Filter News
Area of Research
- (-) Clean Energy (26)
- (-) Computer Science (4)
- (-) Nuclear Science and Technology (1)
- Advanced Manufacturing (6)
- Biology and Environment (4)
- Building Technologies (1)
- Computational Engineering (2)
- Isotopes (8)
- Materials (4)
- Materials for Computing (4)
- Mathematics (1)
- National Security (3)
- Neutron Science (4)
- Quantum information Science (1)
- Supercomputing (9)
News Type
News Topics
- (-) 3-D Printing/Advanced Manufacturing (22)
- (-) Clean Water (1)
- (-) Composites (6)
- (-) Computer Science (6)
- (-) Physics (1)
- (-) Space Exploration (1)
- Artificial Intelligence (1)
- Big Data (3)
- Bioenergy (2)
- Biology (4)
- Biotechnology (1)
- Buildings (10)
- Chemical Sciences (1)
- Climate Change (3)
- Coronavirus (2)
- Critical Materials (3)
- Decarbonization (4)
- Energy Storage (17)
- Environment (9)
- Grid (9)
- High-Performance Computing (3)
- Materials (15)
- Materials Science (6)
- Mathematics (1)
- Mercury (1)
- Microscopy (1)
- Nanotechnology (1)
- Net Zero (1)
- Neutron Science (3)
- Polymers (3)
- Quantum Science (2)
- Statistics (1)
- Sustainable Energy (22)
- Transportation (15)
Media Contacts
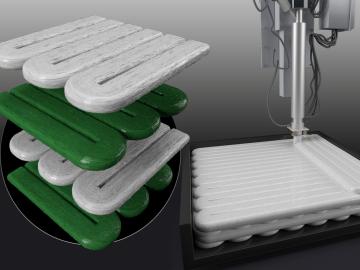
Oak Ridge National Laboratory researchers combined additive manufacturing with conventional compression molding to produce high-performance thermoplastic composites reinforced with short carbon fibers.

Xin Sun has been selected as the associate laboratory director for the Energy Science and Technology Directorate, or ESTD, at the Department of Energy’s Oak Ridge National Laboratory.

A team of Oak Ridge National Laboratory researchers demonstrated that an additively manufactured hot stamping die – a tool used to create car body components – cooled faster than those produced by conventional manufacturing methods.

Oak Ridge National Laboratory researchers have demonstrated that a new class of superalloys made of cobalt and nickel remains crack-free and defect-resistant in extreme heat, making them conducive for use in metal-based 3D printing applications.
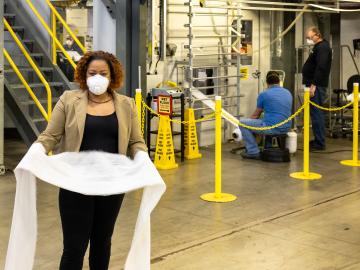
Three technologies developed by ORNL researchers have won National Technology Transfer Awards from the Federal Laboratory Consortium. One of the awards went to a team that adapted melt-blowing capabilities at DOE’s Carbon Fiber Technology Facility to enable the production of filter material for N95 masks in the fight against COVID-19.
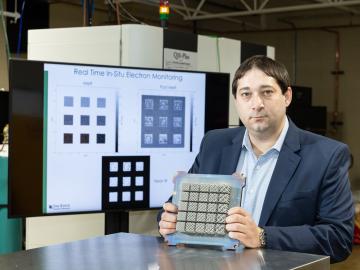
Growing up in the heart of the American automobile industry near Detroit, Oak Ridge National Laboratory materials scientist Mike Kirka was no stranger to manufacturing.
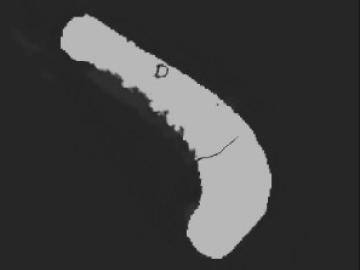
Algorithms developed at Oak Ridge National Laboratory can greatly enhance X-ray computed tomography images of 3D-printed metal parts, resulting in more accurate, faster scans.
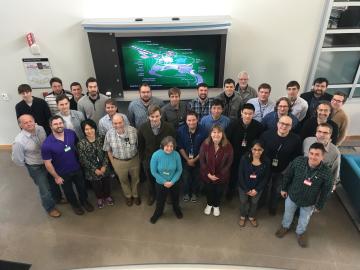
After more than a year of operation at the Department of Energy’s (DOE’s) Oak Ridge National Laboratory (ORNL), the COHERENT experiment, using the world’s smallest neutrino detector, has found a big fingerprint of the elusive, electrically neutral particles that interact only weakly with matter.
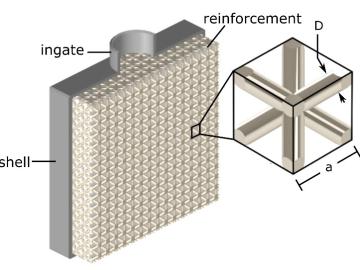
A new manufacturing method created by Oak Ridge National Laboratory and Rice University combines 3D printing with traditional casting to produce damage-tolerant components composed of multiple materials. Composite components made by pouring an aluminum alloy over a printed steel lattice showed an order of magnitude greater damage tolerance than aluminum alone.
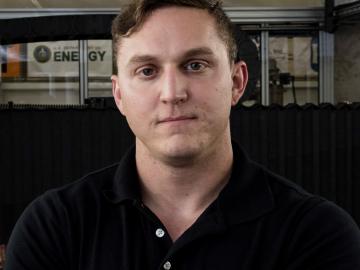
While serving in Kandahar, Afghanistan, U.S. Navy construction mechanic Matthew Sallas may not have imagined where his experience would take him next. But researchers at Oak Ridge National Laboratory certainly had the future in mind as they were creating programs to train men and wome...