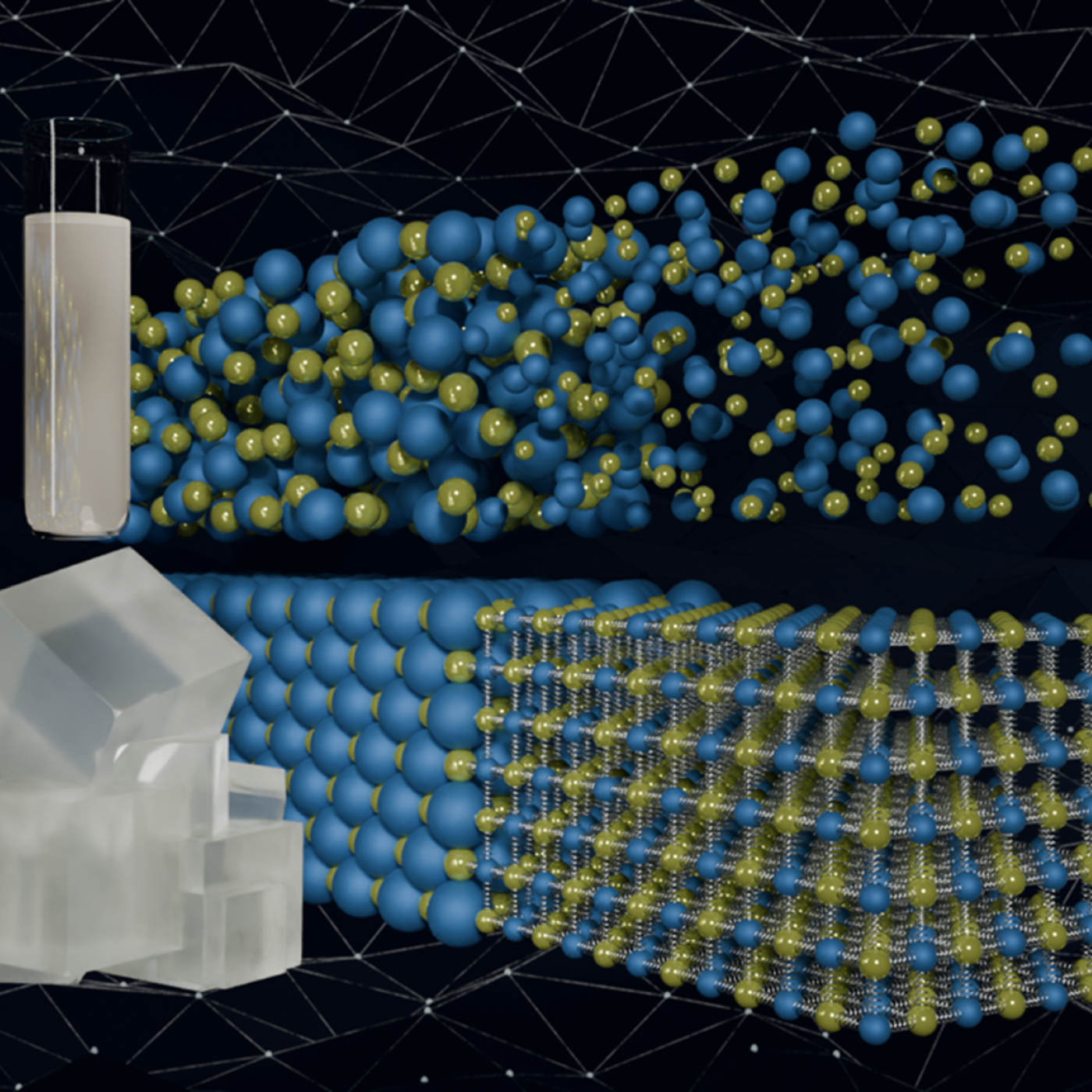
Filter News
Area of Research
- (-) Advanced Manufacturing (14)
- (-) Supercomputing (12)
- Biology and Environment (16)
- Building Technologies (1)
- Computational Engineering (1)
- Energy Science (100)
- Fusion and Fission (18)
- Fusion Energy (9)
- Isotopes (20)
- Materials (39)
- Materials for Computing (5)
- Mathematics (1)
- National Security (12)
- Neutron Science (8)
- Nuclear Science and Technology (27)
- Nuclear Systems Modeling, Simulation and Validation (1)
- Quantum information Science (1)
- Transportation Systems (2)
News Type
News Topics
- (-) 3-D Printing/Advanced Manufacturing (16)
- (-) Cybersecurity (2)
- (-) Isotopes (1)
- (-) Nuclear Energy (4)
- (-) Transportation (4)
- Advanced Reactors (2)
- Artificial Intelligence (23)
- Big Data (20)
- Bioenergy (3)
- Biology (7)
- Biomedical (11)
- Biotechnology (1)
- Buildings (2)
- Chemical Sciences (2)
- Composites (3)
- Computer Science (62)
- Coronavirus (9)
- Critical Materials (3)
- Energy Storage (2)
- Environment (18)
- Exascale Computing (17)
- Frontier (18)
- Fusion (2)
- Grid (1)
- High-Performance Computing (28)
- Machine Learning (9)
- Materials (11)
- Materials Science (14)
- Mathematics (2)
- Microscopy (2)
- Nanotechnology (6)
- National Security (3)
- Neutron Science (8)
- Physics (4)
- Polymers (2)
- Quantum Computing (15)
- Quantum Science (14)
- Security (2)
- Simulation (13)
- Software (1)
- Space Exploration (3)
- Summit (28)
Media Contacts
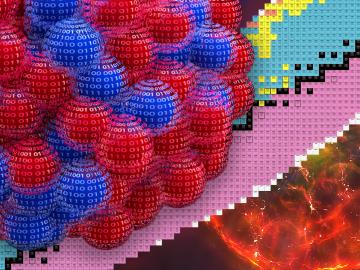
Nuclear physicists at the Department of Energy’s Oak Ridge National Laboratory recently used Frontier, the world’s most powerful supercomputer, to calculate the magnetic properties of calcium-48’s atomic nucleus.
