Filter News
Area of Research
- Advanced Manufacturing (5)
- Biology and Environment (8)
- Clean Energy (57)
- Computer Science (1)
- Electricity and Smart Grid (1)
- Fusion and Fission (4)
- Fusion Energy (3)
- Isotope Development and Production (1)
- Isotopes (1)
- Materials (28)
- Materials for Computing (2)
- National Security (13)
- Neutron Science (10)
- Nuclear Science and Technology (10)
- Nuclear Systems Modeling, Simulation and Validation (1)
- Quantum information Science (3)
- Supercomputing (21)
News Topics
- (-) 3-D Printing/Advanced Manufacturing (49)
- (-) Advanced Reactors (17)
- (-) Composites (8)
- (-) Cybersecurity (15)
- (-) Grid (23)
- (-) Irradiation (2)
- (-) Nanotechnology (24)
- (-) Quantum Science (23)
- Artificial Intelligence (35)
- Big Data (23)
- Bioenergy (36)
- Biology (35)
- Biomedical (28)
- Biotechnology (8)
- Buildings (15)
- Chemical Sciences (29)
- Clean Water (7)
- Climate Change (41)
- Computer Science (68)
- Coronavirus (27)
- Critical Materials (8)
- Decarbonization (31)
- Education (3)
- Emergency (1)
- Energy Storage (43)
- Environment (76)
- Exascale Computing (19)
- Fossil Energy (2)
- Frontier (20)
- Fusion (23)
- High-Performance Computing (36)
- Hydropower (3)
- Isotopes (19)
- Machine Learning (23)
- Materials (61)
- Materials Science (55)
- Mathematics (4)
- Mercury (4)
- Microelectronics (2)
- Microscopy (16)
- Molten Salt (3)
- National Security (23)
- Net Zero (5)
- Neutron Science (64)
- Nuclear Energy (52)
- Partnerships (24)
- Physics (29)
- Polymers (11)
- Quantum Computing (12)
- Renewable Energy (2)
- Security (6)
- Simulation (29)
- Software (1)
- Space Exploration (6)
- Summit (26)
- Sustainable Energy (41)
- Transformational Challenge Reactor (5)
- Transportation (35)
Media Contacts
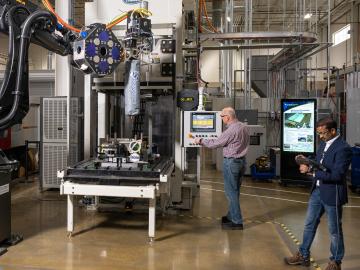
Researchers at ORNL are extending the boundaries of composite-based materials used in additive manufacturing, or AM. ORNL is working with industrial partners who are exploring AM, also known as 3D printing, as a path to higher production levels and fewer supply chain interruptions.

In fiscal year 2023 — Oct. 1–Sept. 30, 2023 — Oak Ridge National Laboratory was awarded more than $8 million in technology maturation funding through the Department of Energy’s Technology Commercialization Fund, or TCF.

As vehicles gain technological capabilities, car manufacturers are using an increasing number of computers and sensors to improve situational awareness and enhance the driving experience.
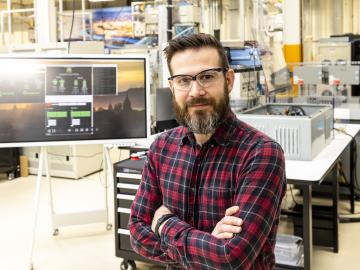
Steven Campbell can often be found deep among tall cases of power electronics, hunkered in his oversized blue lab coat, with 1500 volts of electricity flowing above his head. When interrupted in his laboratory at ORNL, Campbell will usually smile and duck his head.
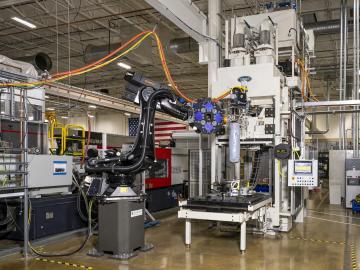
An Oak Ridge National Laboratory-developed advanced manufacturing technology, AMCM, was recently licensed by Orbital Composites and enables the rapid production of composite-based components, which could accelerate the decarbonization of vehicles
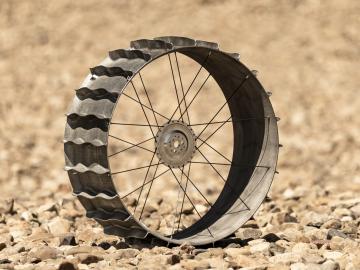
Researchers at the Department of Energy’s Oak Ridge National Laboratory, in collaboration with NASA, are taking additive manufacturing to the final frontier by 3D printing the same kind of wheel as the design used by NASA for its robotic lunar rover, demonstrating the technology for specialized parts needed for space exploration.
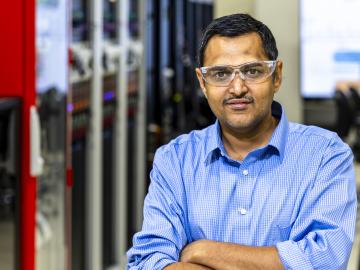
Sreenivasa Jaldanki, a researcher in the Grid Systems Modeling and Controls group at the Department of Energy’s Oak Ridge National Laboratory, was recently elevated to senior membership in the Institute of Electrical and Electronics Engineers, or IEEE.
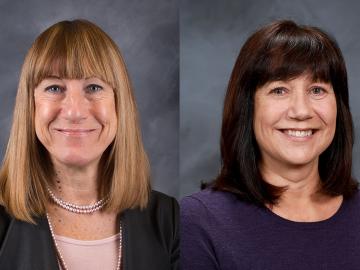
ORNL’s Fulvia Pilat and Karren More recently participated in the inaugural 2023 Nanotechnology Infrastructure Leaders Summit and Workshop at the White House.
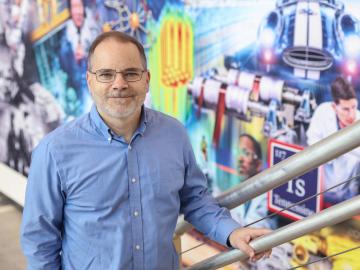
ORNL has been selected to lead an Energy Earthshot Research Center, or EERC, focused on developing chemical processes that use sustainable methods instead of burning fossil fuels to radically reduce industrial greenhouse gas emissions to stem climate change and limit the crisis of a rapidly warming planet.

Oak Ridge National Laboratory researchers have conducted a comprehensive life cycle, cost and carbon emissions analysis on 3D-printed molds for precast concrete and determined the method is economically beneficial compared to conventional wood molds.