Filter Results
Related Organization
- Biological and Environmental Systems Science Directorate (26)
- Computing and Computational Sciences Directorate (38)
- Energy Science and Technology Directorate (223)
- Fusion and Fission Energy and Science Directorate (24)
- Information Technology Services Directorate (3)
- Isotope Science and Enrichment Directorate (7)
- National Security Sciences Directorate (20)
- Neutron Sciences Directorate (11)
- Physical Sciences Directorate (135)
- User Facilities (27)
Researcher
- Chris Tyler
- Justin West
- Ritin Mathews
- Chad Steed
- David Olvera Trejo
- J.R. R Matheson
- Jaydeep Karandikar
- Junghoon Chae
- Scott Smith
- Travis Humble
- Akash Jag Prasad
- Annetta Burger
- Brian Gibson
- Brian Post
- Calen Kimmell
- Carter Christopher
- Chance C Brown
- Debraj De
- Derek Splitter
- Emma Betters
- Gautam Malviya Thakur
- Greg Corson
- Gurneesh Jatana
- James Gaboardi
- James Szybist
- Jesse Heineman
- Jesse McGaha
- John Potter
- Josh B Harbin
- Kevin Sparks
- Liz McBride
- Samudra Dasgupta
- Todd Thomas
- Tony L Schmitz
- Vladimir Orlyanchik
- Xiuling Nie
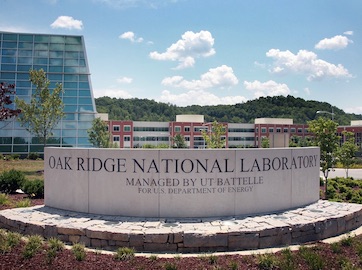
Often there are major challenges in developing diverse and complex human mobility metrics systematically and quickly.
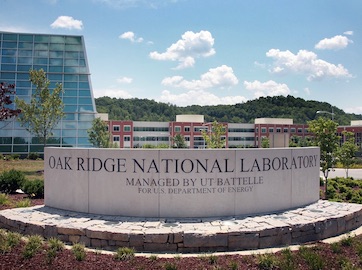
Method to operate a compression ignition engine in dual fuel operation with premixed turbulent flame propagation from low to high loads.
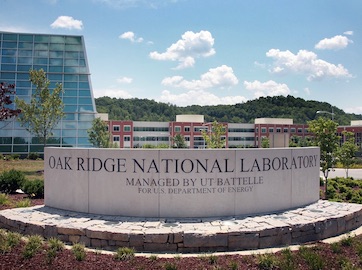
System and method for part porosity monitoring of additively manufactured components using machining
In additive manufacturing, choice of process parameters for a given material and geometry can result in porosities in the build volume, which can result in scrap.
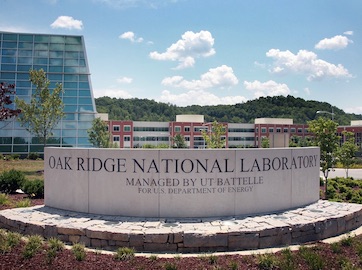
Distortion generated during additive manufacturing of metallic components affect the build as well as the baseplate geometries. These distortions are significant enough to disqualify components for functional purposes.
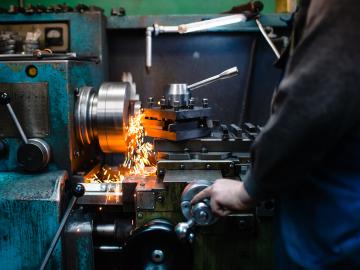
For additive manufacturing of large-scale parts, significant distortion can result from residual stresses during deposition and cooling. This can result in part scraps if the final part geometry is not contained in the additively manufactured preform.
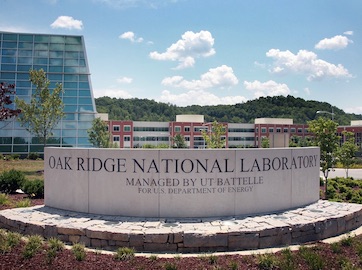
The QVis Quantum Device Circuit Optimization Module gives users the ability to map a circuit to a specific quantum devices based on the device specifications.
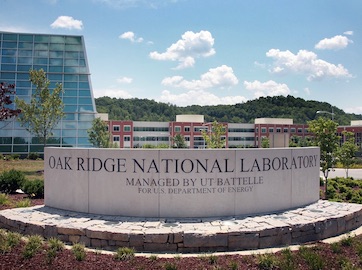
QVis is a visual analytics tool that helps uncover temporal and multivariate variations in noise properties of quantum devices.
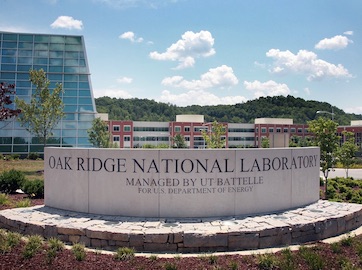
In additive manufacturing large stresses are induced in the build plate and part interface. A result of these stresses are deformations in the build plate and final component.
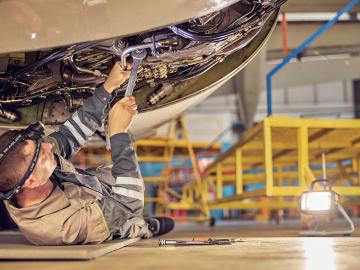
Materials produced via additive manufacturing, or 3D printing, can experience significant residual stress, distortion and cracking, negatively impacting the manufacturing process.