
Filter News
Area of Research
News Type
News Topics
- (-) 3-D Printing/Advanced Manufacturing (5)
- (-) Materials Science (9)
- (-) Molten Salt (1)
- (-) Nanotechnology (3)
- (-) Neutron Science (3)
- Advanced Reactors (2)
- Artificial Intelligence (4)
- Big Data (4)
- Biomedical (1)
- Clean Water (2)
- Composites (1)
- Computer Science (17)
- Energy Storage (4)
- Environment (5)
- Exascale Computing (1)
- Fusion (2)
- Microscopy (2)
- Nuclear Energy (7)
- Physics (1)
- Polymers (1)
- Quantum Science (1)
- Space Exploration (2)
- Summit (6)
- Sustainable Energy (3)
- Transportation (5)
Media Contacts
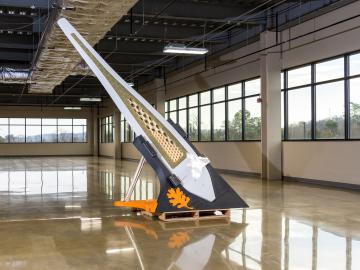
In the shifting landscape of global manufacturing, American ingenuity is once again giving U.S companies an edge with radical productivity improvements as a result of advanced materials and robotic systems developed at the Department of Energy’s Manufacturing Demonstration Facility (MDF) at Oak Ridge National Laboratory.
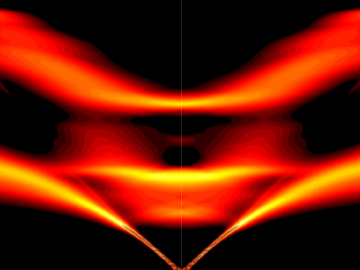
Scientists have discovered a way to alter heat transport in thermoelectric materials, a finding that may ultimately improve energy efficiency as the materials
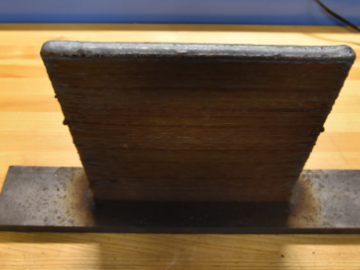
A novel additive manufacturing method developed by researchers at Oak Ridge National Laboratory could be a promising alternative for low-cost, high-quality production of large-scale metal parts with less material waste.

Researchers used neutron scattering at Oak Ridge National Laboratory’s Spallation Neutron Source to investigate the effectiveness of a novel crystallization method to capture carbon dioxide directly from the air.

Scientists have tested a novel heat-shielding graphite foam, originally created at Oak Ridge National Laboratory, at Germany’s Wendelstein 7-X stellarator with promising results for use in plasma-facing components of fusion reactors.
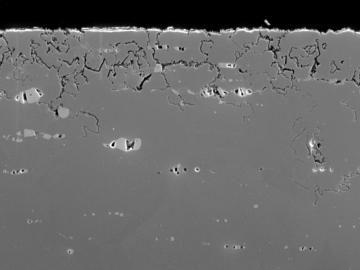
Oak Ridge National Laboratory scientists analyzed more than 50 years of data showing puzzlingly inconsistent trends about corrosion of structural alloys in molten salts and found one factor mattered most—salt purity.