
Filter News
Area of Research
News Topics
- (-) Advanced Reactors (6)
- (-) Climate Change (5)
- (-) Composites (1)
- (-) Coronavirus (3)
- (-) Cybersecurity (1)
- (-) Fusion (3)
- 3-D Printing/Advanced Manufacturing (2)
- Artificial Intelligence (2)
- Big Data (3)
- Biology (2)
- Biomedical (6)
- Computer Science (8)
- Energy Storage (7)
- Environment (8)
- Frontier (1)
- Grid (3)
- Isotopes (1)
- Machine Learning (3)
- Materials Science (8)
- Microscopy (2)
- Molten Salt (1)
- Nanotechnology (2)
- Neutron Science (4)
- Nuclear Energy (6)
- Polymers (2)
- Summit (3)
- Sustainable Energy (8)
- Transportation (5)
Media Contacts
An international team of scientists found that rules governing plant growth hold true even at the edges of the world in the Arctic tundra.
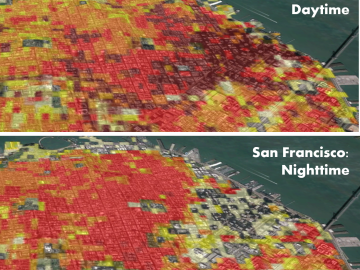
Oak Ridge National Laboratory’s high-resolution population distribution database, LandScan USA, became permanently available to researchers in time to aid the response to the novel coronavirus pandemic.
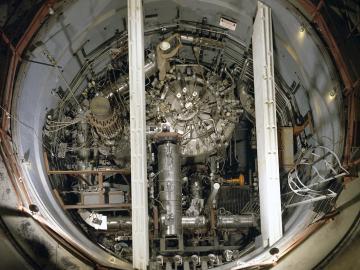
In the 1960s, Oak Ridge National Laboratory's four-year Molten Salt Reactor Experiment tested the viability of liquid fuel reactors for commercial power generation. Results from that historic experiment recently became the basis for the first-ever molten salt reactor benchmark.
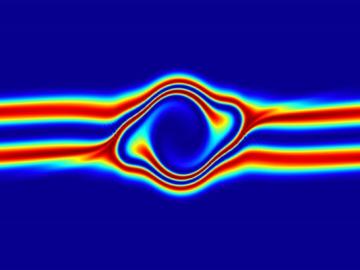
The prospect of simulating a fusion plasma is a step closer to reality thanks to a new computational tool developed by scientists in fusion physics, computer science and mathematics at ORNL.
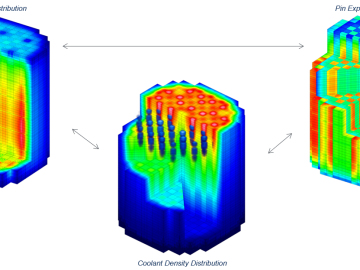
Nuclear scientists at Oak Ridge National Laboratory have established a Nuclear Quality Assurance-1 program for a software product designed to simulate today’s commercial nuclear reactors – removing a significant barrier for industry adoption of the technology.
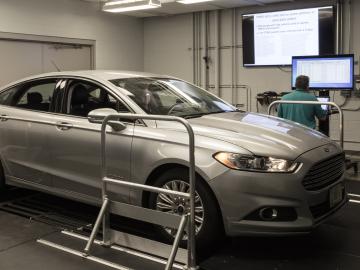
A new Oak Ridge National Laboratory-developed method promises to protect connected and autonomous vehicles from possible network intrusion. Researchers built a prototype plug-in device designed to alert drivers of vehicle cyberattacks. The prototype is coded to learn regular timing...
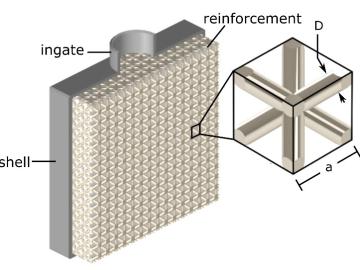
A new manufacturing method created by Oak Ridge National Laboratory and Rice University combines 3D printing with traditional casting to produce damage-tolerant components composed of multiple materials. Composite components made by pouring an aluminum alloy over a printed steel lattice showed an order of magnitude greater damage tolerance than aluminum alone.