Filter News
Area of Research
- (-) Materials for Computing (5)
- (-) Nuclear Science and Technology (9)
- Biology and Environment (8)
- Clean Energy (24)
- Fusion and Fission (2)
- Fusion Energy (4)
- Isotopes (1)
- Materials (14)
- National Security (2)
- Neutron Science (12)
- Nuclear Systems Modeling, Simulation and Validation (1)
- Quantum information Science (2)
- Supercomputing (27)
News Topics
- (-) Advanced Reactors (7)
- (-) Biomedical (4)
- (-) Summit (1)
- (-) Transportation (3)
- 3-D Printing/Advanced Manufacturing (6)
- Bioenergy (1)
- Computer Science (3)
- Coronavirus (1)
- Decarbonization (1)
- Energy Storage (3)
- Environment (1)
- Fusion (6)
- Isotopes (5)
- Materials Science (5)
- Molten Salt (4)
- Nanotechnology (1)
- Neutron Science (4)
- Nuclear Energy (21)
- Physics (1)
- Polymers (1)
- Space Exploration (2)
- Sustainable Energy (3)
- Transformational Challenge Reactor (3)
Media Contacts
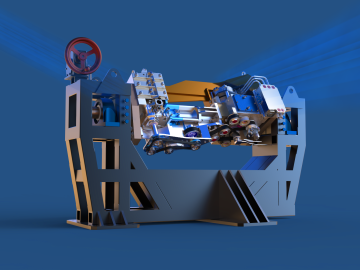
In the quest for advanced vehicles with higher energy efficiency and ultra-low emissions, ORNL researchers are accelerating a research engine that gives scientists and engineers an unprecedented view inside the atomic-level workings of combustion engines in real time.
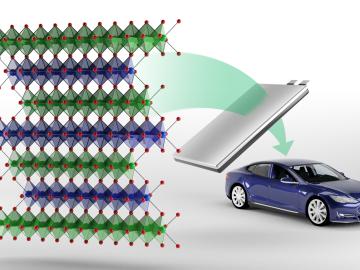
Oak Ridge National Laboratory researchers have developed a new family of cathodes with the potential to replace the costly cobalt-based cathodes typically found in today’s lithium-ion batteries that power electric vehicles and consumer electronics.
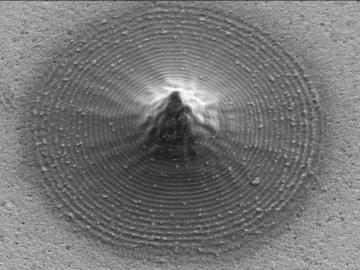
Scientists at Oak Ridge National Laboratory and the University of Tennessee designed and demonstrated a method to make carbon-based materials that can be used as electrodes compatible with a specific semiconductor circuitry.
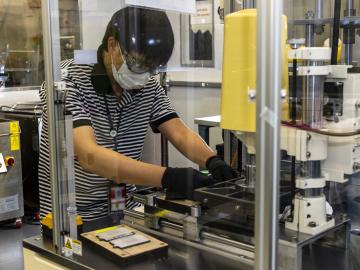
Soteria Battery Innovation Group has exclusively licensed and optioned a technology developed by Oak Ridge National Laboratory designed to eliminate thermal runaway in lithium ion batteries due to mechanical damage.
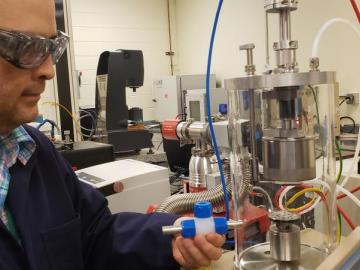
Four research teams from the Department of Energy’s Oak Ridge National Laboratory and their technologies have received 2020 R&D 100 Awards.
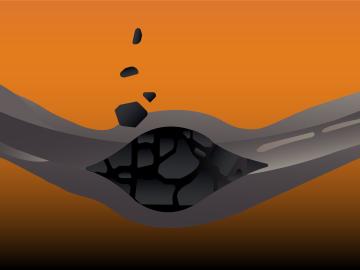
A developing method to gauge the occurrence of a nuclear reactor anomaly has the potential to save millions of dollars.
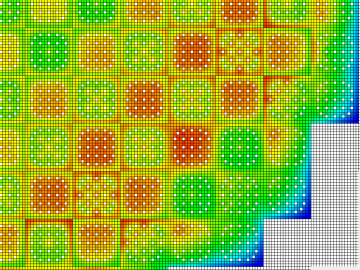
As CASL ends and transitions to VERA Users Group, ORNL looks at the history of the program and its impact on the nuclear industry.
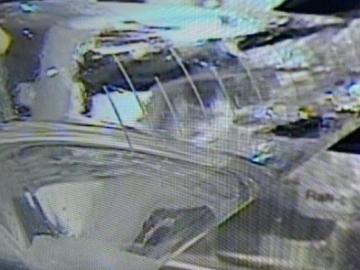
Oak Ridge National Laboratory researchers have discovered a better way to separate actinium-227, a rare isotope essential for an FDA-approved cancer treatment.
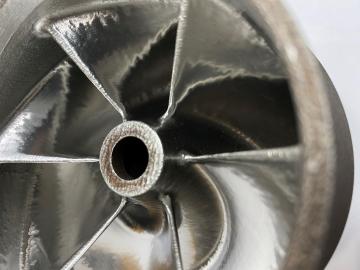
Scientists at the Department of Energy Manufacturing Demonstration Facility at ORNL have their eyes on the prize: the Transformational Challenge Reactor, or TCR, a microreactor built using 3D printing and other new approaches that will be up and running by 2023.

Researchers at the Department of Energy’s Oak Ridge National Laboratory are refining their design of a 3D-printed nuclear reactor core, scaling up the additive manufacturing process necessary to build it, and developing methods