
Filter News
Area of Research
- Advanced Manufacturing (20)
- Biology and Environment (21)
- Building Technologies (3)
- Clean Energy (90)
- Computer Science (2)
- Energy Sciences (1)
- Fusion and Fission (2)
- Fusion Energy (2)
- Materials (41)
- Materials for Computing (10)
- National Security (3)
- Neutron Science (6)
- Nuclear Science and Technology (3)
- Supercomputing (12)
News Type
News Topics
- (-) 3-D Printing/Advanced Manufacturing (76)
- (-) Microscopy (27)
- (-) Sustainable Energy (75)
- Advanced Reactors (24)
- Artificial Intelligence (48)
- Big Data (24)
- Bioenergy (39)
- Biology (40)
- Biomedical (28)
- Biotechnology (11)
- Buildings (35)
- Chemical Sciences (43)
- Clean Water (15)
- Climate Change (46)
- Composites (20)
- Computer Science (101)
- Coronavirus (28)
- Critical Materials (23)
- Cybersecurity (20)
- Decarbonization (31)
- Education (3)
- Element Discovery (1)
- Energy Storage (74)
- Environment (81)
- Exascale Computing (11)
- Fossil Energy (2)
- Frontier (16)
- Fusion (26)
- Grid (37)
- High-Performance Computing (41)
- Hydropower (6)
- Irradiation (2)
- Isotopes (23)
- ITER (5)
- Machine Learning (25)
- Materials (94)
- Materials Science (87)
- Mathematics (2)
- Mercury (5)
- Microelectronics (1)
- Molten Salt (8)
- Nanotechnology (38)
- National Security (21)
- Net Zero (5)
- Neutron Science (78)
- Nuclear Energy (46)
- Partnerships (30)
- Physics (28)
- Polymers (21)
- Quantum Computing (14)
- Quantum Science (37)
- Renewable Energy (1)
- Security (13)
- Simulation (16)
- Space Exploration (13)
- Statistics (2)
- Summit (27)
- Transformational Challenge Reactor (4)
- Transportation (61)
Media Contacts
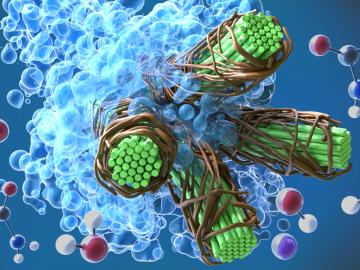
A team led by scientists at ORNL identified and demonstrated a method to process a plant-based material called nanocellulose that reduced energy needs by a whopping 21%, using simulations on the lab’s supercomputers and follow-on analysis.
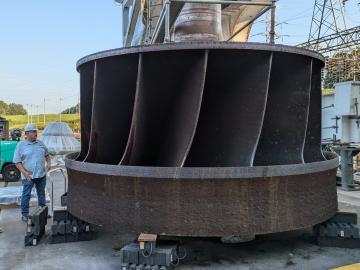
ORNL is working with industry partners to develop a technique that combines 3D printing and conventional machining to produce large metal parts for clean energy applications. The project, known as Rapid Research on Universal Near Net Shape Fabrication Strategies for Expedited Runner Systems, or Rapid RUNNERS, recently received $15 million in funding from DOE.

Oak Ridge National Laboratory scientists have developed a method leveraging artificial intelligence to accelerate the identification of environmentally friendly solvents for industrial carbon capture, biomass processing, rechargeable batteries and other applications.
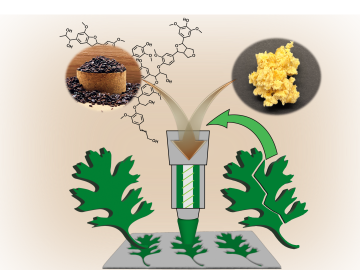
Oak Ridge National Laboratory scientists ingeniously created a sustainable, soft material by combining rubber with woody reinforcements and incorporating “smart” linkages between the components that unlock on demand.
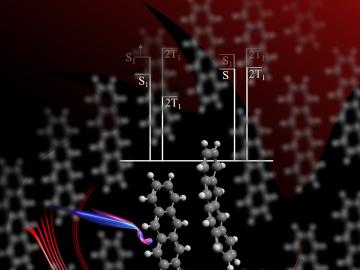
ORNL scientists develop a sample holder that tumbles powdered photochemical materials within a neutron beamline — exposing more of the material to light for increased photo-activation and better photochemistry data capture.
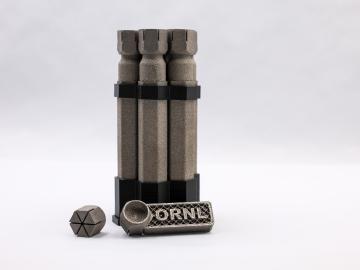
ORNL researchers used electron-beam additive manufacturing to 3D-print the first complex, defect-free tungsten parts with complex geometries.
The United States could triple its current bioeconomy by producing more than 1 billion tons per year of plant-based biomass for renewable fuels, while meeting projected demands for food, feed, fiber, conventional forest products and exports, according to the DOE’s latest Billion-Ton Report led by ORNL.

Four scientists affiliated with ORNL were named Battelle Distinguished Inventors during the lab’s annual Innovation Awards on Dec. 1 in recognition of being granted 14 or more United States patents.
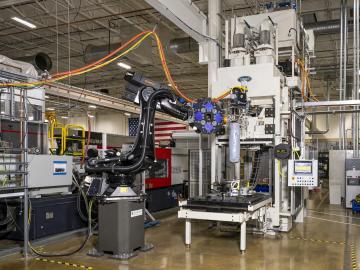
An Oak Ridge National Laboratory-developed advanced manufacturing technology, AMCM, was recently licensed by Orbital Composites and enables the rapid production of composite-based components, which could accelerate the decarbonization of vehicles

Oak Ridge National Laboratory researchers have conducted a comprehensive life cycle, cost and carbon emissions analysis on 3D-printed molds for precast concrete and determined the method is economically beneficial compared to conventional wood molds.