Filter News
Area of Research
News Topics
- (-) Big Data (7)
- (-) Biomedical (1)
- (-) Composites (4)
- (-) High-Performance Computing (5)
- (-) Materials Science (16)
- (-) Nanotechnology (4)
- 3-D Printing/Advanced Manufacturing (18)
- Advanced Reactors (6)
- Artificial Intelligence (6)
- Bioenergy (3)
- Biology (4)
- Biotechnology (1)
- Buildings (4)
- Chemical Sciences (1)
- Clean Water (7)
- Climate Change (7)
- Computer Science (22)
- Coronavirus (3)
- Critical Materials (2)
- Cybersecurity (2)
- Decarbonization (1)
- Energy Storage (9)
- Environment (19)
- Fusion (5)
- Grid (8)
- Isotopes (2)
- ITER (2)
- Machine Learning (3)
- Materials (17)
- Mathematics (1)
- Microscopy (5)
- Molten Salt (1)
- Net Zero (1)
- Neutron Science (12)
- Nuclear Energy (9)
- Physics (2)
- Polymers (2)
- Quantum Computing (1)
- Quantum Science (6)
- Space Exploration (6)
- Statistics (1)
- Summit (2)
- Sustainable Energy (22)
- Transportation (15)
Media Contacts

A new modeling capability developed at Oak Ridge National Laboratory incorporates important biogeochemical processes happening in river corridors for a clearer understanding of how water quality will be impacted by climate change, land use and
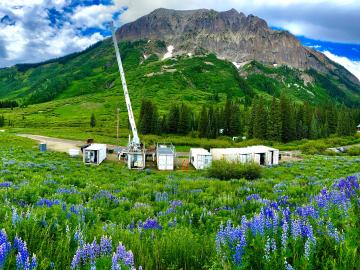
New data hosted through the Atmospheric Radiation Measurement Data Center at Oak Ridge National Laboratory will help improve models that predict climate change effects on the water supply in the Colorado River Basin.

Oak Ridge National Laboratory, University of Tennessee and University of Central Florida researchers released a new high-performance computing code designed to more efficiently examine power systems and identify electrical grid disruptions, such as
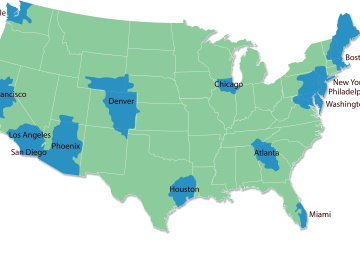
Oak Ridge National Laboratory worked with Colorado State University to simulate how a warming climate may affect U.S. urban hydrological systems.

A research team at Oak Ridge National Laboratory have 3D printed a thermal protection shield, or TPS, for a capsule that will launch with the Cygnus cargo spacecraft as part of the supply mission to the International Space Station.
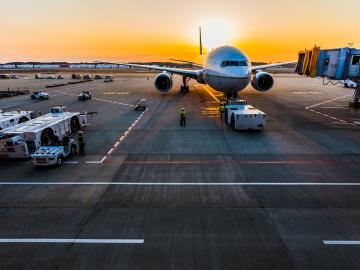
Oak Ridge National Laboratory researchers have developed a new catalyst for converting ethanol into C3+ olefins – the chemical
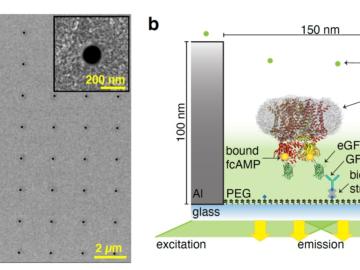
Researchers working with Oak Ridge National Laboratory developed a new method to observe how proteins, at the single-molecule level, bind with other molecules and more accurately pinpoint certain molecular behavior in complex
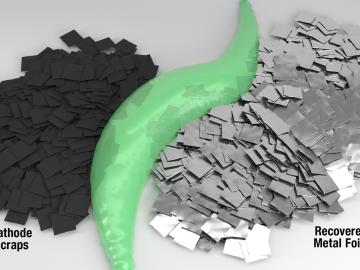
Scientists at Oak Ridge National Laboratory have developed a solvent that results in a more environmentally friendly process to recover valuable materials from used lithium-ion batteries, supports a stable domestic supply chain for new batteries
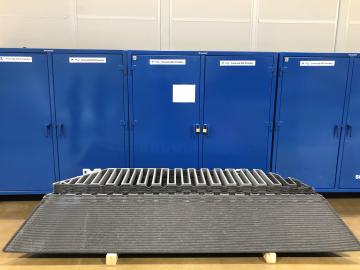
Oak Ridge National Laboratory researchers, in collaboration with Cincinnati Inc., demonstrated the potential for using multimaterials and recycled composites in large-scale applications by 3D printing a mold that replicated a single facet of a
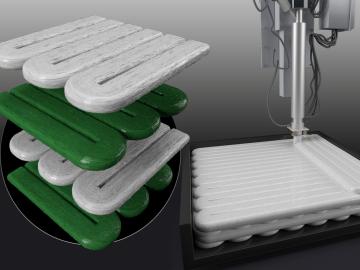
Oak Ridge National Laboratory researchers combined additive manufacturing with conventional compression molding to produce high-performance thermoplastic composites reinforced with short carbon fibers.