Filter News
Area of Research
News Type
News Topics
- (-) 3-D Printing/Advanced Manufacturing (4)
- (-) Critical Materials (2)
- (-) Transportation (3)
- Bioenergy (1)
- Biology (1)
- Biomedical (3)
- Chemical Sciences (1)
- Composites (3)
- Computer Science (1)
- Energy Storage (3)
- Environment (1)
- Fusion (1)
- Grid (1)
- Isotopes (5)
- Materials Science (8)
- Microscopy (5)
- Nanotechnology (6)
- National Security (1)
- Neutron Science (3)
- Nuclear Energy (2)
- Partnerships (1)
- Physics (4)
- Polymers (3)
- Security (1)
- Space Exploration (1)
Media Contacts

A collection of seven technologies for lithium recovery developed by scientists from ORNL has been licensed to Element3, a Texas-based company focused on extracting lithium from wastewater produced by oil and gas production.
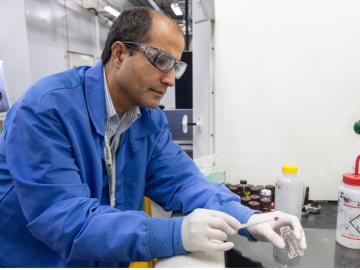
Electric vehicles can drive longer distances if their lithium-ion batteries deliver more energy in a lighter package. A prime weight-loss candidate is the current collector, a component that often adds 10% to the weight of a battery cell without contributing energy.
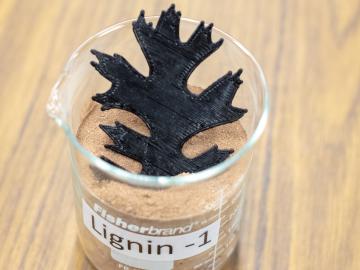
Scientists at the Department of Energy’s Oak Ridge National Laboratory have created a recipe for a renewable 3D printing feedstock that could spur a profitable new use for an intractable biorefinery byproduct: lignin.
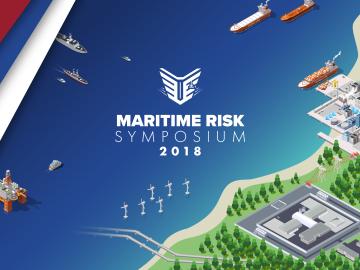
Thought leaders from across the maritime community came together at Oak Ridge National Laboratory to explore the emerging new energy landscape for the maritime transportation system during the Ninth Annual Maritime Risk Symposium.
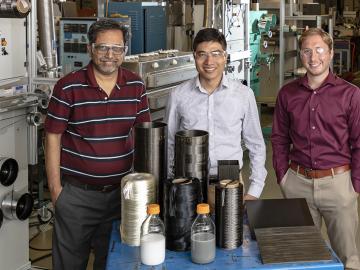
Carbon fiber composites—lightweight and strong—are great structural materials for automobiles, aircraft and other transportation vehicles. They consist of a polymer matrix, such as epoxy, into which reinforcing carbon fibers have been embedded. Because of differences in the mecha...

The construction industry may soon benefit from 3D printed molds to make concrete facades, promising lower cost and production time. Researchers at Oak Ridge National Laboratory are evaluating the performance of 3D printed molds used to precast concrete facades in a 42-story buildin...
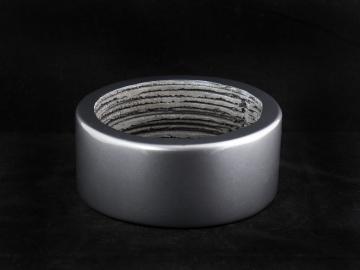
Oak Ridge National Laboratory scientists have improved a mixture of materials used to 3D print permanent magnets with increased density, which could yield longer lasting, better performing magnets for electric motors, sensors and vehicle applications. Building on previous research, ...
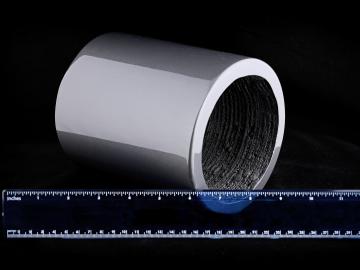
Researchers at the Department of Energy’s Oak Ridge National Laboratory have demonstrated that permanent magnets produced by additive manufacturing can outperform bonded magnets made using traditional techniques while conserving critical materials. Scientists fabric...