Filter Results
Related Organization
- Biological and Environmental Systems Science Directorate (23)
- Computing and Computational Sciences Directorate (35)
- Energy Science and Technology Directorate (217)
- Fusion and Fission Energy and Science Directorate (21)
- Information Technology Services Directorate (2)
- Isotope Science and Enrichment Directorate (6)
- National Security Sciences Directorate (17)
- Neutron Sciences Directorate (11)
- Physical Sciences Directorate
(128)
- User Facilities (27)
Researcher
- Sheng Dai
- Parans Paranthaman
- Bishnu Prasad Thapaliya
- Zhenzhen Yang
- Craig A Bridges
- Shannon M Mahurin
- Ying Yang
- Adam Willoughby
- Bruce A Pint
- Edgar Lara-Curzio
- Ilja Popovs
- Li-Qi Qiu
- Rishi Pillai
- Ryan Dehoff
- Saurabh Prakash Pethe
- Steven J Zinkle
- Tolga Aytug
- Uday Vaidya
- Vincent Paquit
- Yanli Wang
- Yutai Kato
- Ahmed Hassen
- Akash Jag Prasad
- Alexei P Sokolov
- Alice Perrin
- Anees Alnajjar
- Ben Lamm
- Beth L Armstrong
- Brandon Johnston
- Bruce Moyer
- Calen Kimmell
- Canhai Lai
- Charles Hawkins
- Christopher Ledford
- Chris Tyler
- Clay Leach
- Costas Tsouris
- Eric Wolfe
- Frederic Vautard
- James Haley
- James Parks II
- Jayanthi Kumar
- Jaydeep Karandikar
- Jiheon Jun
- Kaustubh Mungale
- Marie Romedenne
- Meghan Lamm
- Michael Kirka
- Nageswara Rao
- Nidia Gallego
- Patxi Fernandez-Zelaia
- Phillip Halstenberg
- Priyanshi Agrawal
- Santa Jansone-Popova
- Shajjad Chowdhury
- Subhamay Pramanik
- Tao Hong
- Tim Graening Seibert
- Tomonori Saito
- Vladimir Orlyanchik
- Vlastimil Kunc
- Weicheng Zhong
- Wei Tang
- Xiang Chen
- Yan-Ru Lin
- Yong Chae Lim
- Zackary Snow
- Zhili Feng
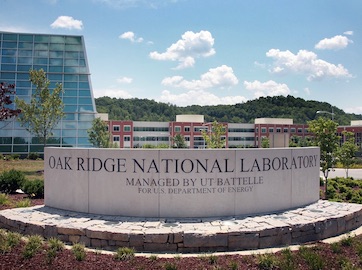
A novel strategy was developed to solve the limitations of the current sorbent systems in CO2 chemisorption in terms of energy consumption in CO2 release and improved CO2 uptake capacity.
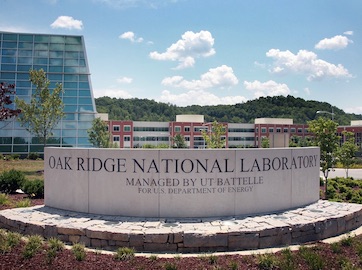
This invention introduces a novel sintering approach to produce hard carbon with a finely tuned microstructure, derived from biomass and plastic waste.
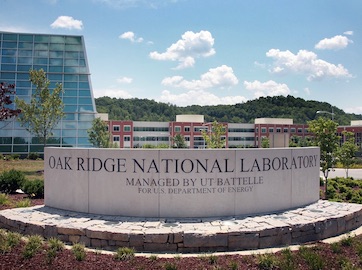
System and method for part porosity monitoring of additively manufactured components using machining
In additive manufacturing, choice of process parameters for a given material and geometry can result in porosities in the build volume, which can result in scrap.
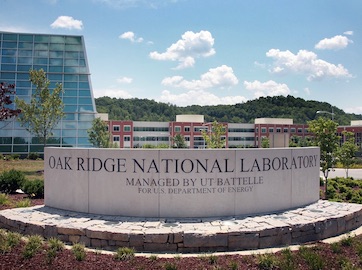
V-Cr-Ti alloys have been proposed as candidate structural materials in fusion reactor blanket concepts with operation temperatures greater than that for reduced activation ferritic martensitic steels (RAFMs).
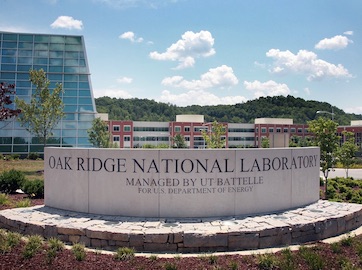
A novel method that prevents detachment of an optical fiber from a metal/alloy tube and allows strain measurement up to higher temperatures, about 800 C has been developed. Standard commercial adhesives typically only survive up to about 400 C.
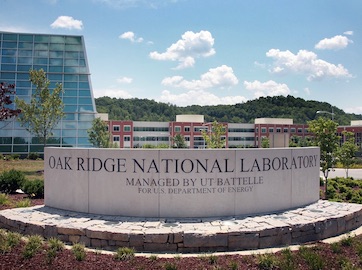
The increasing demand for high-purity lanthanides, essential for advanced technologies such as electronics, renewable energy, and medical applications, presents a significant challenge due to their similar chemical properties.
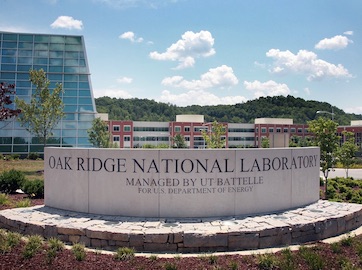
With the ever-growing reliance on batteries, the need for the chemicals and materials to produce these batteries is also growing accordingly. One area of critical concern is the need for high quality graphite to ensure adequate energy storage capacity and battery stability.
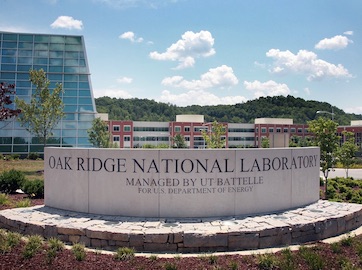
Test facilities to evaluate materials compatibility in hydrogen are abundant for high pressure and low temperature (<100C).
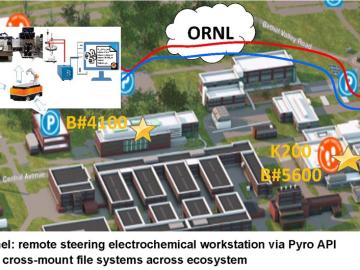
Electrochemistry synthesis and characterization testing typically occurs manually at a research facility.
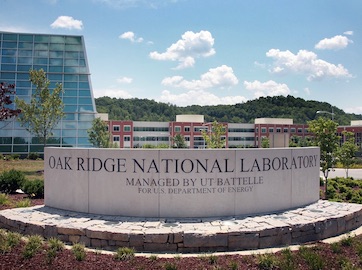
Sensing of additive manufacturing processes promises to facilitate detailed quality inspection at scales that have seldom been seen in traditional manufacturing processes.