
Filter News
Area of Research
- Advanced Manufacturing (4)
- Biology and Environment (4)
- Clean Energy (34)
- Computer Science (1)
- Fusion and Fission (4)
- Fusion Energy (4)
- Materials (9)
- Materials for Computing (3)
- National Security (1)
- Neutron Science (3)
- Nuclear Science and Technology (11)
- Quantum information Science (1)
- Supercomputing (7)
News Topics
- (-) 3-D Printing/Advanced Manufacturing (28)
- (-) Fusion (13)
- (-) Sustainable Energy (24)
- Advanced Reactors (14)
- Artificial Intelligence (8)
- Big Data (11)
- Bioenergy (12)
- Biology (5)
- Biomedical (21)
- Biotechnology (2)
- Buildings (1)
- Chemical Sciences (5)
- Clean Water (2)
- Climate Change (10)
- Composites (1)
- Computer Science (39)
- Coronavirus (23)
- Critical Materials (2)
- Cybersecurity (4)
- Decarbonization (1)
- Energy Storage (21)
- Environment (29)
- Exascale Computing (3)
- Frontier (1)
- Grid (7)
- High-Performance Computing (3)
- Isotopes (8)
- Machine Learning (8)
- Materials (2)
- Materials Science (37)
- Mathematics (2)
- Mercury (1)
- Microscopy (8)
- Molten Salt (2)
- Nanotechnology (17)
- National Security (2)
- Neutron Science (30)
- Nuclear Energy (31)
- Physics (13)
- Polymers (7)
- Quantum Science (14)
- Security (3)
- Space Exploration (2)
- Summit (17)
- Transformational Challenge Reactor (5)
- Transportation (15)
Media Contacts
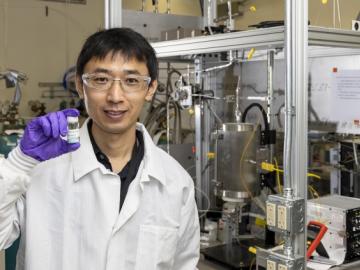
Prometheus Fuels has licensed an ethanol-to-jet-fuel conversion process developed by researchers at Oak Ridge National Laboratory. The ORNL technology will enable cost-competitive production of jet fuel and co-production of butadiene for use in renewable polymer synthesis.
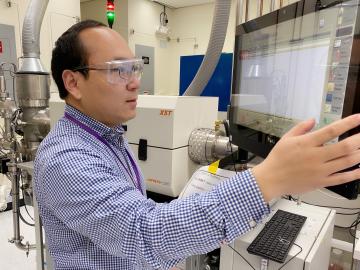
About 60 years ago, scientists discovered that a certain rare earth metal-hydrogen mixture, yttrium, could be the ideal moderator to go inside small, gas-cooled nuclear reactors.
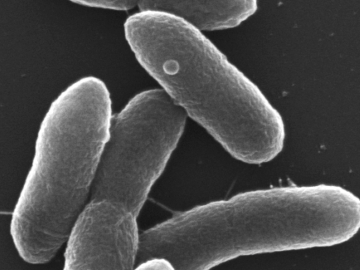
ORNL scientists have modified a single microbe to simultaneously digest five of the most abundant components of lignocellulosic biomass, a big step forward in the development of a cost-effective biochemical conversion process to turn plants into
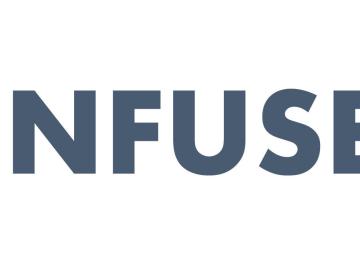
The Department of Energy announced awards for 10 projects with private industry that will allow for collaboration with DOE national laboratories in accelerating fusion energy development.
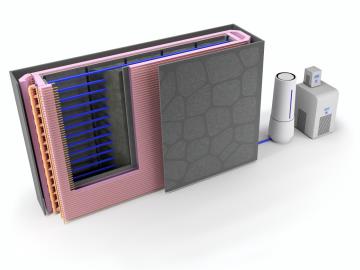
Oak Ridge National Laboratory researchers used additive manufacturing to build a first-of-its kind smart wall called EMPOWER.

The inside of future nuclear fusion energy reactors will be among the harshest environments ever produced on Earth. What’s strong enough to protect the inside of a fusion reactor from plasma-produced heat fluxes akin to space shuttles reentering Earth’s atmosphere?
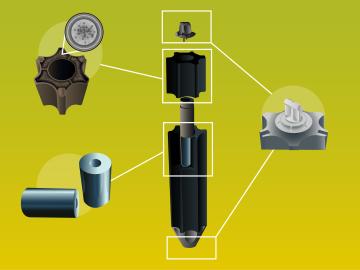
It’s a new type of nuclear reactor core. And the materials that will make it up are novel — products of Oak Ridge National Laboratory’s advanced materials and manufacturing technologies.
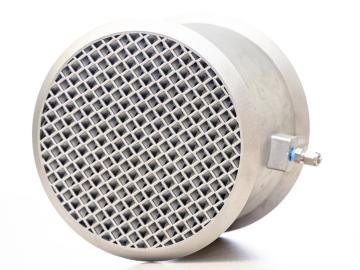
Oak Ridge National Laboratory researchers have designed and additively manufactured a first-of-its-kind aluminum device that enhances the capture of carbon dioxide emitted from fossil fuel plants and other industrial processes.
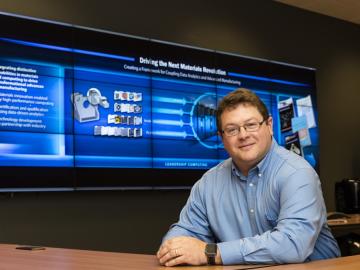
The Society of Manufacturing Engineers, known as SME, has named William Peter, director of Oak Ridge National Laboratory’s Manufacturing Demonstration Facility in the Energy and Environmental Sciences Directorate, among its 2020 College of SME Fellows.
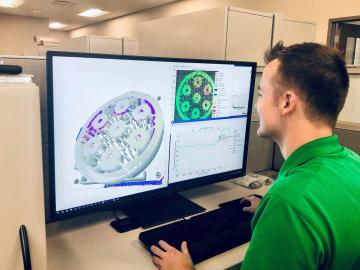
Oak Ridge National Laboratory researchers have developed artificial intelligence software for powder bed 3D printers that assesses the quality of parts in real time, without the need for expensive characterization equipment.