Filter News
Area of Research
News Topics
- (-) 3-D Printing/Advanced Manufacturing (6)
- (-) Composites (2)
- (-) Cybersecurity (2)
- (-) Grid (3)
- Advanced Reactors (5)
- Artificial Intelligence (6)
- Big Data (5)
- Biomedical (1)
- Clean Water (2)
- Computer Science (16)
- Energy Storage (4)
- Environment (6)
- Fusion (3)
- Machine Learning (3)
- Materials Science (9)
- Microscopy (2)
- Molten Salt (1)
- Nanotechnology (2)
- Neutron Science (8)
- Nuclear Energy (9)
- Physics (2)
- Polymers (1)
- Quantum Science (3)
- Space Exploration (3)
- Summit (2)
- Sustainable Energy (2)
- Transportation (8)
Media Contacts
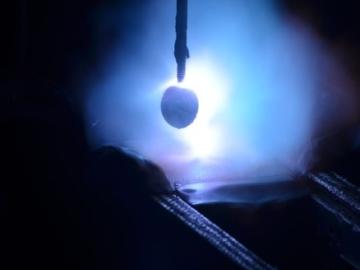
Researchers at Oak Ridge National Laboratory demonstrated that an additively manufactured polymer layer, when applied to carbon fiber reinforced plastic, or CFRP, can serve as an effective protector against aircraft lightning strikes.
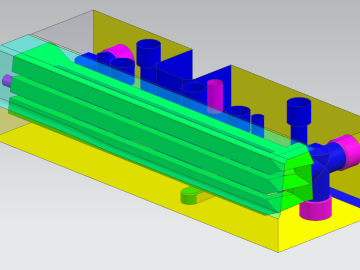
Researchers demonstrated that an additively manufactured hot stamping die can withstand up to 25,000 usage cycles, proving that this technique is a viable solution for production.
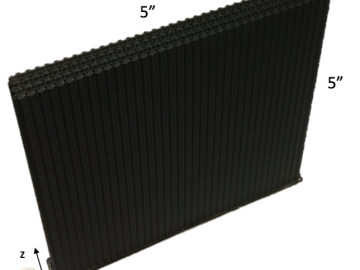
A team including Oak Ridge National Laboratory and University of Tennessee researchers demonstrated a novel 3D printing approach called Z-pinning that can increase the material’s strength and toughness by more than three and a half times compared to conventional additive manufacturing processes.
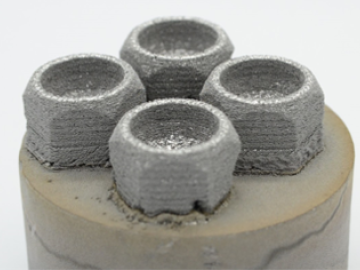
Using additive manufacturing, scientists experimenting with tungsten at Oak Ridge National Laboratory hope to unlock new potential of the high-performance heat-transferring material used to protect components from the plasma inside a fusion reactor. Fusion requires hydrogen isotopes to reach millions of degrees.

Scientists at Oak Ridge National Laboratory studying quantum communications have discovered a more practical way to share secret messages among three parties, which could ultimately lead to better cybersecurity for the electric grid
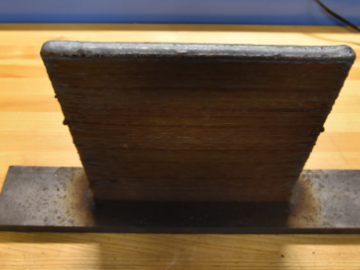
A novel additive manufacturing method developed by researchers at Oak Ridge National Laboratory could be a promising alternative for low-cost, high-quality production of large-scale metal parts with less material waste.
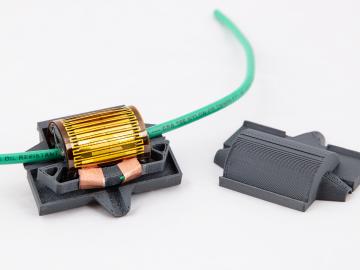
Scientists at Oak Ridge National Laboratory have developed a low-cost, printed, flexible sensor that can wrap around power cables to precisely monitor electrical loads from household appliances to support grid operations.
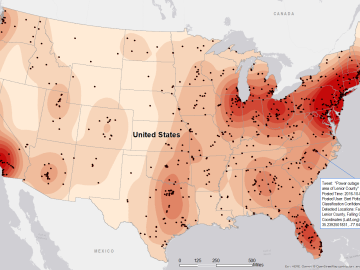
Gleaning valuable data from social platforms such as Twitter—particularly to map out critical location information during emergencies— has become more effective and efficient thanks to Oak Ridge National Laboratory.
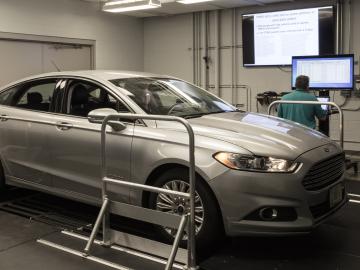
A new Oak Ridge National Laboratory-developed method promises to protect connected and autonomous vehicles from possible network intrusion. Researchers built a prototype plug-in device designed to alert drivers of vehicle cyberattacks. The prototype is coded to learn regular timing...
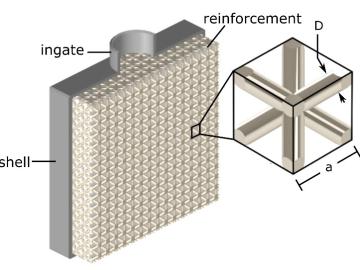
A new manufacturing method created by Oak Ridge National Laboratory and Rice University combines 3D printing with traditional casting to produce damage-tolerant components composed of multiple materials. Composite components made by pouring an aluminum alloy over a printed steel lattice showed an order of magnitude greater damage tolerance than aluminum alone.