Filter News
Area of Research
- Advanced Manufacturing (11)
- Biology and Environment (8)
- Building Technologies (1)
- Clean Energy (41)
- Computational Engineering (2)
- Computer Science (7)
- Electricity and Smart Grid (1)
- Fusion Energy (1)
- Materials (15)
- Materials for Computing (4)
- Mathematics (1)
- National Security (3)
- Neutron Science (2)
- Nuclear Science and Technology (3)
- Quantum information Science (3)
- Sensors and Controls (1)
- Supercomputing (8)
News Type
News Topics
- (-) 3-D Printing/Advanced Manufacturing (30)
- (-) Big Data (15)
- (-) Clean Water (13)
- (-) Grid (20)
- (-) Machine Learning (10)
- (-) Molten Salt (5)
- (-) Nanotechnology (12)
- (-) Quantum Science (10)
- Advanced Reactors (13)
- Artificial Intelligence (13)
- Bioenergy (15)
- Biology (17)
- Biomedical (11)
- Biotechnology (3)
- Buildings (17)
- Chemical Sciences (7)
- Climate Change (20)
- Composites (9)
- Computer Science (39)
- Coronavirus (11)
- Critical Materials (11)
- Cybersecurity (3)
- Decarbonization (7)
- Energy Storage (30)
- Environment (43)
- Exascale Computing (1)
- Frontier (1)
- Fusion (9)
- High-Performance Computing (11)
- Hydropower (6)
- Irradiation (2)
- Isotopes (5)
- ITER (3)
- Materials (34)
- Materials Science (31)
- Mathematics (1)
- Mercury (3)
- Microscopy (11)
- National Security (3)
- Net Zero (1)
- Neutron Science (27)
- Nuclear Energy (18)
- Partnerships (1)
- Physics (4)
- Polymers (8)
- Quantum Computing (4)
- Security (1)
- Simulation (6)
- Space Exploration (10)
- Statistics (1)
- Summit (6)
- Sustainable Energy (42)
- Transportation (35)
Media Contacts
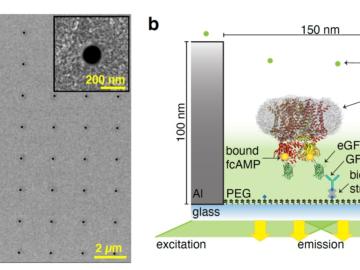
Researchers working with Oak Ridge National Laboratory developed a new method to observe how proteins, at the single-molecule level, bind with other molecules and more accurately pinpoint certain molecular behavior in complex
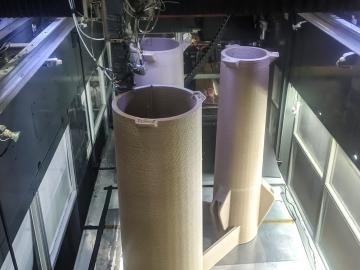
A team of researchers at Oak Ridge National Laboratory demonstrated the ability to additively manufacture power poles from bioderived and recycled materials, which could more quickly restore electricity after natural disasters.

Oak Ridge National Laboratory researchers demonstrated their wireless charging technology on an autonomous electric vehicle for the first time in a project with Local Motors.
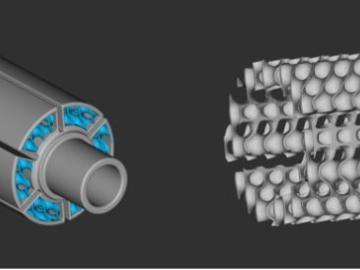
Additive manufacturing can make the design and production of specialized tools for geothermal energy cheaper and more efficient, according to a study by Oak Ridge National Laboratory.
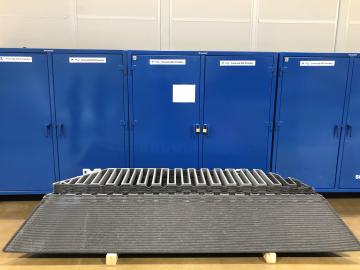
Oak Ridge National Laboratory researchers, in collaboration with Cincinnati Inc., demonstrated the potential for using multimaterials and recycled composites in large-scale applications by 3D printing a mold that replicated a single facet of a
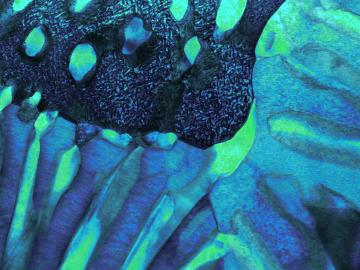
Oak Ridge National Laboratory scientists proved molybdenum titanium carbide, a refractory metal alloy that can withstand extreme temperature environments, can also be crack free and dense when produced with electron beam powder bed fusion.
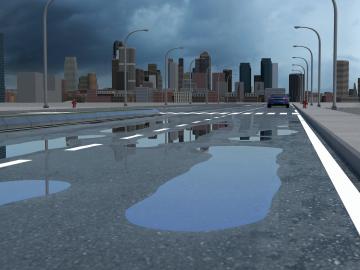
Researchers at Oak Ridge National Laboratory have identified a statistical relationship between the growth of cities and the spread of paved surfaces like roads and sidewalks. These impervious surfaces impede the flow of water into the ground, affecting the water cycle and, by extension, the climate.
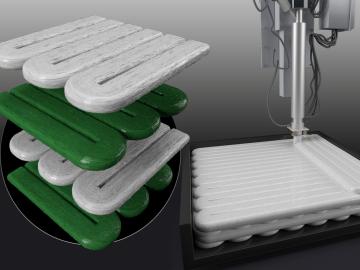
Oak Ridge National Laboratory researchers combined additive manufacturing with conventional compression molding to produce high-performance thermoplastic composites reinforced with short carbon fibers.
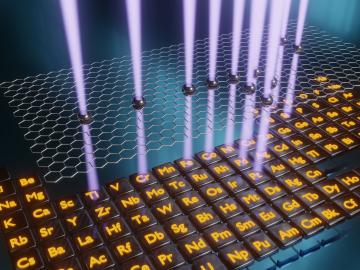
Oak Ridge National Laboratory scientists demonstrated that an electron microscope can be used to selectively remove carbon atoms from graphene’s atomically thin lattice and stitch transition-metal dopant atoms in their place.

A team of Oak Ridge National Laboratory researchers demonstrated that an additively manufactured hot stamping die – a tool used to create car body components – cooled faster than those produced by conventional manufacturing methods.