Filter News
Area of Research
News Topics
- (-) 3-D Printing/Advanced Manufacturing (119)
- (-) Net Zero (13)
- Advanced Reactors (34)
- Artificial Intelligence (90)
- Big Data (51)
- Bioenergy (90)
- Biology (97)
- Biomedical (58)
- Biotechnology (22)
- Buildings (56)
- Chemical Sciences (62)
- Clean Water (29)
- Climate Change (97)
- Composites (25)
- Computer Science (185)
- Coronavirus (46)
- Critical Materials (25)
- Cybersecurity (35)
- Decarbonization (78)
- Education (4)
- Element Discovery (1)
- Emergency (2)
- Energy Storage (108)
- Environment (194)
- Exascale Computing (37)
- Fossil Energy (5)
- Frontier (42)
- Fusion (53)
- Grid (61)
- High-Performance Computing (84)
- Hydropower (11)
- Irradiation (3)
- Isotopes (51)
- ITER (7)
- Machine Learning (47)
- Materials (142)
- Materials Science (137)
- Mathematics (7)
- Mercury (12)
- Microelectronics (2)
- Microscopy (51)
- Molten Salt (8)
- Nanotechnology (60)
- National Security (60)
- Neutron Science (130)
- Nuclear Energy (105)
- Partnerships (41)
- Physics (59)
- Polymers (32)
- Quantum Computing (31)
- Quantum Science (66)
- Renewable Energy (2)
- Security (24)
- Simulation (45)
- Software (1)
- Space Exploration (25)
- Statistics (3)
- Summit (57)
- Sustainable Energy (123)
- Transformational Challenge Reactor (7)
- Transportation (95)
Media Contacts

Scientists at ORNL have developed 3D-printed collimator techniques that can be used to custom design collimators that better filter out noise during different types of neutron scattering experiments
ORNL scientists have determined how to avoid costly and potentially irreparable damage to large metallic parts fabricated through additive manufacturing, also known as 3D printing, that is caused by residual stress in the material.
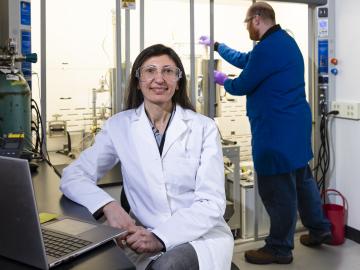
Canan Karakaya, a R&D Staff member in the Chemical Process Scale-Up group at ORNL, was inspired to become a chemical engineer after she experienced a magical transformation that turned ammonia gas into ammonium nitrate, turning a liquid into white flakes gently floating through the air.
The United States could triple its current bioeconomy by producing more than 1 billion tons per year of plant-based biomass for renewable fuels, while meeting projected demands for food, feed, fiber, conventional forest products and exports, according to the DOE’s latest Billion-Ton Report led by ORNL.
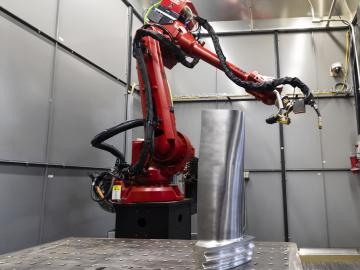
Researchers at ORNL became the first to 3D-print large rotating steam turbine blades for generating energy in power plants.
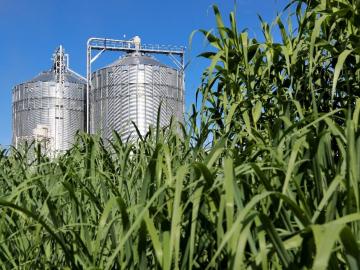
Scientists from more than a dozen institutions have completed a first-of-its-kind high-resolution assessment of carbon dioxide removal potential in the United States, charting a path to achieve a net-zero greenhouse gas economy by 2050.

Four scientists affiliated with ORNL were named Battelle Distinguished Inventors during the lab’s annual Innovation Awards on Dec. 1 in recognition of being granted 14 or more United States patents.
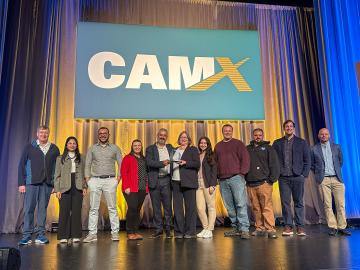
The Hub & Spoke Sustainable Materials & Manufacturing Alliance for Renewable Technologies, or SM2ART, program has been honored with the composites industry’s Combined Strength Award at the Composites and Advanced Materials Expo, or CAMX, 2023 in Atlanta. This distinction goes to the team that applies their knowledge, resources and talent to solve a problem by making the best use of composites materials.
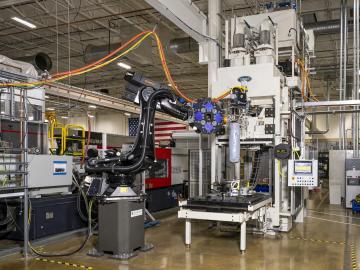
An Oak Ridge National Laboratory-developed advanced manufacturing technology, AMCM, was recently licensed by Orbital Composites and enables the rapid production of composite-based components, which could accelerate the decarbonization of vehicles
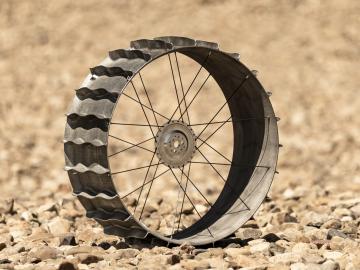
Researchers at the Department of Energy’s Oak Ridge National Laboratory, in collaboration with NASA, are taking additive manufacturing to the final frontier by 3D printing the same kind of wheel as the design used by NASA for its robotic lunar rover, demonstrating the technology for specialized parts needed for space exploration.