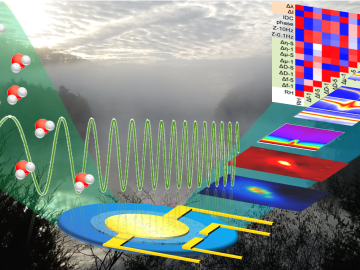
An all-in-one experimental platform developed at Oak Ridge National Laboratory’s Center for Nanophase Materials Sciences accelerates research on promising materials for future technologies.
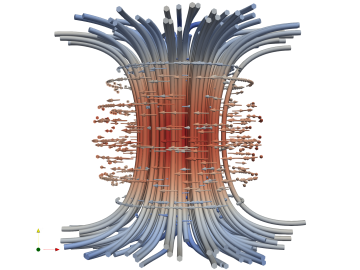
Combining expertise in physics, applied math and computing, Oak Ridge National Laboratory scientists are expanding the possibilities for simulating electromagnetic fields that underpin phenomena in materials design and telecommunications.
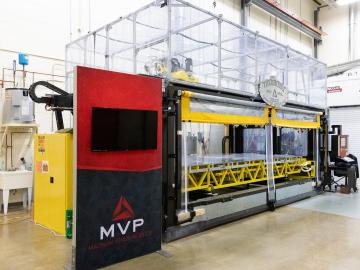
ORNL has licensed two additive manufacturing-related technologies that aim to streamline and ramp up production processes to Knoxville-based Magnum Venus Products, Inc., a global manufacturer of fluid movement and product solutions for industrial applications in composites and adhesives.