Filter News
Area of Research
- Advanced Manufacturing (4)
- Biology and Environment (7)
- Clean Energy (24)
- Fusion and Fission (7)
- Fusion Energy (7)
- Materials (14)
- Materials for Computing (1)
- National Security (1)
- Neutron Science (2)
- Nuclear Science and Technology (11)
- Nuclear Systems Modeling, Simulation and Validation (1)
- Supercomputing (1)
News Topics
- (-) Advanced Reactors (34)
- (-) Composites (26)
- (-) Renewable Energy (2)
- 3-D Printing/Advanced Manufacturing (119)
- Artificial Intelligence (91)
- Big Data (53)
- Bioenergy (91)
- Biology (98)
- Biomedical (58)
- Biotechnology (22)
- Buildings (57)
- Chemical Sciences (63)
- Clean Water (29)
- Climate Change (99)
- Computer Science (186)
- Coronavirus (46)
- Critical Materials (25)
- Cybersecurity (35)
- Decarbonization (79)
- Education (4)
- Element Discovery (1)
- Emergency (2)
- Energy Storage (108)
- Environment (194)
- Exascale Computing (37)
- Fossil Energy (5)
- Frontier (42)
- Fusion (53)
- Grid (62)
- High-Performance Computing (84)
- Hydropower (11)
- Irradiation (3)
- Isotopes (53)
- ITER (7)
- Machine Learning (47)
- Materials (143)
- Materials Science (139)
- Mathematics (7)
- Mercury (12)
- Microelectronics (2)
- Microscopy (51)
- Molten Salt (8)
- Nanotechnology (60)
- National Security (60)
- Net Zero (13)
- Neutron Science (131)
- Nuclear Energy (106)
- Partnerships (43)
- Physics (60)
- Polymers (33)
- Quantum Computing (33)
- Quantum Science (68)
- Security (24)
- Simulation (46)
- Software (1)
- Space Exploration (25)
- Statistics (3)
- Summit (57)
- Sustainable Energy (125)
- Transformational Challenge Reactor (7)
- Transportation (96)
Media Contacts

Chemical and environmental engineer Samarthya Bhagia is focused on achieving carbon neutrality and a circular economy by designing new plant-based materials for a range of applications from energy storage devices and sensors to environmentally friendly bioplastics.

An Oak Ridge National Laboratory team developed a novel technique using sensors to monitor seismic and acoustic activity and machine learning to differentiate operational activities at facilities from “noise” in the recorded data.
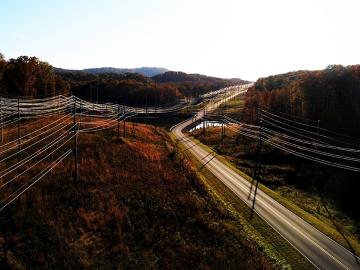
ORNL and the Tennessee Valley Authority, or TVA, are joining forces to advance decarbonization technologies from discovery through deployment through a new memorandum of understanding, or MOU.
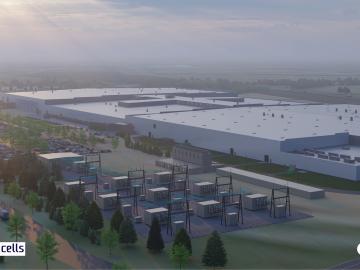
ORNL, TVA and TNECD were recognized by the Federal Laboratory Consortium for their impactful partnership that resulted in a record $2.3 billion investment by Ultium Cells, a General Motors and LG Energy Solution joint venture, to build a battery cell manufacturing plant in Spring Hill, Tennessee.

A novel method to 3D print components for nuclear reactors, developed by the Department of Energy’s Oak Ridge National Laboratory, has been licensed by Ultra Safe Nuclear Corporation.

Ten scientists from the Department of Energy’s Oak Ridge National Laboratory are among the world’s most highly cited researchers, according to a bibliometric analysis conducted by the scientific publication analytics firm Clarivate.
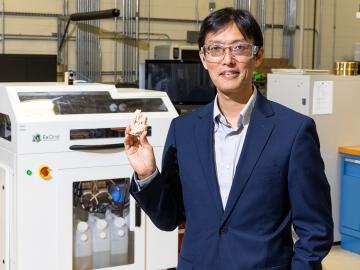
Researchers at ORNL designed a novel polymer to bind and strengthen silica sand for binder jet additive manufacturing, a 3D-printing method used by industries for prototyping and part production.
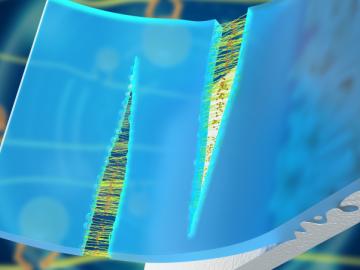
Research teams from the Department of Energy’s Oak Ridge National Laboratory and their technologies have received seven 2021 R&D 100 Awards, plus special recognition for a COVID-19-related project.

Staff at Oak Ridge National Laboratory organized transport for a powerful component that is critical to the world’s largest experiment, the international ITER project.
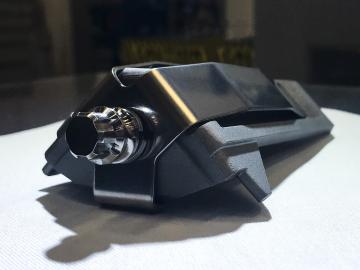
Four first-of-a-kind 3D-printed fuel assembly brackets, produced at the Department of Energy’s Manufacturing Demonstration Facility at Oak Ridge National Laboratory, have been installed and are now under routine operating