
Filter News
Area of Research
- Advanced Manufacturing (10)
- Biological Systems (1)
- Biology and Environment (67)
- Clean Energy (87)
- Computational Biology (1)
- Computational Engineering (1)
- Computer Science (3)
- Fusion and Fission (4)
- Isotopes (5)
- Materials (44)
- Materials for Computing (6)
- National Security (32)
- Neutron Science (29)
- Nuclear Science and Technology (6)
- Quantum information Science (5)
- Supercomputing (84)
News Type
News Topics
- (-) 3-D Printing/Advanced Manufacturing (88)
- (-) Bioenergy (74)
- (-) Biomedical (49)
- (-) Clean Water (17)
- (-) Cybersecurity (31)
- (-) Machine Learning (36)
- (-) Quantum Science (60)
- (-) Summit (54)
- Advanced Reactors (19)
- Artificial Intelligence (85)
- Big Data (37)
- Biology (83)
- Biotechnology (20)
- Buildings (38)
- Chemical Sciences (60)
- Climate Change (74)
- Composites (19)
- Computer Science (150)
- Coronavirus (34)
- Critical Materials (16)
- Decarbonization (67)
- Education (5)
- Element Discovery (1)
- Emergency (2)
- Energy Storage (73)
- Environment (141)
- Exascale Computing (41)
- Fossil Energy (5)
- Frontier (42)
- Fusion (47)
- Grid (42)
- High-Performance Computing (79)
- Hydropower (5)
- Isotopes (49)
- ITER (4)
- Materials (106)
- Materials Science (102)
- Mathematics (7)
- Mercury (9)
- Microelectronics (4)
- Microscopy (36)
- Molten Salt (4)
- Nanotechnology (42)
- National Security (65)
- Net Zero (11)
- Neutron Science (105)
- Nuclear Energy (83)
- Partnerships (50)
- Physics (55)
- Polymers (20)
- Quantum Computing (34)
- Renewable Energy (2)
- Security (24)
- Simulation (43)
- Software (1)
- Space Exploration (15)
- Statistics (2)
- Sustainable Energy (78)
- Transformational Challenge Reactor (7)
- Transportation (52)
Media Contacts
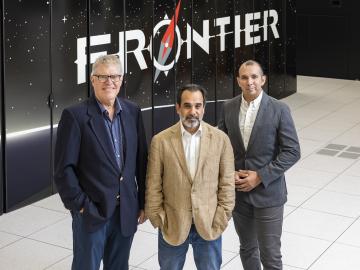
A study by more than a dozen scientists at the Department of Energy’s Oak Ridge National Laboratory examines potential strategies to integrate quantum computing with the world’s most powerful supercomputing systems in the pursuit of science.

Jeremiah Sewell leads a team at ORNL, working on xenon-129 production for lung imaging. Reflecting on his career, Sewell views each opportunity as a "door" he steps through, leveraging over 25 years of experience in nuclear power and centrifuge operations to advance the facility’s mission.
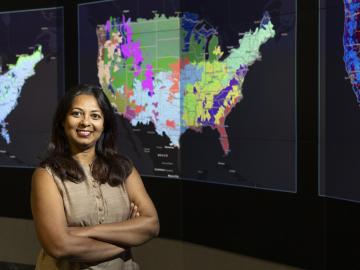
Debjani Singh, a senior scientist at ORNL, leads the HydroSource project, which enhances hydropower research by making water data more accessible and useful. With a background in water resources, data science, and earth science, Singh applies innovative tools like AI to advance research. Her career, shaped by her early exposure to science in India, focuses on bridging research with practical applications.

At ORNL, a group of scientists used neutron scattering techniques to investigate a relatively new functional material called a Weyl semimetal. These Weyl fermions move very quickly in a material and can carry electrical charge at room temperature. Scientists think that Weyl semimetals, if used in future electronics, could allow electricity to flow more efficiently and enable more energy-efficient computers and other electronic devices.
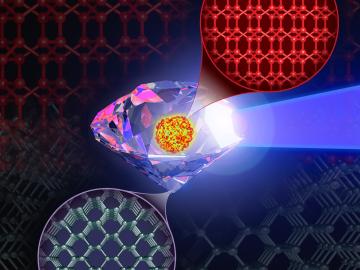
The world’s fastest supercomputer helped researchers simulate synthesizing a material harder and tougher than a diamond — or any other substance on Earth. The study used Frontier to predict the likeliest strategy to synthesize such a material, thought to exist so far only within the interiors of giant exoplanets, or planets beyond our solar system.
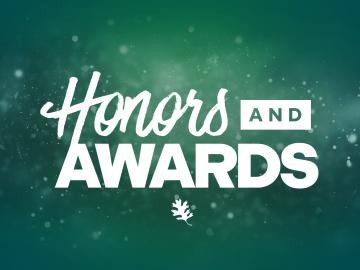
Two additive manufacturing researchers from ORNL received prestigious awards from national organizations. Amy Elliott and Nadim Hmeidat, who both work in the Manufacturing Science Division, were recognized recently for their early career accomplishments.

Brian Sanders is focused on impactful, multidisciplinary science at Oak Ridge National Laboratory, developing solutions for everything from improved imaging of plant-microbe interactions that influence ecosystem health to advancing new treatments for cancer and viral infections.
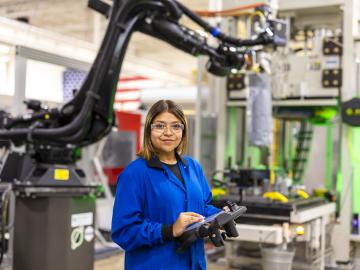
Brittany Rodriguez never imagined she would pursue a science career at a Department of Energy national laboratory. However, after some encouraging words from her mother, input from key mentors at the University of Texas Rio Grande Valley, or UTRGV, and a lot of hard work, Rodriguez landed at DOE’s Manufacturing Demonstration Facility, or MDF, at Oak Ridge National Laboratory.
The contract will be awarded to develop the newest high-performance computing system at the Oak Ridge Leadership Computing Facility.
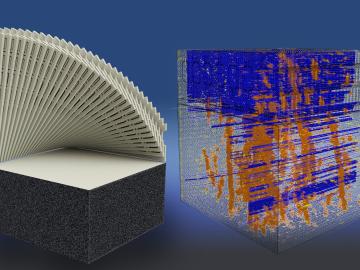
The Department of Energy’s Oak Ridge National Laboratory has publicly released a new set of additive manufacturing data that industry and researchers can use to evaluate and improve the quality of 3D-printed components. The breadth of the datasets can significantly boost efforts to verify the quality of additively manufactured parts using only information gathered during printing, without requiring expensive and time-consuming post-production analysis.