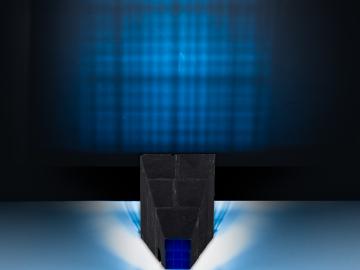
Scientists at ORNL have developed 3-D-printed collimator techniques that can be used to custom design collimators that better filter out noise during different types of neutron scattering experiments
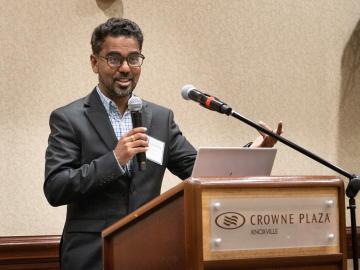
The Department of Energy’s Oak Ridge National Laboratory hosted its Smoky Mountains Computational Science and Engineering Conference for the first time in person since the COVID pandemic broke in 2020. The conference, which celebrated its 20th consecutive year, took place at the Crowne Plaza Hotel in downtown Knoxville, Tenn., in late August.
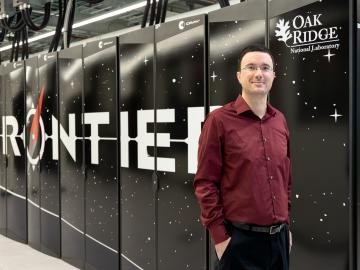
The Exascale Small Modular Reactor effort, or ExaSMR, is a software stack developed over seven years under the Department of Energy’s Exascale Computing Project to produce the highest-resolution simulations of nuclear reactor systems to date. Now, ExaSMR has been nominated for a 2023 Gordon Bell Prize by the Association for Computing Machinery and is one of six finalists for the annual award, which honors outstanding achievements in high-performance computing from a variety of scientific domains.
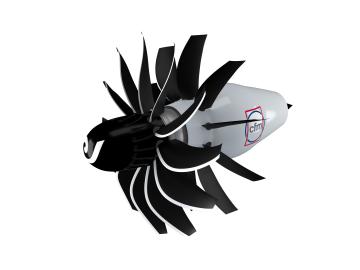
To support the development of a revolutionary new open fan engine architecture for the future of flight, GE Aerospace has run simulations using the world’s fastest supercomputer capable of crunching data in excess of exascale speed, or more than a quintillion calculations per second.
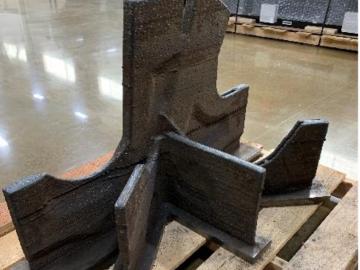
Oak Ridge National Laboratory researchers recently used large-scale additive manufacturing with metal to produce a full-strength steel component for a wind turbine, proving the technique as a viable alternative to
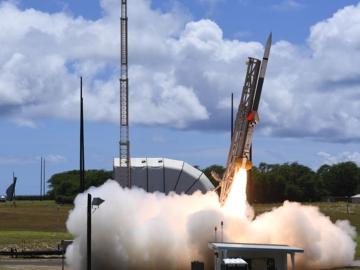
Oak Ridge National Laboratory researchers have developed a novel process to manufacture extreme heat resistant carbon-carbon composites. The performance of these materials will be tested in a U.S. Navy rocket that NASA will launch this fall.
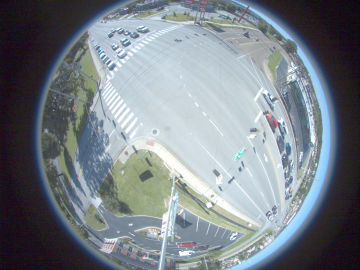
The daily traffic congestion along the streets and interstate lanes of Chattanooga could be headed the way of the horse and buggy with help from ORNL researchers.

A research team at Oak Ridge National Laboratory have 3D printed a thermal protection shield, or TPS, for a capsule that will launch with the Cygnus cargo spacecraft as part of the supply mission to the International Space Station.

Oak Ridge National Laboratory researchers combined additive manufacturing with conventional compression molding to produce high-performance thermoplastic composites reinforced with short carbon fibers.