Filter News
Area of Research
News Topics
- (-) 3-D Printing/Advanced Manufacturing (5)
- (-) Bioenergy (1)
- Advanced Reactors (1)
- Biomedical (2)
- Chemical Sciences (1)
- Composites (1)
- Energy Storage (2)
- Environment (1)
- Fusion (1)
- Materials (2)
- Materials Science (5)
- Microscopy (1)
- Nanotechnology (1)
- Neutron Science (14)
- Nuclear Energy (1)
- Physics (1)
- Quantum Science (1)
- Transportation (1)
Media Contacts
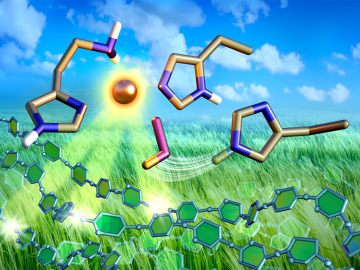
Nonfood, plant-based biofuels have potential as a green alternative to fossil fuels, but the enzymes required for production are too inefficient and costly to produce. However, new research is shining a light on enzymes from fungi that could make biofuels economically viable.
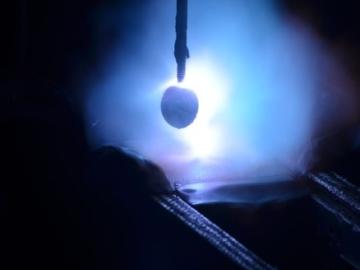
Researchers at Oak Ridge National Laboratory demonstrated that an additively manufactured polymer layer, when applied to carbon fiber reinforced plastic, or CFRP, can serve as an effective protector against aircraft lightning strikes.
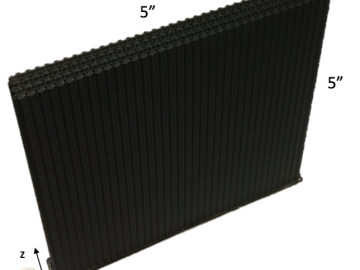
A team including Oak Ridge National Laboratory and University of Tennessee researchers demonstrated a novel 3D printing approach called Z-pinning that can increase the material’s strength and toughness by more than three and a half times compared to conventional additive manufacturing processes.
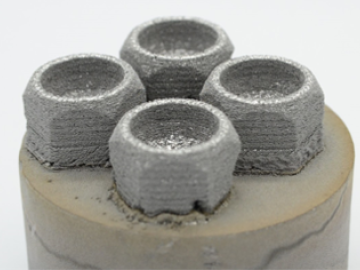
Using additive manufacturing, scientists experimenting with tungsten at Oak Ridge National Laboratory hope to unlock new potential of the high-performance heat-transferring material used to protect components from the plasma inside a fusion reactor. Fusion requires hydrogen isotopes to reach millions of degrees.
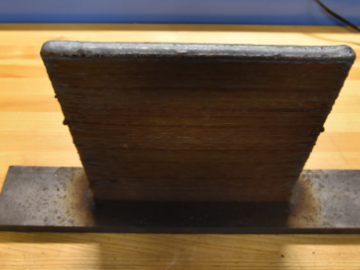
A novel additive manufacturing method developed by researchers at Oak Ridge National Laboratory could be a promising alternative for low-cost, high-quality production of large-scale metal parts with less material waste.

The construction industry may soon benefit from 3D printed molds to make concrete facades, promising lower cost and production time. Researchers at Oak Ridge National Laboratory are evaluating the performance of 3D printed molds used to precast concrete facades in a 42-story buildin...