Filter News
Area of Research
News Type
News Topics
- (-) 3-D Printing/Advanced Manufacturing (16)
- (-) Advanced Reactors (2)
- (-) Biomedical (5)
- (-) Frontier (17)
- (-) Mercury (2)
- Artificial Intelligence (25)
- Big Data (9)
- Bioenergy (15)
- Biology (23)
- Biotechnology (4)
- Buildings (9)
- Chemical Sciences (18)
- Clean Water (5)
- Climate Change (29)
- Composites (4)
- Computer Science (21)
- Coronavirus (3)
- Critical Materials (4)
- Cybersecurity (9)
- Decarbonization (25)
- Education (3)
- Emergency (1)
- Energy Storage (14)
- Environment (38)
- Exascale Computing (15)
- Fossil Energy (2)
- Fusion (9)
- Grid (13)
- High-Performance Computing (31)
- Hydropower (2)
- Isotopes (9)
- Machine Learning (14)
- Materials (49)
- Materials Science (14)
- Mathematics (2)
- Microelectronics (2)
- Microscopy (7)
- Molten Salt (1)
- Nanotechnology (6)
- National Security (19)
- Net Zero (5)
- Neutron Science (27)
- Nuclear Energy (19)
- Partnerships (24)
- Physics (14)
- Polymers (3)
- Quantum Computing (9)
- Quantum Science (7)
- Renewable Energy (2)
- Security (3)
- Simulation (26)
- Software (1)
- Space Exploration (4)
- Summit (9)
- Sustainable Energy (11)
- Transportation (9)
Media Contacts
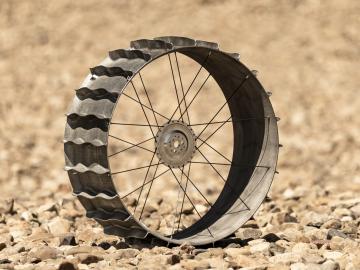
Researchers at the Department of Energy’s Oak Ridge National Laboratory, in collaboration with NASA, are taking additive manufacturing to the final frontier by 3D printing the same kind of wheel as the design used by NASA for its robotic lunar rover, demonstrating the technology for specialized parts needed for space exploration.
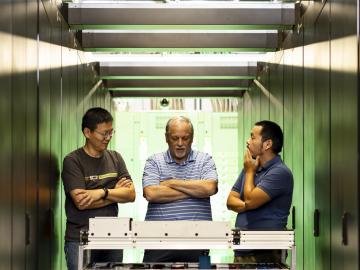
As Frontier, the world’s first exascale supercomputer, was being assembled at the Oak Ridge Leadership Computing Facility in 2021, understanding its performance on mixed-precision calculations remained a difficult prospect.
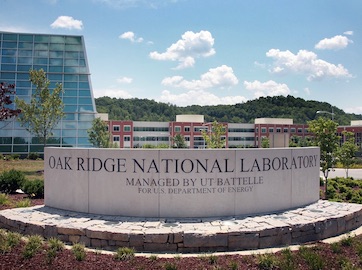
The Department of Energy’s Office of Science has selected three ORNL research teams to receive funding through DOE’s new Biopreparedness Research Virtual Environment initiative.

Outside the high-performance computing, or HPC, community, exascale may seem more like fodder for science fiction than a powerful tool for scientific research. Yet, when seen through the lens of real-world applications, exascale computing goes from ethereal concept to tangible reality with exceptional benefits.

A licensing agreement between the Department of Energy’s Oak Ridge National Laboratory and research partner ZEISS will enable industrial X-ray computed tomography, or CT, to perform rapid evaluations of 3D-printed components using ORNL’s machine

Technologies developed by researchers at ORNL have received six 2023 R&D 100 Awards.
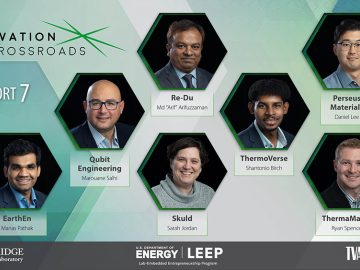
Seven entrepreneurs will embark on a two-year fellowship as the seventh cohort of Innovation Crossroads kicks off this month at ORNL. Representing a range of transformative energy technologies, Cohort 7 is a diverse class of innovators with promising new companies.

Yarom Polsky, director of the Manufacturing Science Division, or MSD, at the Department of Energy’s Oak Ridge National Laboratory, has been elected a Fellow of the American Society of Mechanical Engineers, or ASME.
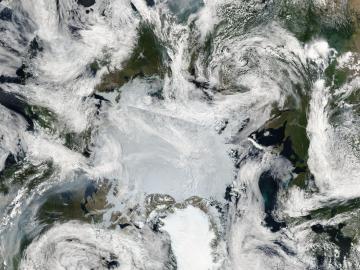
Wildfires have shaped the environment for millennia, but they are increasing in frequency, range and intensity in response to a hotter climate. The phenomenon is being incorporated into high-resolution simulations of the Earth’s climate by scientists at the Department of Energy’s Oak Ridge National Laboratory, with a mission to better understand and predict environmental change.
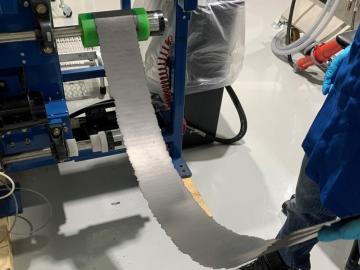
Early experiments at the Department of Energy’s Oak Ridge National Laboratory have revealed significant benefits to a dry battery manufacturing process. This eliminates the use of solvents and is more affordable, while showing promise for delivering a battery that is durable, less weighed down by inactive elements, and able to maintain a high capacity after use.