Filter News
Area of Research
News Topics
- (-) 3-D Printing/Advanced Manufacturing (8)
- (-) Bioenergy (3)
- (-) Composites (2)
- (-) Microscopy (5)
- (-) Molten Salt (1)
- (-) Nuclear Energy (6)
- Advanced Reactors (1)
- Artificial Intelligence (1)
- Biomedical (1)
- Clean Water (2)
- Computer Science (3)
- Cybersecurity (1)
- Energy Storage (4)
- Environment (5)
- Fusion (2)
- Isotopes (1)
- Materials Science (19)
- Nanotechnology (6)
- Neutron Science (4)
- Physics (2)
- Polymers (2)
- Quantum Science (2)
- Sustainable Energy (5)
- Transportation (5)
Media Contacts
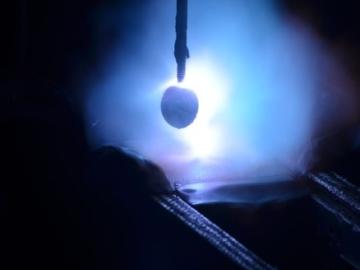
Researchers at Oak Ridge National Laboratory demonstrated that an additively manufactured polymer layer, when applied to carbon fiber reinforced plastic, or CFRP, can serve as an effective protector against aircraft lightning strikes.
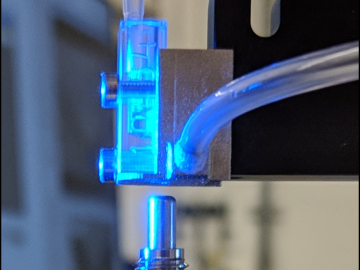
Researchers at the Department of Energy’s Oak Ridge National Laboratory have received five 2019 R&D 100 Awards, increasing the lab’s total to 221 since the award’s inception in 1963.

ORNL and The University of Toledo have entered into a memorandum of understanding for collaborative research.
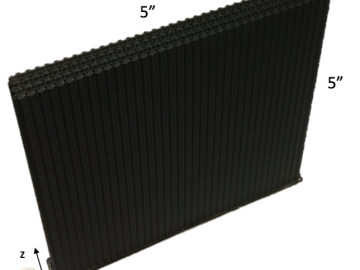
A team including Oak Ridge National Laboratory and University of Tennessee researchers demonstrated a novel 3D printing approach called Z-pinning that can increase the material’s strength and toughness by more than three and a half times compared to conventional additive manufacturing processes.
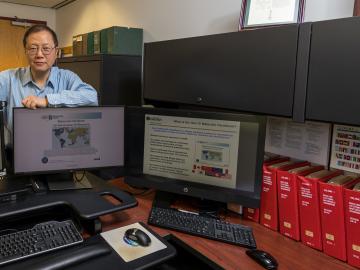
Six new nuclear reactor technologies are set to deploy for commercial use between 2030 and 2040. Called Generation IV nuclear reactors, they will operate with improved performance at dramatically higher temperatures than today’s reactors.
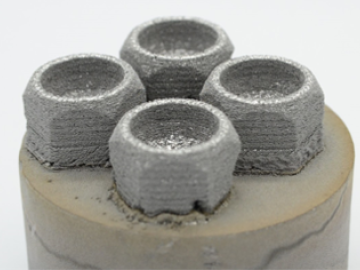
Using additive manufacturing, scientists experimenting with tungsten at Oak Ridge National Laboratory hope to unlock new potential of the high-performance heat-transferring material used to protect components from the plasma inside a fusion reactor. Fusion requires hydrogen isotopes to reach millions of degrees.
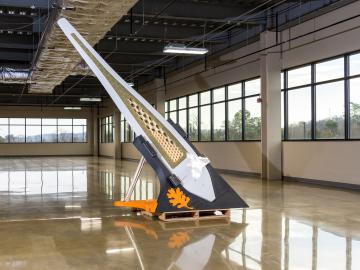
In the shifting landscape of global manufacturing, American ingenuity is once again giving U.S companies an edge with radical productivity improvements as a result of advanced materials and robotic systems developed at the Department of Energy’s Manufacturing Demonstration Facility (MDF) at Oak Ridge National Laboratory.
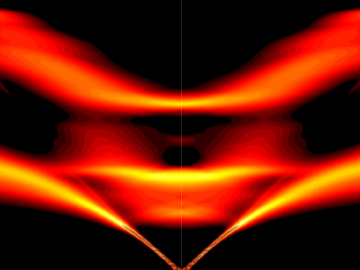
Scientists have discovered a way to alter heat transport in thermoelectric materials, a finding that may ultimately improve energy efficiency as the materials
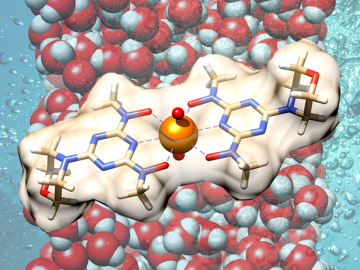
Scientists have demonstrated a new bio-inspired material for an eco-friendly and cost-effective approach to recovering uranium from seawater.
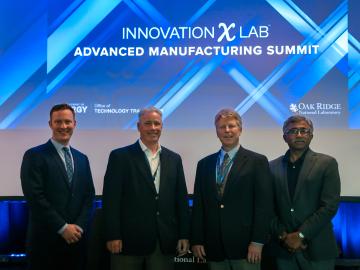
OAK RIDGE, Tenn., May 8, 2019—Oak Ridge National Laboratory and Lincoln Electric (NASDAQ: LECO) announced their continued collaboration on large-scale, robotic additive manufacturing technology at the Department of Energy’s Advanced Manufacturing InnovationXLab Summit.