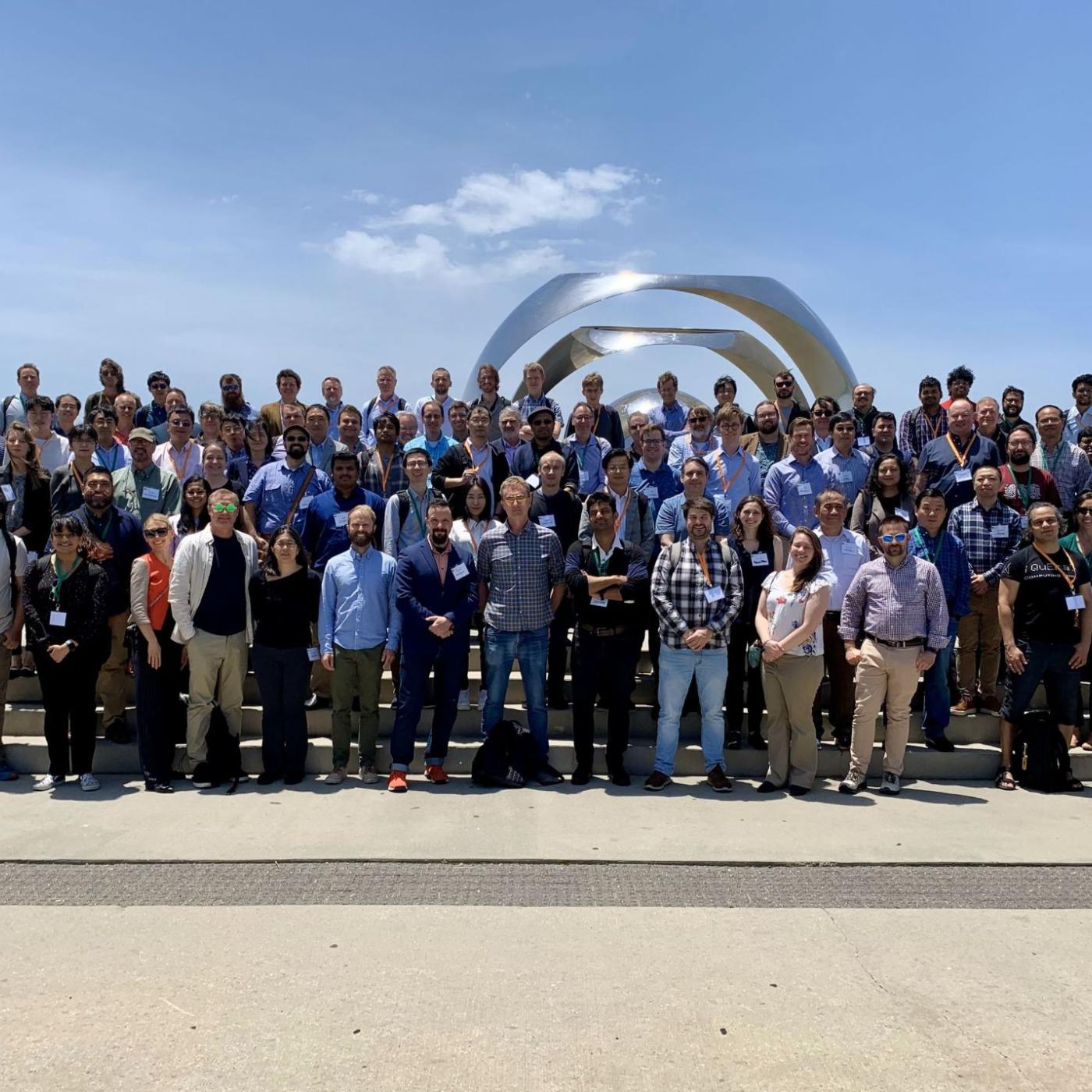
Filter News
Area of Research
News Topics
- (-) Composites (35)
- (-) Space Exploration (26)
- 3-D Printing/Advanced Manufacturing (146)
- Advanced Reactors (40)
- Artificial Intelligence (129)
- Big Data (78)
- Bioenergy (111)
- Biology (128)
- Biomedical (73)
- Biotechnology (38)
- Buildings (74)
- Chemical Sciences (85)
- Clean Water (33)
- Computer Science (226)
- Coronavirus (48)
- Critical Materials (29)
- Cybersecurity (35)
- Education (5)
- Element Discovery (1)
- Emergency (4)
- Energy Storage (114)
- Environment (218)
- Exascale Computing (67)
- Fossil Energy (8)
- Frontier (64)
- Fusion (66)
- Grid (74)
- High-Performance Computing (130)
- Hydropower (12)
- Irradiation (3)
- Isotopes (62)
- ITER (9)
- Machine Learning (67)
- Materials (157)
- Materials Science (158)
- Mathematics (12)
- Mercury (12)
- Microelectronics (4)
- Microscopy (56)
- Molten Salt (10)
- Nanotechnology (64)
- National Security (86)
- Neutron Science (171)
- Nuclear Energy (122)
- Partnerships (67)
- Physics (69)
- Polymers (35)
- Quantum Computing (53)
- Quantum Science (92)
- Security (31)
- Simulation (64)
- Software (1)
- Statistics (4)
- Summit (70)
- Transportation (102)
Media Contacts
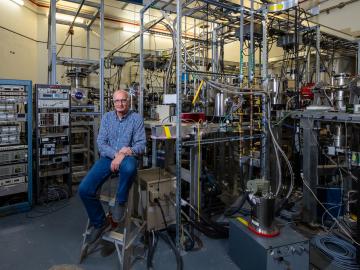
Scientists are using Oak Ridge National Laboratory’s Multicharged Ion Research Facility to simulate the cosmic origin of X-ray emissions resulting when highly charged ions collide with neutral atoms and molecules, such as helium and gaseous hydrogen.
