Filter News
Area of Research
News Type
News Topics
- (-) Computer Science (6)
- (-) Microscopy (6)
- (-) Nanotechnology (6)
- (-) Neutron Science (4)
- (-) Polymers (3)
- (-) Security (1)
- (-) Transportation (2)
- 3-D Printing/Advanced Manufacturing (5)
- Advanced Reactors (1)
- Artificial Intelligence (2)
- Big Data (2)
- Bioenergy (2)
- Biomedical (2)
- Chemical Sciences (2)
- Clean Water (1)
- Composites (2)
- Coronavirus (2)
- Critical Materials (2)
- Cybersecurity (1)
- Decarbonization (1)
- Energy Storage (7)
- Environment (2)
- Exascale Computing (1)
- Grid (1)
- High-Performance Computing (1)
- Isotopes (2)
- Machine Learning (2)
- Materials (12)
- Materials Science (18)
- Mathematics (1)
- Nuclear Energy (3)
- Physics (5)
- Quantum Science (1)
- Summit (1)
- Sustainable Energy (2)
- Transformational Challenge Reactor (2)
Media Contacts
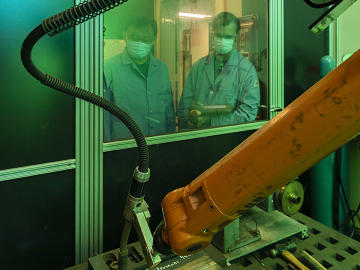
The U.S. Departments of Energy and Defense teamed up to create a series of weld filler materials that could dramatically improve high-strength steel repair in vehicles, bridges and pipelines.

Oak Ridge National Laboratory researchers serendipitously discovered when they automated the beam of an electron microscope to precisely drill holes in the atomically thin lattice of graphene, the drilled holes closed up.
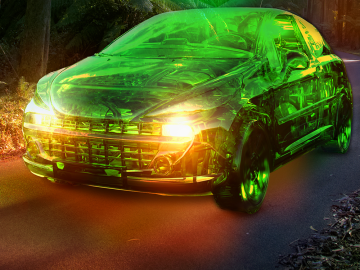
Oak Ridge National Laboratory scientists designed a recyclable polymer for carbon-fiber composites to enable circular manufacturing of parts that boost energy efficiency in automotive, wind power and aerospace applications.
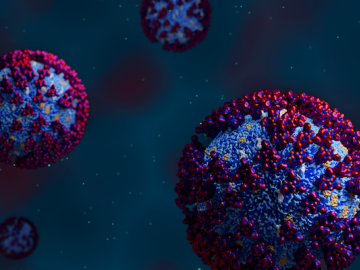
Researchers from ORNL, the University of Tennessee at Chattanooga and Tuskegee University used mathematics to predict which areas of the SARS-CoV-2 spike protein are most likely to mutate.

Larry Allard, a distinguished research staff member at Oak Ridge National Laboratory, has been named a Fellow of the Microanalysis Society.

A study led by researchers at ORNL could help make materials design as customizable as point-and-click.
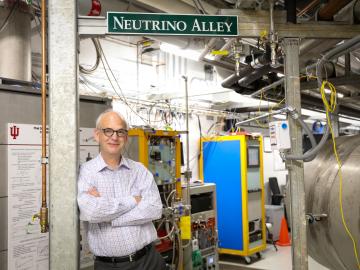
Marcel Demarteau is director of the Physics Division at the Department of Energy’s Oak Ridge National Laboratory. For topics from nuclear structure to astrophysics, he shapes ORNL’s physics research agenda.
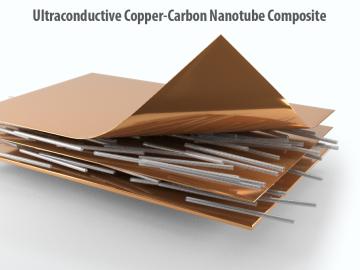
Scientists at Oak Ridge National Laboratory used new techniques to create a composite that increases the electrical current capacity of copper wires, providing a new material that can be scaled for use in ultra-efficient, power-dense electric vehicle traction motors.
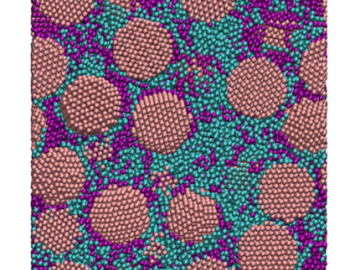
Oak Ridge National Laboratory scientists have discovered a cost-effective way to significantly improve the mechanical performance of common polymer nanocomposite materials.
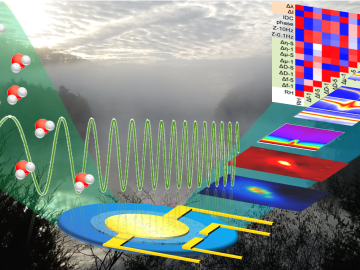
An all-in-one experimental platform developed at Oak Ridge National Laboratory’s Center for Nanophase Materials Sciences accelerates research on promising materials for future technologies.