Filter News
Area of Research
News Topics
- (-) 3-D Printing/Advanced Manufacturing (11)
- (-) Computer Science (5)
- Advanced Reactors (1)
- Biomedical (1)
- Buildings (4)
- Chemical Sciences (3)
- Clean Water (2)
- Composites (2)
- Critical Materials (3)
- Decarbonization (2)
- Energy Storage (6)
- Environment (8)
- Fusion (2)
- Grid (5)
- Hydropower (1)
- Isotopes (1)
- Materials (4)
- Materials Science (13)
- Mercury (1)
- Microscopy (3)
- Molten Salt (1)
- Nanotechnology (5)
- Neutron Science (4)
- Nuclear Energy (4)
- Physics (2)
- Polymers (3)
- Quantum Computing (1)
- Simulation (1)
- Space Exploration (2)
- Sustainable Energy (4)
- Transportation (13)
Media Contacts
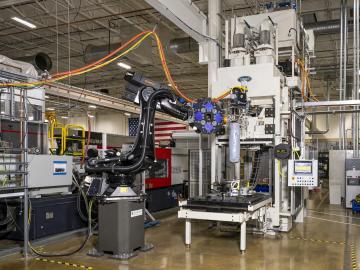
An Oak Ridge National Laboratory-developed advanced manufacturing technology, AMCM, was recently licensed by Orbital Composites and enables the rapid production of composite-based components, which could accelerate the decarbonization of vehicles

Oak Ridge National Laboratory researchers have conducted a comprehensive life cycle, cost and carbon emissions analysis on 3D-printed molds for precast concrete and determined the method is economically beneficial compared to conventional wood molds.

A new report published by ORNL assessed how advanced manufacturing and materials, such as 3D printing and novel component coatings, could offer solutions to modernize the existing fleet and design new approaches to hydropower.

Critical Materials Institute researchers at Oak Ridge National Laboratory and Arizona State University studied the mineral monazite, an important source of rare-earth elements, to enhance methods of recovering critical materials for energy, defense and manufacturing applications.

ORNL researchers have identified a mechanism in a 3D-printed alloy – termed “load shuffling” — that could enable the design of better-performing lightweight materials for vehicles.
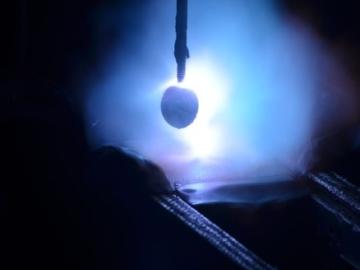
Researchers at Oak Ridge National Laboratory demonstrated that an additively manufactured polymer layer, when applied to carbon fiber reinforced plastic, or CFRP, can serve as an effective protector against aircraft lightning strikes.
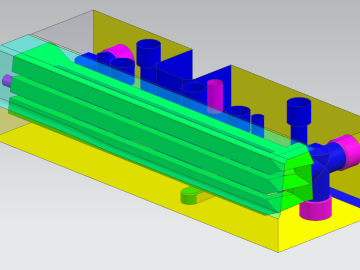
Researchers demonstrated that an additively manufactured hot stamping die can withstand up to 25,000 usage cycles, proving that this technique is a viable solution for production.
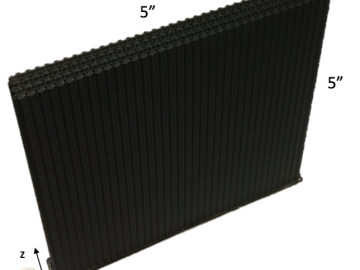
A team including Oak Ridge National Laboratory and University of Tennessee researchers demonstrated a novel 3D printing approach called Z-pinning that can increase the material’s strength and toughness by more than three and a half times compared to conventional additive manufacturing processes.
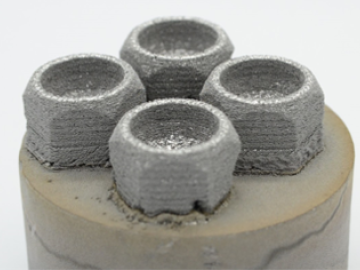
Using additive manufacturing, scientists experimenting with tungsten at Oak Ridge National Laboratory hope to unlock new potential of the high-performance heat-transferring material used to protect components from the plasma inside a fusion reactor. Fusion requires hydrogen isotopes to reach millions of degrees.

A detailed study by Oak Ridge National Laboratory estimated how much more—or less—energy United States residents might consume by 2050 relative to predicted shifts in seasonal weather patterns