Filter News
Area of Research
- (-) Advanced Manufacturing (24)
- (-) National Security (31)
- Biology and Environment (68)
- Building Technologies (3)
- Clean Energy (185)
- Computational Biology (1)
- Computational Engineering (3)
- Computer Science (12)
- Electricity and Smart Grid (3)
- Energy Sciences (1)
- Fuel Cycle Science and Technology (1)
- Functional Materials for Energy (1)
- Fusion and Fission (33)
- Fusion Energy (11)
- Isotope Development and Production (1)
- Isotopes (5)
- Materials (117)
- Materials Characterization (1)
- Materials for Computing (19)
- Materials Under Extremes (1)
- Mathematics (1)
- Neutron Science (41)
- Nuclear Science and Technology (37)
- Nuclear Systems Modeling, Simulation and Validation (1)
- Quantum information Science (9)
- Sensors and Controls (1)
- Supercomputing (96)
- Transportation Systems (1)
News Topics
- (-) 3-D Printing/Advanced Manufacturing (24)
- (-) Composites (3)
- (-) Grid (6)
- (-) Machine Learning (13)
- (-) Materials Science (8)
- (-) Nuclear Energy (7)
- (-) Quantum Science (1)
- (-) Summit (2)
- (-) Sustainable Energy (8)
- Advanced Reactors (2)
- Artificial Intelligence (13)
- Big Data (6)
- Bioenergy (4)
- Biology (5)
- Biomedical (2)
- Biotechnology (1)
- Buildings (1)
- Chemical Sciences (2)
- Climate Change (5)
- Computer Science (20)
- Coronavirus (2)
- Cybersecurity (20)
- Decarbonization (2)
- Energy Storage (2)
- Environment (5)
- Exascale Computing (1)
- Frontier (1)
- Fusion (2)
- High-Performance Computing (4)
- Materials (8)
- Nanotechnology (1)
- National Security (34)
- Neutron Science (6)
- Partnerships (4)
- Physics (1)
- Security (11)
- Simulation (1)
- Space Exploration (1)
- Transformational Challenge Reactor (1)
- Transportation (2)
Media Contacts
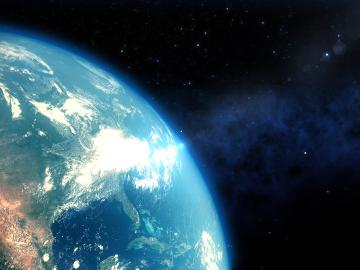
Tackling the climate crisis and achieving an equitable clean energy future are among the biggest challenges of our time.

Unequal access to modern infrastructure is a feature of growing cities, according to a study published this week in the Proceedings of the National Academy of Sciences
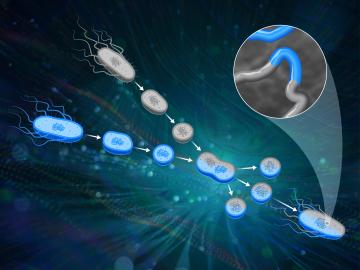
ORNL scientists had a problem mapping the genomes of bacteria to better understand the origins of their physical traits and improve their function for bioenergy production.
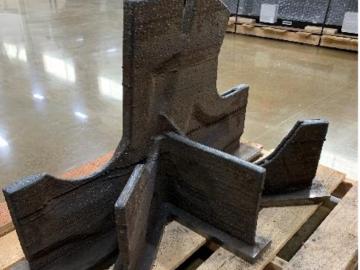
Oak Ridge National Laboratory researchers recently used large-scale additive manufacturing with metal to produce a full-strength steel component for a wind turbine, proving the technique as a viable alternative to

Oak Ridge National Laboratory researchers determined that designing polymers specifically with upcycling in mind could reduce future plastic waste considerably and facilitate a circular economy where the material is used repeatedly.
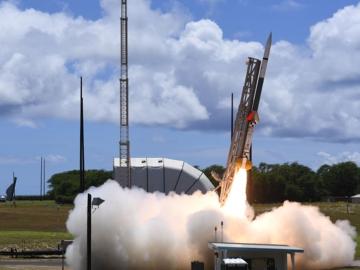
Oak Ridge National Laboratory researchers have developed a novel process to manufacture extreme heat resistant carbon-carbon composites. The performance of these materials will be tested in a U.S. Navy rocket that NASA will launch this fall.

A research team at Oak Ridge National Laboratory have 3D printed a thermal protection shield, or TPS, for a capsule that will launch with the Cygnus cargo spacecraft as part of the supply mission to the International Space Station.
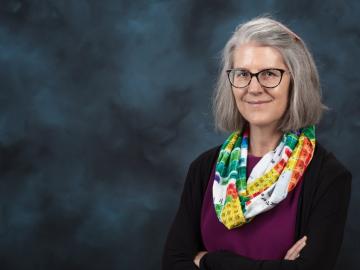
Deborah Frincke, one of the nation’s preeminent computer scientists and cybersecurity experts, serves as associate laboratory director of ORNL’s National Security Science Directorate. Credit: Carlos Jones/ORNL, U.S. Dept. of Energy
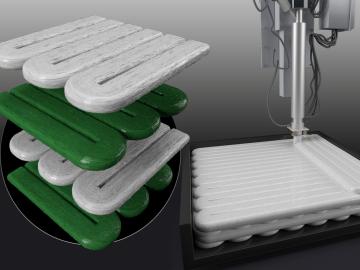
Oak Ridge National Laboratory researchers combined additive manufacturing with conventional compression molding to produce high-performance thermoplastic composites reinforced with short carbon fibers.

A team of Oak Ridge National Laboratory researchers demonstrated that an additively manufactured hot stamping die – a tool used to create car body components – cooled faster than those produced by conventional manufacturing methods.