Filter News
Area of Research
- (-) Advanced Manufacturing (6)
- (-) Supercomputing (5)
- Biology and Environment (2)
- Clean Energy (23)
- Computer Science (1)
- Fusion Energy (1)
- Isotopes (1)
- Materials (10)
- Materials for Computing (2)
- National Security (2)
- Neutron Science (2)
- Nuclear Science and Technology (2)
- Quantum information Science (3)
- Transportation Systems (1)
News Topics
- (-) 3-D Printing/Advanced Manufacturing (7)
- (-) Isotopes (1)
- (-) Molten Salt (1)
- (-) Quantum Science (1)
- (-) Transportation (2)
- Advanced Reactors (2)
- Artificial Intelligence (2)
- Big Data (4)
- Bioenergy (1)
- Biology (1)
- Biomedical (3)
- Chemical Sciences (1)
- Climate Change (1)
- Composites (1)
- Computer Science (16)
- Coronavirus (2)
- Cybersecurity (1)
- Energy Storage (2)
- Environment (2)
- Frontier (1)
- Fusion (2)
- High-Performance Computing (1)
- Machine Learning (2)
- Materials (2)
- Materials Science (5)
- Nanotechnology (2)
- National Security (1)
- Neutron Science (1)
- Nuclear Energy (2)
- Physics (1)
- Polymers (1)
- Space Exploration (1)
- Summit (5)
- Sustainable Energy (3)
Media Contacts
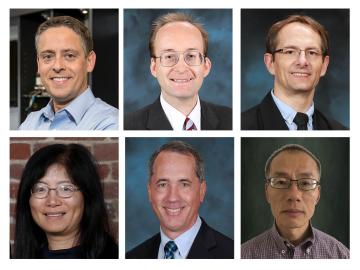
Six scientists at the Department of Energy’s Oak Ridge National Laboratory were named Battelle Distinguished Inventors, in recognition of obtaining 14 or more patents during their careers at the lab.
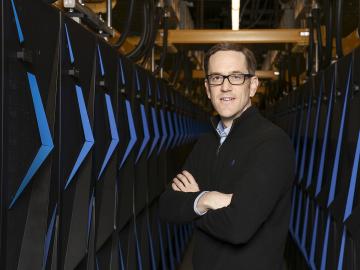
The annual Director's Awards recognized four individuals and teams including awards for leadership in quantum simulation development and application on high-performance computing platforms, and revolutionary advancements in the area of microbial
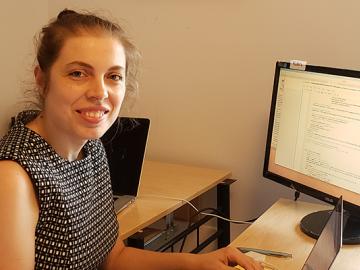
Kübra Yeter-Aydeniz, a postdoctoral researcher, was recently named the Turkish Women in Science group’s “Scientist of the Week.”
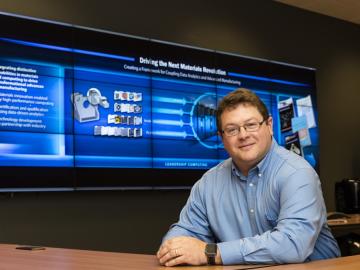
The Society of Manufacturing Engineers, known as SME, has named William Peter, director of Oak Ridge National Laboratory’s Manufacturing Demonstration Facility in the Energy and Environmental Sciences Directorate, among its 2020 College of SME Fellows.
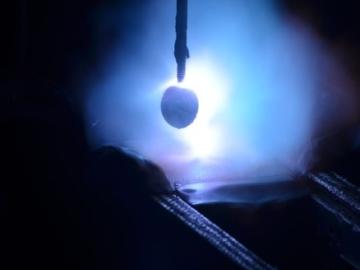
Researchers at Oak Ridge National Laboratory demonstrated that an additively manufactured polymer layer, when applied to carbon fiber reinforced plastic, or CFRP, can serve as an effective protector against aircraft lightning strikes.
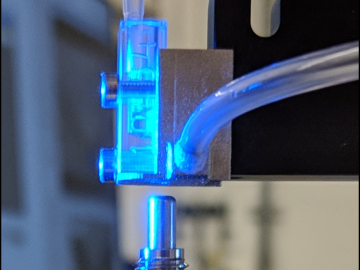
Researchers at the Department of Energy’s Oak Ridge National Laboratory have received five 2019 R&D 100 Awards, increasing the lab’s total to 221 since the award’s inception in 1963.
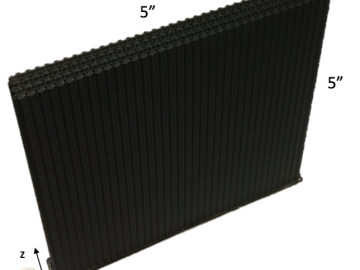
A team including Oak Ridge National Laboratory and University of Tennessee researchers demonstrated a novel 3D printing approach called Z-pinning that can increase the material’s strength and toughness by more than three and a half times compared to conventional additive manufacturing processes.
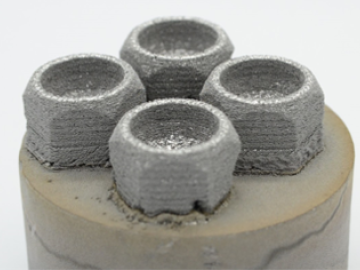
Using additive manufacturing, scientists experimenting with tungsten at Oak Ridge National Laboratory hope to unlock new potential of the high-performance heat-transferring material used to protect components from the plasma inside a fusion reactor. Fusion requires hydrogen isotopes to reach millions of degrees.
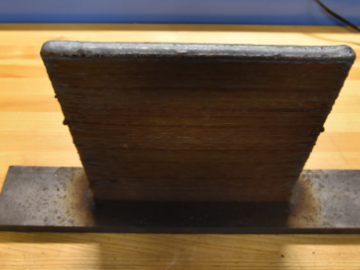
A novel additive manufacturing method developed by researchers at Oak Ridge National Laboratory could be a promising alternative for low-cost, high-quality production of large-scale metal parts with less material waste.
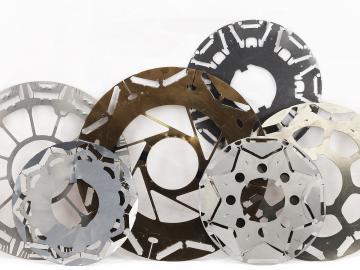
Oak Ridge National Laboratory scientists have created open source software that scales up analysis of motor designs to run on the fastest computers available, including those accessible to outside users at the Oak Ridge Leadership Computing Facility.