Filter Results
Related Organization
- Biological and Environmental Systems Science Directorate (23)
- Computing and Computational Sciences Directorate (35)
- Energy Science and Technology Directorate (217)
- Fusion and Fission Energy and Science Directorate (21)
- Information Technology Services Directorate (2)
- Isotope Science and Enrichment Directorate (6)
- National Security Sciences Directorate (17)
- Neutron Sciences Directorate (11)
- Physical Sciences Directorate
(128)
- User Facilities (27)
Researcher
- Adam Willoughby
- Mingyan Li
- Rishi Pillai
- Sam Hollifield
- Vincent Paquit
- Akash Jag Prasad
- Brandon Johnston
- Brian Weber
- Bruce A Pint
- Calen Kimmell
- Canhai Lai
- Charles Hawkins
- Chris Tyler
- Clay Leach
- Costas Tsouris
- Isaac Sikkema
- James Haley
- James Parks II
- Jaydeep Karandikar
- Jiheon Jun
- Joseph Olatt
- Kevin Spakes
- Kunal Mondal
- Lilian V Swann
- Luke Koch
- Mahim Mathur
- Marie Romedenne
- Mary A Adkisson
- Oscar Martinez
- Priyanshi Agrawal
- Ryan Dehoff
- T Oesch
- Vladimir Orlyanchik
- Yong Chae Lim
- Zackary Snow
- Zhili Feng
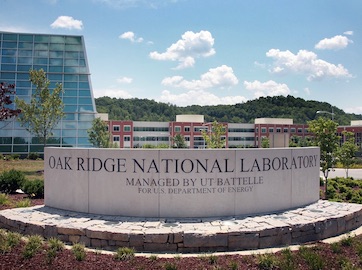
System and method for part porosity monitoring of additively manufactured components using machining
In additive manufacturing, choice of process parameters for a given material and geometry can result in porosities in the build volume, which can result in scrap.
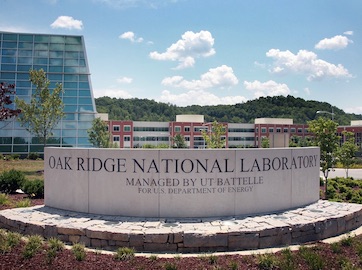
A novel method that prevents detachment of an optical fiber from a metal/alloy tube and allows strain measurement up to higher temperatures, about 800 C has been developed. Standard commercial adhesives typically only survive up to about 400 C.
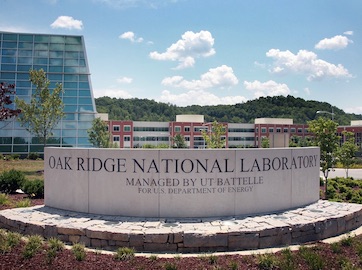
Test facilities to evaluate materials compatibility in hydrogen are abundant for high pressure and low temperature (<100C).
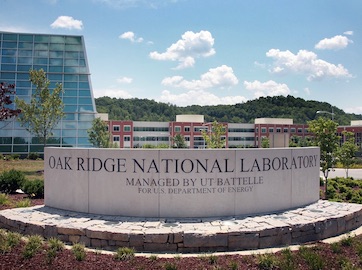
Sensing of additive manufacturing processes promises to facilitate detailed quality inspection at scales that have seldom been seen in traditional manufacturing processes.
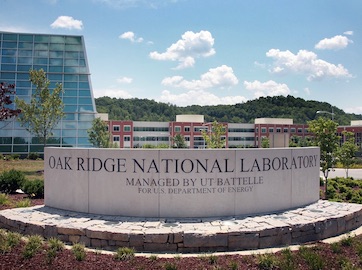
The technologies provide a coating method to produce corrosion resistant and electrically conductive coating layer on metallic bipolar plates for hydrogen fuel cell and hydrogen electrolyzer applications.

Real-time tracking and monitoring of radioactive/nuclear materials during transportation is a critical need to ensure safety and security. Current technologies rely on simple tagging, using sensors attached to transport containers, but they have limitations.
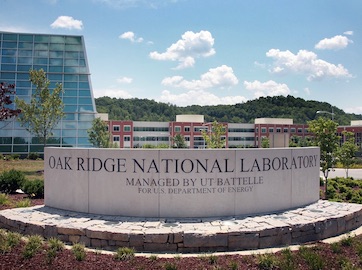
The technology provides a transformational approach to digitally manufacture structural alloys with co- optimized strength and environmental resistance