Filter News
Area of Research
News Topics
- (-) 3-D Printing/Advanced Manufacturing (8)
- (-) Biomedical (2)
- (-) Composites (2)
- (-) Grid (1)
- (-) Materials Science (19)
- (-) Quantum Science (5)
- Advanced Reactors (2)
- Artificial Intelligence (6)
- Big Data (4)
- Bioenergy (3)
- Clean Water (2)
- Computer Science (24)
- Cybersecurity (2)
- Energy Storage (5)
- Environment (6)
- Exascale Computing (2)
- Frontier (2)
- Fusion (2)
- Isotopes (1)
- Microscopy (5)
- Molten Salt (1)
- Nanotechnology (6)
- Neutron Science (5)
- Nuclear Energy (8)
- Physics (3)
- Polymers (2)
- Security (1)
- Space Exploration (2)
- Summit (9)
- Sustainable Energy (6)
- Transportation (6)
Media Contacts

Oak Ridge National Laboratory has teamed with Cornell College and the University of Tennessee to study ways to repurpose waste soft drinks for carbon capture that could help cut carbon dioxide emissions.
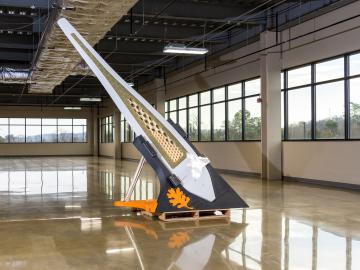
In the shifting landscape of global manufacturing, American ingenuity is once again giving U.S companies an edge with radical productivity improvements as a result of advanced materials and robotic systems developed at the Department of Energy’s Manufacturing Demonstration Facility (MDF) at Oak Ridge National Laboratory.
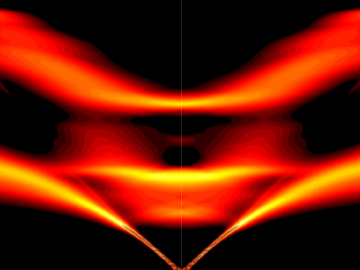
Scientists have discovered a way to alter heat transport in thermoelectric materials, a finding that may ultimately improve energy efficiency as the materials
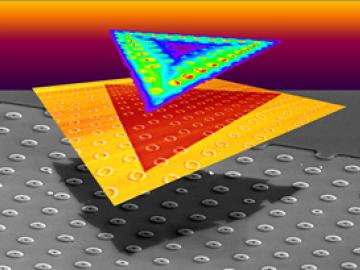
A team led by scientists at the Department of Energy’s Oak Ridge National Laboratory explored how atomically thin two-dimensional (2D) crystals can grow over 3D objects and how the curvature of those objects can stretch and strain the
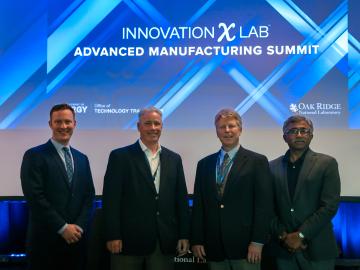
OAK RIDGE, Tenn., May 8, 2019—Oak Ridge National Laboratory and Lincoln Electric (NASDAQ: LECO) announced their continued collaboration on large-scale, robotic additive manufacturing technology at the Department of Energy’s Advanced Manufacturing InnovationXLab Summit.
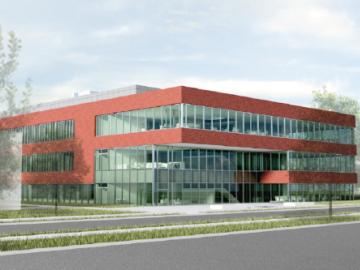
OAK RIDGE, Tenn., May 7, 2019—Energy Secretary Rick Perry, Congressman Chuck Fleischmann and lab officials today broke ground on a multipurpose research facility that will provide state-of-the-art laboratory space
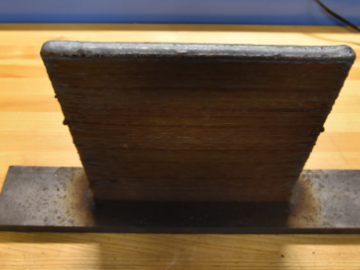
A novel additive manufacturing method developed by researchers at Oak Ridge National Laboratory could be a promising alternative for low-cost, high-quality production of large-scale metal parts with less material waste.
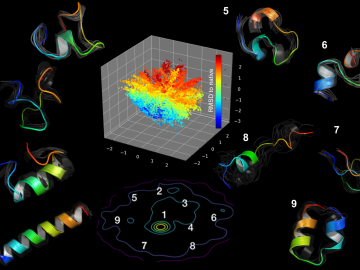
Using artificial neural networks designed to emulate the inner workings of the human brain, deep-learning algorithms deftly peruse and analyze large quantities of data. Applying this technique to science problems can help unearth historically elusive solutions.
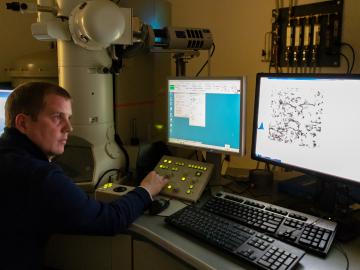
Kevin Field at the Department of Energy’s Oak Ridge National Laboratory synthesizes and scrutinizes materials for nuclear power systems that must perform safely and efficiently over decades of irradiation.
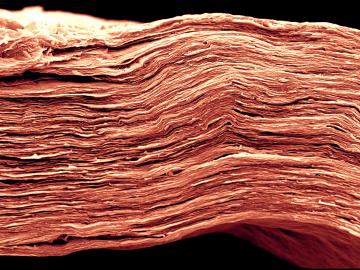