Filter News
Area of Research
- (-) Clean Energy (33)
- (-) Neutron Science (13)
- (-) Nuclear Science and Technology (6)
- Advanced Manufacturing (6)
- Biology and Environment (10)
- Building Technologies (1)
- Climate and Environmental Systems (1)
- Computational Engineering (2)
- Computer Science (9)
- Electricity and Smart Grid (1)
- Fusion Energy (3)
- Materials (10)
- Materials for Computing (4)
- Mathematics (1)
- National Security (1)
- Quantum information Science (3)
- Sensors and Controls (1)
- Supercomputing (9)
News Topics
- (-) Clean Water (4)
- (-) Composites (6)
- (-) Computer Science (8)
- (-) Grid (7)
- (-) Neutron Science (13)
- (-) Nuclear Energy (6)
- (-) Quantum Science (1)
- (-) Sustainable Energy (18)
- 3-D Printing/Advanced Manufacturing (17)
- Advanced Reactors (2)
- Artificial Intelligence (2)
- Big Data (1)
- Bioenergy (2)
- Biology (2)
- Biomedical (1)
- Biotechnology (1)
- Buildings (9)
- Climate Change (2)
- Coronavirus (1)
- Critical Materials (2)
- Decarbonization (2)
- Energy Storage (11)
- Environment (11)
- Fusion (1)
- High-Performance Computing (1)
- Hydropower (1)
- Materials (12)
- Materials Science (7)
- Mathematics (1)
- Microscopy (2)
- Nanotechnology (1)
- Net Zero (1)
- Physics (1)
- Polymers (3)
- Space Exploration (4)
- Statistics (1)
- Transportation (14)
Media Contacts
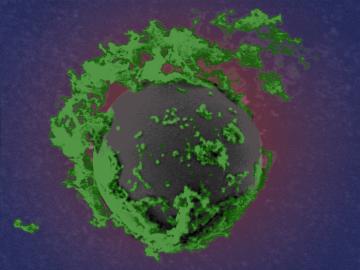
The presence of minerals called ash in plants makes little difference to the fitness of new naturally derived compound materials designed for additive manufacturing, an Oak Ridge National Laboratory-led team found.
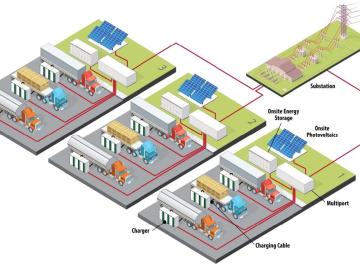
Researchers at Oak Ridge National Laboratory have designed architecture, software and control strategies for a futuristic EV truck stop that can draw megawatts of power and reduce carbon emissions.
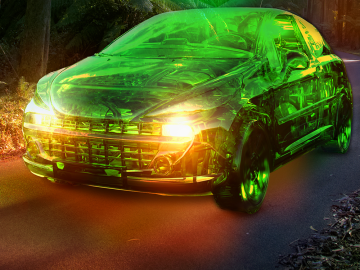
Oak Ridge National Laboratory scientists designed a recyclable polymer for carbon-fiber composites to enable circular manufacturing of parts that boost energy efficiency in automotive, wind power and aerospace applications.
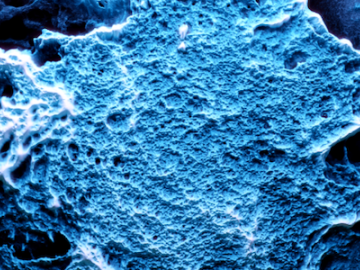
Neutron scattering techniques were used as part of a study of a novel nanoreactor material that grows crystalline hydrogen clathrates, or HCs, capable of storing hydrogen.

To further the potential benefits of the nation’s hydropower resources, researchers at Oak Ridge National Laboratory have developed and maintain a comprehensive water energy digital platform called HydroSource.
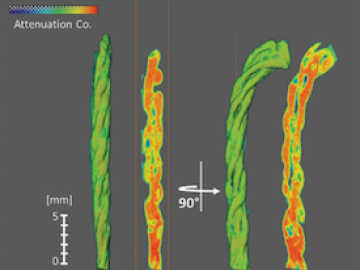
Textile engineering researchers from North Carolina State University used neutrons at Oak Ridge National Laboratory to identify a special wicking mechanism in a type of cotton yarn that allows the fibers to control the flow of liquid across certain strands.

Oak Ridge National Laboratory scientists worked with the Colorado School of Mines and Baylor University to develop and test control methods for autonomous water treatment plants that use less energy and generate less waste.
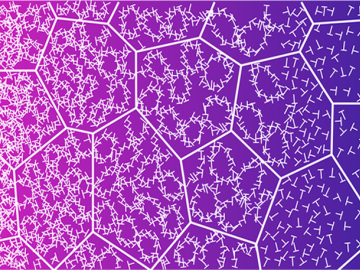
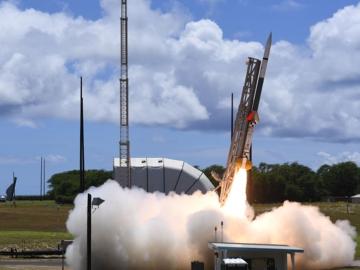
Oak Ridge National Laboratory researchers have developed a novel process to manufacture extreme heat resistant carbon-carbon composites. The performance of these materials will be tested in a U.S. Navy rocket that NASA will launch this fall.
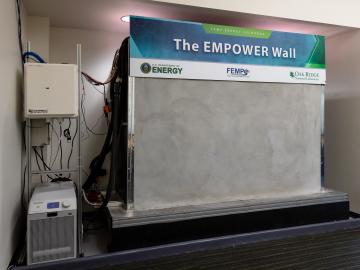
Oak Ridge National Laboratory researchers demonstrated that cooling cost savings could be achieved with a 3D printed concrete smart wall following a three-month field test.