Filter News
Area of Research
- Advanced Manufacturing (5)
- Biology and Environment (5)
- Clean Energy (21)
- Climate and Environmental Systems (1)
- Computational Engineering (1)
- Computer Science (6)
- Fusion Energy (3)
- Materials (12)
- National Security (1)
- Neutron Science (11)
- Nuclear Science and Technology (2)
- Quantum information Science (1)
- Supercomputing (5)
- Transportation Systems (1)
News Topics
- (-) 3-D Printing/Advanced Manufacturing (10)
- (-) Advanced Reactors (6)
- (-) Artificial Intelligence (8)
- (-) Big Data (8)
- (-) Clean Water (5)
- (-) Environment (12)
- (-) Grid (7)
- (-) Microscopy (5)
- (-) Neutron Science (10)
- (-) Transportation (9)
- Bioenergy (4)
- Biology (5)
- Biomedical (3)
- Buildings (8)
- Chemical Sciences (2)
- Climate Change (3)
- Composites (3)
- Computer Science (19)
- Coronavirus (4)
- Critical Materials (4)
- Cybersecurity (1)
- Decarbonization (1)
- Energy Storage (10)
- Exascale Computing (1)
- Fusion (3)
- High-Performance Computing (4)
- Hydropower (5)
- Irradiation (1)
- Isotopes (1)
- Machine Learning (5)
- Materials (11)
- Materials Science (12)
- Mercury (1)
- Molten Salt (1)
- Nanotechnology (4)
- National Security (3)
- Nuclear Energy (9)
- Partnerships (1)
- Physics (3)
- Polymers (2)
- Quantum Science (5)
- Simulation (2)
- Space Exploration (6)
- Summit (3)
- Sustainable Energy (8)
Media Contacts

Researchers at Oak Ridge National Laboratory are using a novel approach in determining environmental impacts to aquatic species near hydropower facilities, potentially leading to smarter facility designs that can support electrical grid reliability.
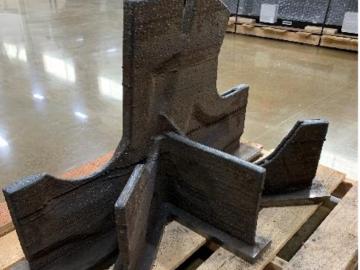
Oak Ridge National Laboratory researchers recently used large-scale additive manufacturing with metal to produce a full-strength steel component for a wind turbine, proving the technique as a viable alternative to

A new analysis from Oak Ridge National Laboratory shows that intensified aridity, or drier atmospheric conditions, is caused by human-driven increases in greenhouse gas emissions. The findings point to an opportunity to address and potentially reverse the trend by reducing emissions.
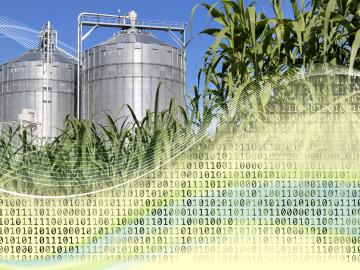
A research team from Oak Ridge National Laboratory has identified and improved the usability of data that can help accelerate innovation for the growing bioeconomy.
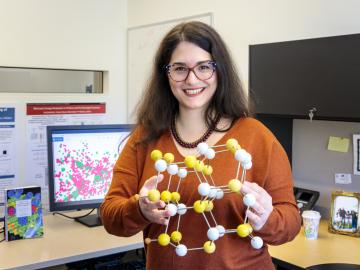
To advance sensor technologies, Oak Ridge National Laboratory researchers studied piezoelectric materials, which convert mechanical stress into electrical energy, to see how they could handle bombardment with energetic neutrons.
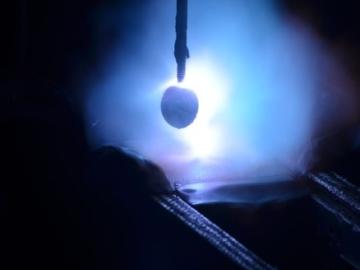
Researchers at Oak Ridge National Laboratory demonstrated that an additively manufactured polymer layer, when applied to carbon fiber reinforced plastic, or CFRP, can serve as an effective protector against aircraft lightning strikes.
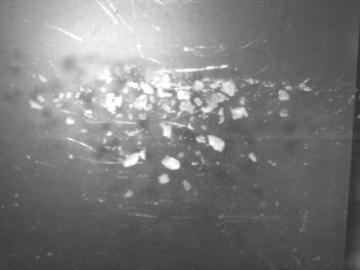
As scientists study approaches to best sustain a fusion reactor, a team led by Oak Ridge National Laboratory investigated injecting shattered argon pellets into a super-hot plasma, when needed, to protect the reactor’s interior wall from high-energy runaway electrons.
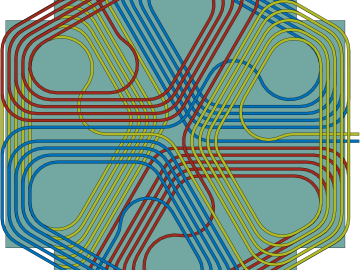
ORNL researchers created and tested new wireless charging designs that may double the power density, resulting in a lighter weight system compared with existing technologies.
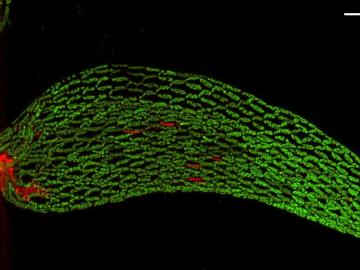
A team of scientists found that critical interactions between microbes and peat moss break down under warming temperatures, impacting moss health and ultimately carbon stored in soil.
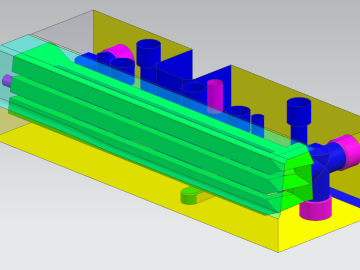
Researchers demonstrated that an additively manufactured hot stamping die can withstand up to 25,000 usage cycles, proving that this technique is a viable solution for production.