Filter News
Area of Research
News Topics
- (-) Composites (33)
- (-) Isotopes (62)
- 3-D Printing/Advanced Manufacturing (142)
- Advanced Reactors (40)
- Artificial Intelligence (124)
- Big Data (77)
- Bioenergy (110)
- Biology (126)
- Biomedical (73)
- Biotechnology (37)
- Buildings (73)
- Chemical Sciences (84)
- Clean Water (32)
- Computer Science (223)
- Coronavirus (48)
- Critical Materials (29)
- Cybersecurity (35)
- Education (5)
- Element Discovery (1)
- Emergency (4)
- Energy Storage (114)
- Environment (217)
- Exascale Computing (64)
- Fossil Energy (8)
- Frontier (62)
- Fusion (65)
- Grid (74)
- High-Performance Computing (128)
- Hydropower (12)
- Irradiation (3)
- ITER (9)
- Machine Learning (67)
- Materials (156)
- Materials Science (155)
- Mathematics (12)
- Mercury (12)
- Microelectronics (4)
- Microscopy (56)
- Molten Salt (10)
- Nanotechnology (62)
- National Security (85)
- Neutron Science (169)
- Nuclear Energy (121)
- Partnerships (66)
- Physics (68)
- Polymers (34)
- Quantum Computing (52)
- Quantum Science (88)
- Security (30)
- Simulation (64)
- Software (1)
- Space Exploration (26)
- Statistics (4)
- Summit (70)
- Transportation (102)
Media Contacts
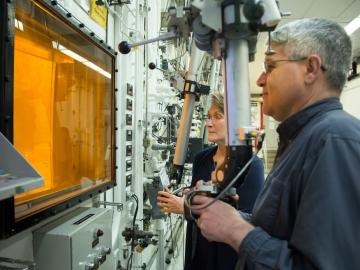
The Department of Energy’s Oak Ridge National Laboratory is now producing actinium-227 (Ac-227) to meet projected demand for a highly effective cancer drug through a 10-year contract between the U.S. DOE Isotope Program and Bayer.
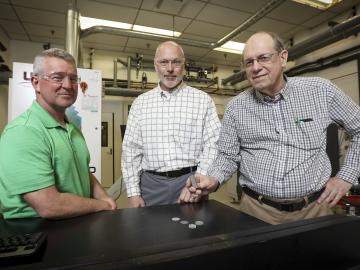
“Made in the USA.” That can now be said of the radioactive isotope molybdenum-99 (Mo-99), last made in the United States in the late 1980s. Its short-lived decay product, technetium-99m (Tc-99m), is the most widely used radioisotope in medical diagnostic imaging. Tc-99m is best known ...
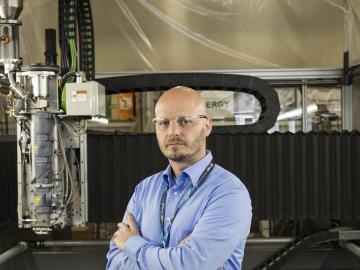
Vlastimil Kunc grew up in a family of scientists where his natural curiosity was encouraged—an experience that continues to drive his research today in polymer composite additive manufacturing at Oak Ridge National Laboratory. “I’ve been interested in the science of composites si...
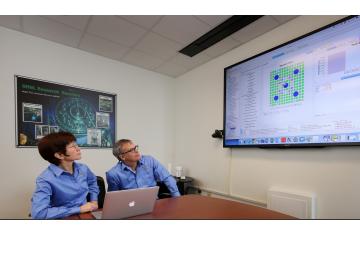
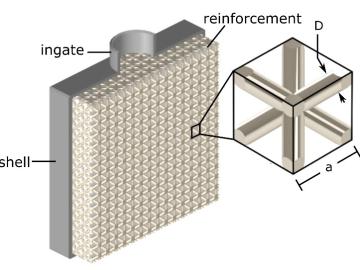
A new manufacturing method created by Oak Ridge National Laboratory and Rice University combines 3D printing with traditional casting to produce damage-tolerant components composed of multiple materials. Composite components made by pouring an aluminum alloy over a printed steel lattice showed an order of magnitude greater damage tolerance than aluminum alone.