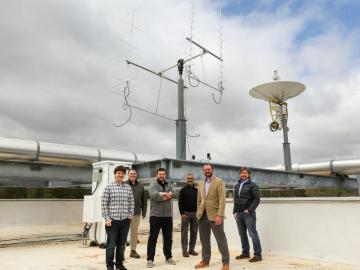
Oak Ridge National Laboratory is debuting a small satellite ground station that uses high-performance computing to support automated detection of changes to Earth’s landscape.
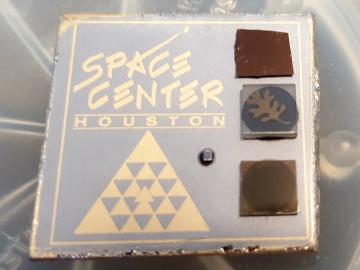
To study how space radiation affects materials for spacecraft and satellites, Oak Ridge National Laboratory scientists sent samples to the International Space Station. The results will inform design of radiation-resistant magnetic and electronic systems.
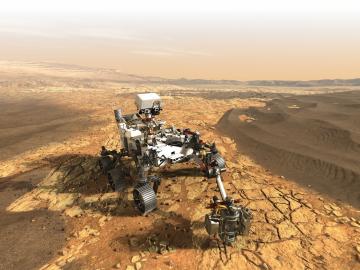
More than 50 current employees and recent retirees from ORNL received Department of Energy Secretary’s Honor Awards from Secretary Jennifer Granholm in January as part of project teams spanning the national laboratory system. The annual awards recognized 21 teams and three individuals for service and contributions to DOE’s mission and to the benefit of the nation.
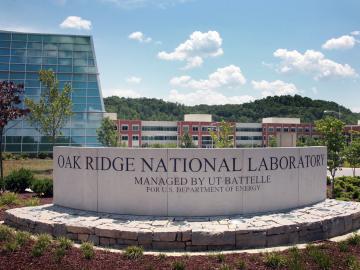
Ten scientists from the Department of Energy’s Oak Ridge National Laboratory are among the world’s most highly cited researchers, according to a bibliometric analysis conducted by the scientific publication analytics firm Clarivate.

Researchers at ORNL designed a novel polymer to bind and strengthen silica sand for binder jet additive manufacturing, a 3D-printing method used by industries for prototyping and part production.
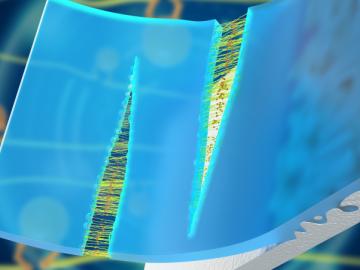
Research teams from the Department of Energy’s Oak Ridge National Laboratory and their technologies have received seven 2021 R&D 100 Awards, plus special recognition for a COVID-19-related project.

A research team at Oak Ridge National Laboratory have 3D printed a thermal protection shield, or TPS, for a capsule that will launch with the Cygnus cargo spacecraft as part of the supply mission to the International Space Station.
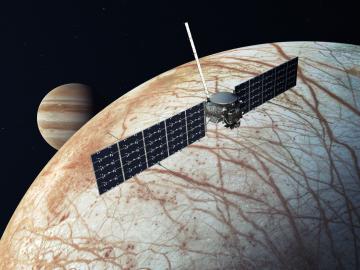
Researchers from NASA’s Jet Propulsion Laboratory and Oak Ridge National Laboratory successfully created amorphous ice, similar to ice in interstellar space and on icy worlds in our solar system. They documented that its disordered atomic behavior is unlike any ice on Earth.
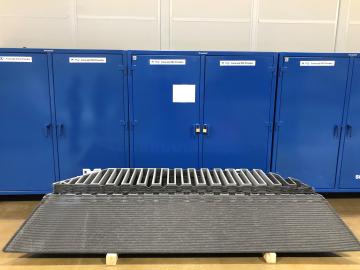
Oak Ridge National Laboratory researchers, in collaboration with Cincinnati Inc., demonstrated the potential for using multimaterials and recycled composites in large-scale applications by 3D printing a mold that replicated a single facet of a