When U.S. industries need to research, test, troubleshoot and perfect an innovation before it reaches the marketplace, many turn to DOE’s applied science user facilities at ORNL.
Sponsored by DOE’s Office of Energy Efficiency and Renewable Energy, the Manufacturing Demonstration Facility, Carbon Fiber Technology Facility, Building Technologies Research and Integration Center, and National Transportation Research Center provide private industry as well as universities and other laboratories access to the capabilities and expertise necessary to quickly move new technologies from research and demonstration to deployment in support of national priorities such as decarbonization.
These facilities foster place-based innovation, applying ORNL’s resources to address community needs, fuel regional innovation hubs and spur economic development and job growth. Industries partner with user facilities through technical collaborations and cooperative R&D agreements, or CRADAs.
To date, these facilities have enabled more than 140 patented technologies and collaborated with more than 700 industrial partners, universities and laboratories.
Many of these technologies have been licensed by some of the nation’s largest companies, including GE, Cummins, ExOne and Zeiss. Small and newly established companies also work with the user facilities, collaborating on-site and alongside ORNL researchers.
Economic impact
“What makes a facility like the Manufacturing Demonstration Facility, or MDF, unique is that we colocate our scientists and support staff with users, which allows them to work together while accessing multiple disciplines all integrated under one roof,” said Xin Sun, associate laboratory director for ORNL’s Energy Science and Technology Directorate..
Sun said this type of model not only gets products to the marketplace faster, but also trains, educates and guides workforce development and enables next-generation technologies.
“We form strategic partnerships with equipment managers, for example, so that we can have national impact,” she added. “The MDF’s partnerships alone have had about a billion-dollar impact on U.S. manufacturing and enabled many startups.”
In 2018, when Knoxville, Tennessee-based entrepreneur Jonaaron Jones opened Volunteer Aerospace’s headquarters in the Hardin Valley area about a 15-minute drive from ORNL’s main campus, he made sure the growing company was located near the MDF.
Jones worked with the facility while he was an MDF research engineer, investigating the use of a powder bed additive manufacturing process to produce parts and products for the aerospace and defense industries. He spent four years fine-tuning that process and says the MDF served as an incubator for his company.
In just under three years, Jones was able to grow the company to seven employees, adding five additive systems capable of fabricating components. One of the first machines Volunteer Aerospace began working with was the original Concept Laser, a machine that Jones became familiar with while at the MDF. He noted that having access to ORNL research expertise enabled his company’s rapid expansion, something that would not have been possible without the support of the MDF. Volunteer Aerospace’s growth ultimately led to a company acquisition in late 2021 by Florida-based additive solutions provider Beehive 3D, Inc.
Meeting the challenge
Making the seemingly impossible a reality is what researchers at these user facilities thrive on. Early in the COVID-19 pandemic in 2020, researchers from the MDF collaborated with ORNL's Carbon Fiber Technology Facility, or CFTF, and industry partner Cummins on ways to produce filter media for N95 masks.
Merlin Theodore, ORNL’s Advanced Fibers Manufacturing Group leader, converted the CFTF’s melt blowing capability to the production of polypropylene. Polypropylene is a nonwoven material that is permanently electrostatically charged, with millions of microfibers layered on top of each other to filter out virus particles smaller than a millionth of a meter.
Theodore transferred the capability to Cummins, an engine and power generation manufacturer, so that the company could convert its own melt blowing line into producing N95 filter material. The company ultimately made enough filter media to supply a million masks a day.
“We knew melt blowing, but we could not have gotten up to speed without the interactions with ORNL,” said Christopher Holm, Cummins’ director of filter media technology. “Their technical guidance helped us become operational in a short amount of time so that we could meet the demand and supply our customers with material during a time of crisis.”
Said Theodore: “Our goal is to transfer our technology to industry partners to increase U.S. competitiveness in manufacturing. This also supplies a critical need for our country, creates job growth and stimulates the economy. We are the catalyst that helps industry bring technology to the consumer.”
As the pandemic progressed and COVID-19 vaccines became available, Carrier Global Corporation needed to figure out how to keep them properly stored and refrigerated when being transported to rural and remote areas. To solve the challenge, the refrigerant manufacturing expert consulted with researchers within DOE’s Building Technologies Research and Integration Center, or BTRIC, at ORNL.
Carrier and ORNL retrofitted a commercial storage container on the BTRIC campus, where they conducted experiments to determine the lowest temperature that could be maintained for the longest period. Six months of testing determined that an all-electric unit container could provide precise temperature control at the minus-30-to-35-degree range necessary for COVID-19 vaccines. By optimizing package placements within the container to hold 20 polystyrene foam packages, each with around 5,000 doses, one container could transport 100,000 refrigerated doses of vaccine.
“By collaborating with BTRIC at ORNL, we have been able to validate our mobile cold storage solution that can support COVID-19 vaccine distribution,” said Nader Awwad, Carrier’s director of engineering.
“This project is an example of how the scientific creativity and resources of a national user facility and coordination with industry can lead to meeting the needs of our nation during a critical period,” said Melissa Lapsa, ORNL’s building technologies program manager. “Our researchers recognized the urgency of Carrier’s need and brought the appropriate resources together so that we could quickly deliver solutions.”
Powerful collaboration
Working with industry leaders like Carrier is part of the day-to-day operations of the national user facilities. In recent years, the National Transportation Research Center, or NTRC, partnered with another global brand, ExxonMobil, to operate a one-of-a-kind experimental engine that would enable the development of next-generation lubricants for the marine industry.
Exxon installed a custom-built, one-tenth-scale marine diesel engine called the Enterprise at the NTRC. At 12 feet tall and weighing more than 16,000 pounds, the flexible-fuel, single-cylinder engine has a rated speed of 625 rpm to match the speed of a full-scale engine. Overall, the ORNL and Exxon collaboration informed the production of a new suite of low-sulfur fuels, known as EMF.5, that adhere to sulfur-compliant marine fuel specifications.
“ExxonMobil came to ORNL because we know fuels and emissions, and we know engines,” said Robert Wagner, director of ORNL’s Buildings and Transportation Science Division. “The NTRC user facility allowed Exxon to perform controlled engine-based experiments, filling the gap between bench-scale and full-engine tests. This one collaboration helped develop Exxon’s whole research strategy for the development of next-generation lubricants.”
“This engine is a dream come true,” said John Fogarty, research team lead for ExxonMobil. “We wanted to put our engine here to have the expertise Oak Ridge provided.”
Industry partnerships also feed an innovation ecosystem — something that is uniquely suited to national user facilities. More than 5,000 companies have visited MDF alone, resulting in more than 180 collaborative research projects. Each collaboration helps shape a future vision for U.S. industry based on the problems and needs discovered through core scientific research and development. Ultimately, innovation cultivated within a user facility can lead to workforce development initiatives, not only creating jobs but also helping to shape the next generation of innovators.
Within advanced manufacturing, specifically, Sun noted that the MDF aims to develop technology faster than the competition can copy.
“We have close to a hundred manufacturing systems installed at the MDF, and these all support the production of energy-efficient products with benefits extending across the nation’s economy. We’re creating and driving a system of innovation,” she said.
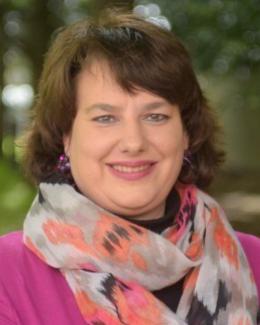