Filter News
Area of Research
- (-) Materials (15)
- (-) National Security (5)
- (-) Neutron Science (6)
- (-) Nuclear Science and Technology (10)
- Advanced Manufacturing (1)
- Biology and Environment (2)
- Clean Energy (36)
- Computer Science (1)
- Fusion and Fission (2)
- Fusion Energy (4)
- Materials for Computing (4)
- Nuclear Systems Modeling, Simulation and Validation (1)
- Quantum information Science (1)
- Sensors and Controls (1)
- Supercomputing (8)
News Topics
- (-) Advanced Reactors (8)
- (-) Polymers (8)
- (-) Security (4)
- (-) Sustainable Energy (7)
- (-) Transformational Challenge Reactor (4)
- (-) Transportation (7)
- 3-D Printing/Advanced Manufacturing (10)
- Artificial Intelligence (3)
- Big Data (3)
- Bioenergy (7)
- Biomedical (10)
- Chemical Sciences (2)
- Climate Change (1)
- Composites (2)
- Computer Science (16)
- Coronavirus (7)
- Critical Materials (2)
- Cybersecurity (3)
- Decarbonization (1)
- Energy Storage (10)
- Environment (6)
- Exascale Computing (1)
- Fusion (7)
- Grid (2)
- Isotopes (9)
- Machine Learning (3)
- Materials (1)
- Materials Science (38)
- Mathematics (1)
- Microscopy (9)
- Molten Salt (5)
- Nanotechnology (20)
- National Security (2)
- Neutron Science (33)
- Nuclear Energy (25)
- Physics (13)
- Quantum Science (5)
- Space Exploration (3)
- Summit (6)
Media Contacts
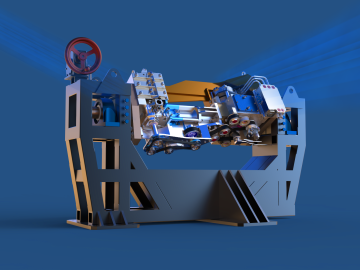
In the quest for advanced vehicles with higher energy efficiency and ultra-low emissions, ORNL researchers are accelerating a research engine that gives scientists and engineers an unprecedented view inside the atomic-level workings of combustion engines in real time.
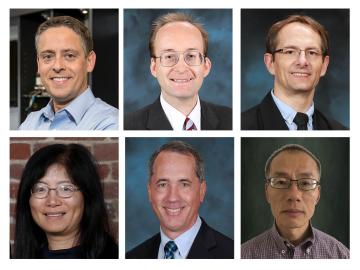
Six scientists at the Department of Energy’s Oak Ridge National Laboratory were named Battelle Distinguished Inventors, in recognition of obtaining 14 or more patents during their careers at the lab.
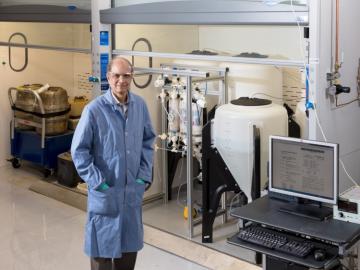
Momentum Technologies Inc., a Dallas, Texas-based materials science company that is focused on extracting critical metals from electronic waste, has licensed an Oak Ridge National Laboratory process for recovering cobalt and other metals from spent
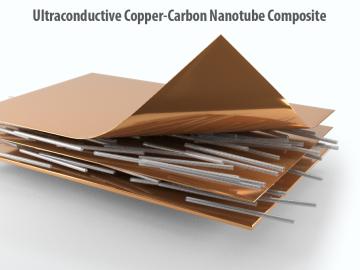
Scientists at Oak Ridge National Laboratory used new techniques to create a composite that increases the electrical current capacity of copper wires, providing a new material that can be scaled for use in ultra-efficient, power-dense electric vehicle traction motors.
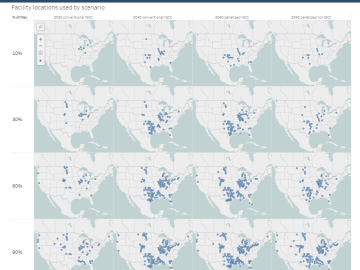
The combination of bioenergy with carbon capture and storage could cost-effectively sequester hundreds of millions of metric tons per year of carbon dioxide in the United States, making it a competitive solution for carbon management, according to a new analysis by ORNL scientists.
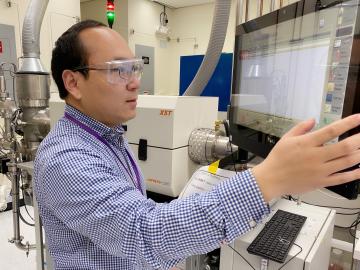
About 60 years ago, scientists discovered that a certain rare earth metal-hydrogen mixture, yttrium, could be the ideal moderator to go inside small, gas-cooled nuclear reactors.
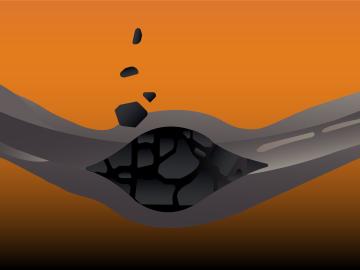
A developing method to gauge the occurrence of a nuclear reactor anomaly has the potential to save millions of dollars.
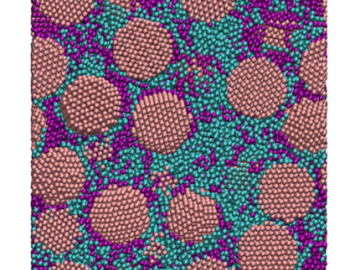
Oak Ridge National Laboratory scientists have discovered a cost-effective way to significantly improve the mechanical performance of common polymer nanocomposite materials.
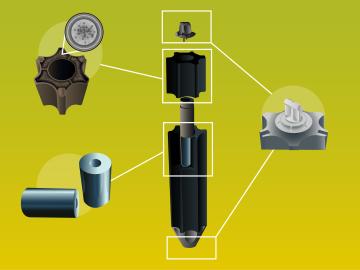
It’s a new type of nuclear reactor core. And the materials that will make it up are novel — products of Oak Ridge National Laboratory’s advanced materials and manufacturing technologies.
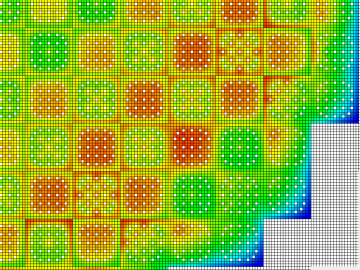
As CASL ends and transitions to VERA Users Group, ORNL looks at the history of the program and its impact on the nuclear industry.