Filter Results
Related Organization
- Biological and Environmental Systems Science Directorate (23)
- Computing and Computational Sciences Directorate (35)
- Energy Science and Technology Directorate
(217)
- Fusion and Fission Energy and Science Directorate (21)
- Information Technology Services Directorate (2)
- Isotope Science and Enrichment Directorate (6)
- National Security Sciences Directorate (17)
- Neutron Sciences Directorate (11)
- Physical Sciences Directorate (128)
- User Facilities (27)
Researcher
- Omer Onar
- Subho Mukherjee
- Vivek Sujan
- Mostak Mohammad
- Vandana Rallabandi
- Ryan Dehoff
- Erdem Asa
- Shajjad Chowdhury
- Burak Ozpineci
- Emrullah Aydin
- Jon Wilkins
- Adam Siekmann
- Gui-Jia Su
- Michael Kirka
- Veda Prakash Galigekere
- Vincent Paquit
- Adam Stevens
- Ahmed Hassen
- Alex Plotkowski
- Alice Perrin
- Ali Riza Ekti
- Amir K Ziabari
- Amit Shyam
- Andres Marquez Rossy
- Blane Fillingim
- Brian Post
- Christopher Ledford
- Clay Leach
- David Nuttall
- Hong Wang
- Hyeonsup Lim
- Isabelle Snyder
- James Haley
- Lingxiao Xue
- Patxi Fernandez-Zelaia
- Peeyush Nandwana
- Philip Bingham
- Rafal Wojda
- Rangasayee Kannan
- Roger G Miller
- Sarah Graham
- Singanallur Venkatakrishnan
- Sudarsanam Babu
- Vipin Kumar
- Vlastimil Kunc
- William Peter
- Yan-Ru Lin
- Ying Yang
- Yukinori Yamamoto
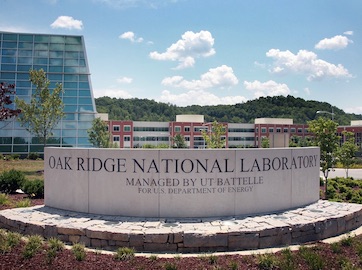
Technologies directed to an integrated on-board charger for dual motor based electric vehicle power train are described.
Contact:
To learn more about this technology, email partnerships@ornl.gov or call 865-574-1051.
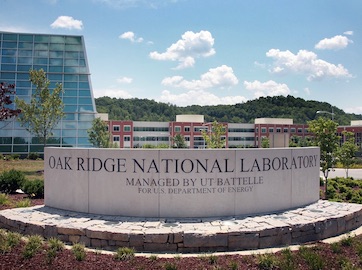
This invention proposes a Honeycomb-DD coupling structure that addresses the shortcomings of the conventional honeycomb coil array and gathering the advantage of DD and honeycomb designs advantages in a single design.
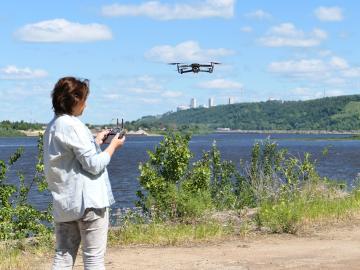
Wireless charging systems need to operate at high frequency, at or near resonance, to maximize power transfer distance and efficiency. High voltages appear across the inductors and capacitors. The use of discrete components reduces efficiency, increases system complexity.
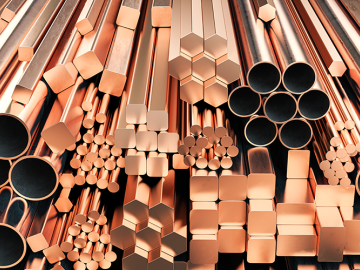
In manufacturing parts for industry using traditional molds and dies, about 70 percent to 80 percent of the time it takes to create a part is a result of a relatively slow cooling process.
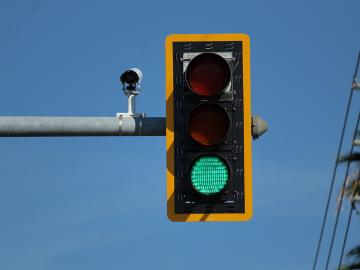
Pairing hybrid neural network modeling techniques with artificial intelligence, or AI, controls has resulted in a unique hybrid system that creates a smart solution for traffic-signal timing.
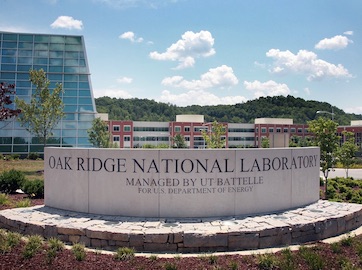
This technology combines 3D printing and compression molding to produce high-strength, low-porosity composite articles.