
Filter News
Area of Research
- (-) Advanced Manufacturing (9)
- (-) Materials (35)
- (-) Nuclear Science and Technology (2)
- Biology and Environment (10)
- Building Technologies (1)
- Clean Energy (58)
- Computational Engineering (1)
- Computer Science (5)
- Electricity and Smart Grid (1)
- Functional Materials for Energy (1)
- Fusion and Fission (2)
- Fusion Energy (1)
- Isotopes (2)
- Materials for Computing (2)
- National Security (15)
- Neutron Science (6)
- Quantum information Science (3)
- Sensors and Controls (1)
- Supercomputing (24)
- Transportation Systems (1)
News Topics
- (-) 3-D Printing/Advanced Manufacturing (18)
- (-) Cybersecurity (2)
- (-) Grid (3)
- (-) Isotopes (8)
- (-) Quantum Science (4)
- (-) Security (1)
- (-) Transportation (8)
- Advanced Reactors (6)
- Artificial Intelligence (6)
- Bioenergy (6)
- Biology (3)
- Biomedical (5)
- Buildings (2)
- Chemical Sciences (11)
- Clean Water (3)
- Composites (6)
- Computer Science (7)
- Coronavirus (2)
- Critical Materials (3)
- Decarbonization (3)
- Energy Storage (18)
- Environment (9)
- Exascale Computing (1)
- Frontier (2)
- Fusion (5)
- High-Performance Computing (4)
- Machine Learning (2)
- Materials (25)
- Materials Science (35)
- Microscopy (13)
- Molten Salt (4)
- Nanotechnology (18)
- National Security (2)
- Neutron Science (12)
- Nuclear Energy (20)
- Partnerships (4)
- Physics (11)
- Polymers (8)
- Simulation (1)
- Space Exploration (3)
- Sustainable Energy (7)
- Transformational Challenge Reactor (1)
Media Contacts
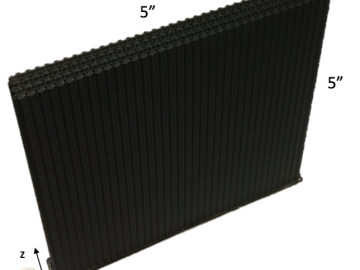
A team including Oak Ridge National Laboratory and University of Tennessee researchers demonstrated a novel 3D printing approach called Z-pinning that can increase the material’s strength and toughness by more than three and a half times compared to conventional additive manufacturing processes.
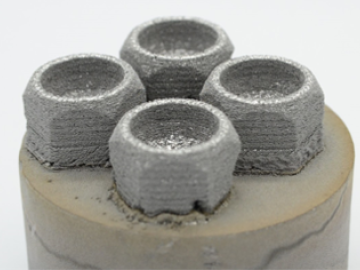
Using additive manufacturing, scientists experimenting with tungsten at Oak Ridge National Laboratory hope to unlock new potential of the high-performance heat-transferring material used to protect components from the plasma inside a fusion reactor. Fusion requires hydrogen isotopes to reach millions of degrees.

A team of researchers at Oak Ridge National Laboratory have demonstrated that designed synthetic polymers can serve as a high-performance binding material for next-generation lithium-ion batteries.
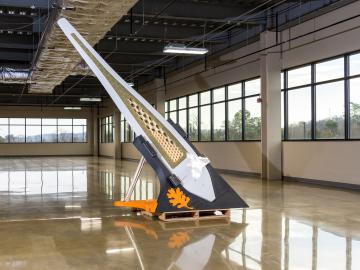
In the shifting landscape of global manufacturing, American ingenuity is once again giving U.S companies an edge with radical productivity improvements as a result of advanced materials and robotic systems developed at the Department of Energy’s Manufacturing Demonstration Facility (MDF) at Oak Ridge National Laboratory.
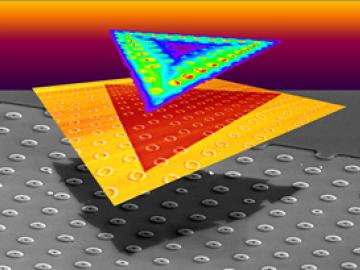
A team led by scientists at the Department of Energy’s Oak Ridge National Laboratory explored how atomically thin two-dimensional (2D) crystals can grow over 3D objects and how the curvature of those objects can stretch and strain the
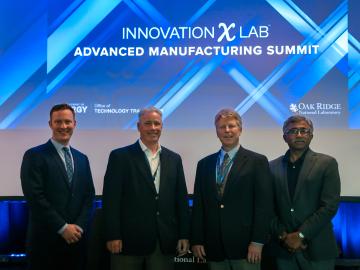
OAK RIDGE, Tenn., May 8, 2019—Oak Ridge National Laboratory and Lincoln Electric (NASDAQ: LECO) announced their continued collaboration on large-scale, robotic additive manufacturing technology at the Department of Energy’s Advanced Manufacturing InnovationXLab Summit.
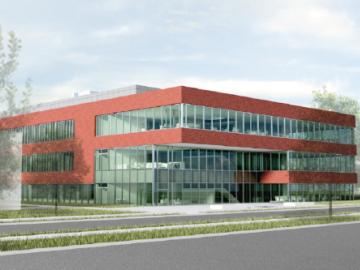
OAK RIDGE, Tenn., May 7, 2019—Energy Secretary Rick Perry, Congressman Chuck Fleischmann and lab officials today broke ground on a multipurpose research facility that will provide state-of-the-art laboratory space
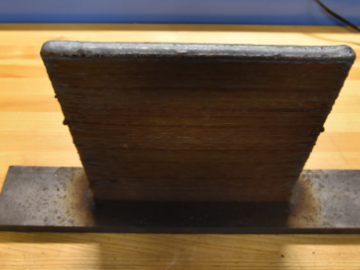
A novel additive manufacturing method developed by researchers at Oak Ridge National Laboratory could be a promising alternative for low-cost, high-quality production of large-scale metal parts with less material waste.
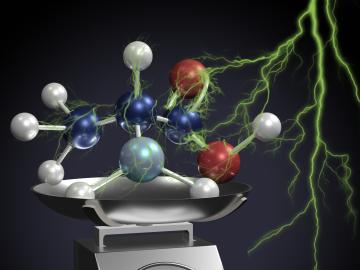
OAK RIDGE, Tenn., Jan. 31, 2019—A new electron microscopy technique that detects the subtle changes in the weight of proteins at the nanoscale—while keeping the sample intact—could open a new pathway for deeper, more comprehensive studies of the basic building blocks of life.
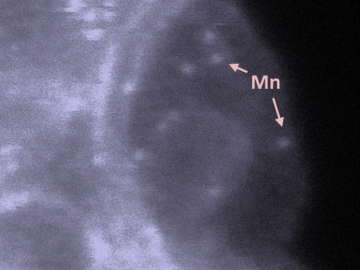
Oak Ridge National Laboratory scientists studying fuel cells as a potential alternative to internal combustion engines used sophisticated electron microscopy to investigate the benefits of replacing high-cost platinum with a lower cost, carbon-nitrogen-manganese-based catalyst.