Filter News
Area of Research
News Topics
- (-) Bioenergy (4)
- (-) Composites (4)
- (-) Molten Salt (1)
- (-) Nanotechnology (6)
- 3-D Printing/Advanced Manufacturing (19)
- Advanced Reactors (1)
- Artificial Intelligence (1)
- Biology (1)
- Biomedical (1)
- Biotechnology (1)
- Buildings (10)
- Chemical Sciences (9)
- Clean Water (5)
- Climate Change (1)
- Computer Science (7)
- Critical Materials (3)
- Cybersecurity (2)
- Decarbonization (8)
- Energy Storage (13)
- Environment (15)
- Fossil Energy (1)
- Fusion (4)
- Grid (12)
- Hydropower (1)
- Isotopes (2)
- Materials (19)
- Materials Science (12)
- Mercury (1)
- Microelectronics (1)
- Microscopy (3)
- National Security (1)
- Neutron Science (10)
- Nuclear Energy (8)
- Partnerships (4)
- Physics (7)
- Polymers (4)
- Quantum Computing (2)
- Security (1)
- Simulation (1)
- Space Exploration (1)
- Sustainable Energy (8)
- Transportation (17)
Media Contacts
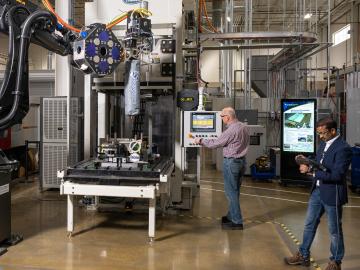
Researchers at ORNL are extending the boundaries of composite-based materials used in additive manufacturing, or AM. ORNL is working with industrial partners who are exploring AM, also known as 3D printing, as a path to higher production levels and fewer supply chain interruptions.

In fiscal year 2023 — Oct. 1–Sept. 30, 2023 — Oak Ridge National Laboratory was awarded more than $8 million in technology maturation funding through the Department of Energy’s Technology Commercialization Fund, or TCF.
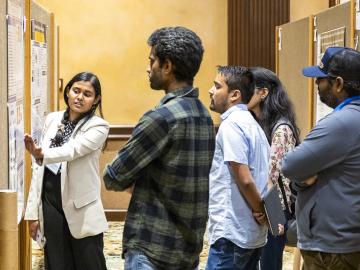
Speakers, scientific workshops, speed networking, a student poster showcase and more energized the Annual User Meeting of the Department of Energy’s Center for Nanophase Materials Sciences, or CNMS, Aug. 7-10, near Market Square in downtown Knoxville, Tennessee.
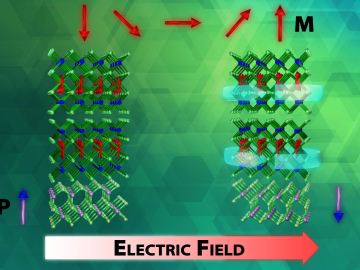
An advance in a topological insulator material — whose interior behaves like an electrical insulator but whose surface behaves like a conductor — could revolutionize the fields of next-generation electronics and quantum computing, according to scientists at ORNL.
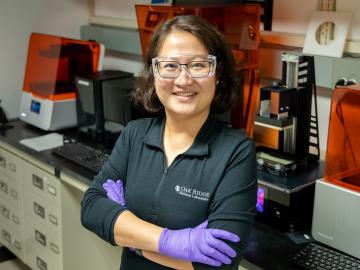
Growing up in China, Yue Yuan stood beneath the world’s largest hydroelectric dam, built to harness the world’s third-longest river. Her father brought her to Three Gorges Dam every year as it was being constructed across the Yangtze River so she could witness its progress.
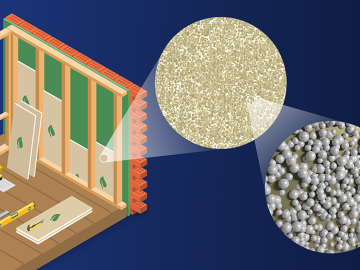
Scientists at ORNL developed a competitive, eco-friendly alternative made without harmful blowing agents.
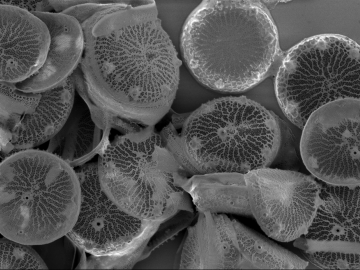
Students often participate in internships and receive formal training in their chosen career fields during college, but some pursue professional development opportunities even earlier.
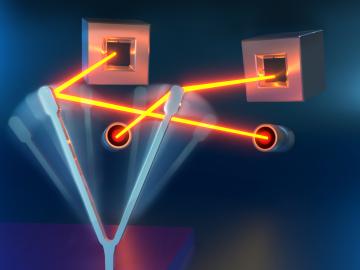
Researchers at ORNL and the National Renewable Energy Laboratory took inspiration from flying insects to demonstrate a miniaturized gyroscope, a special sensor used in navigation technologies.
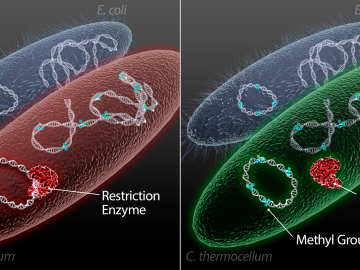
Scientists at the US Department of Energy’s Oak Ridge National Laboratory have demonstrated a method to insert genes into a variety of microorganisms that previously would not accept foreign DNA, with the goal of creating custom microbes to break down plants for bioenergy.
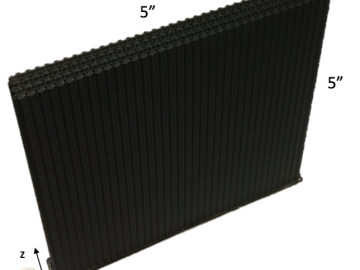
A team including Oak Ridge National Laboratory and University of Tennessee researchers demonstrated a novel 3D printing approach called Z-pinning that can increase the material’s strength and toughness by more than three and a half times compared to conventional additive manufacturing processes.