Filter Results
Related Organization
- Biological and Environmental Systems Science Directorate (23)
- Computing and Computational Sciences Directorate (35)
- Energy Science and Technology Directorate (217)
- Fusion and Fission Energy and Science Directorate (21)
- Information Technology Services Directorate (2)
- Isotope Science and Enrichment Directorate (6)
- National Security Sciences Directorate (17)
- Neutron Sciences Directorate (11)
- Physical Sciences Directorate
(128)
- User Facilities (27)
Researcher
- Brian Post
- Chris Tyler
- Radu Custelcean
- Justin West
- Peter Wang
- Costas Tsouris
- Ritin Mathews
- Andrzej Nycz
- Blane Fillingim
- Chris Masuo
- Gyoung Gug Jang
- Jeffrey Einkauf
- Sudarsanam Babu
- Thomas Feldhausen
- Ahmed Hassen
- Benjamin L Doughty
- Bruce Moyer
- David Olvera Trejo
- Gs Jung
- J.R. R Matheson
- Jaydeep Karandikar
- Joshua Vaughan
- Lauren Heinrich
- Nikki Thiele
- Peeyush Nandwana
- Santa Jansone-Popova
- Scott Smith
- Yousub Lee
- Adam Stevens
- Akash Jag Prasad
- Alexander I Wiechert
- Alex Roschli
- Amit Shyam
- Brian Gibson
- Calen Kimmell
- Cameron Adkins
- Christopher Fancher
- Craig Blue
- Emma Betters
- Gordon Robertson
- Greg Corson
- Ilja Popovs
- Isha Bhandari
- Jayanthi Kumar
- Jay Reynolds
- Jeff Brookins
- Jennifer M Pyles
- Jesse Heineman
- John Lindahl
- John Potter
- Jong K Keum
- Josh B Harbin
- Laetitia H Delmau
- Liam White
- Luke Meyer
- Luke Sadergaski
- Md Faizul Islam
- Michael Borish
- Mina Yoon
- Parans Paranthaman
- Rangasayee Kannan
- Roger G Miller
- Ryan Dehoff
- Santanu Roy
- Sarah Graham
- Saurabh Prakash Pethe
- Steven Guzorek
- Subhamay Pramanik
- Tony L Schmitz
- Uvinduni Premadasa
- Vera Bocharova
- Vladimir Orlyanchik
- Vlastimil Kunc
- William Carter
- William Peter
- Yingzhong Ma
- Yukinori Yamamoto
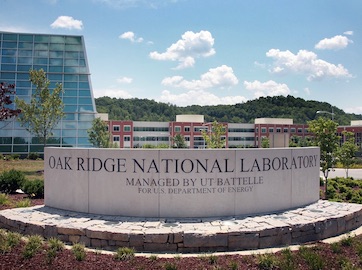
The technologies provides for regeneration of anion-exchange resin.
Contact
To learn more about this technology, email partnerships@ornl.gov or call 865-574-1051.
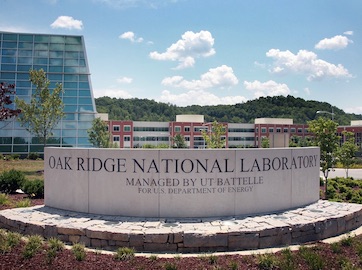
Ruthenium is recovered from used nuclear fuel in an oxidizing environment by depositing the volatile RuO4 species onto a polymeric substrate.
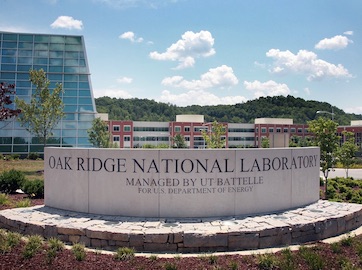
This invention describes a new class of amphiphilic chelators (extractants) that can selectively separate large, light rare earth elements from heavy, small rare earth elements in solvent extraction schemes.
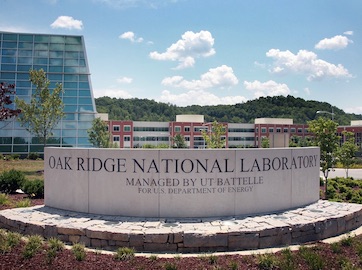
System and method for part porosity monitoring of additively manufactured components using machining
In additive manufacturing, choice of process parameters for a given material and geometry can result in porosities in the build volume, which can result in scrap.
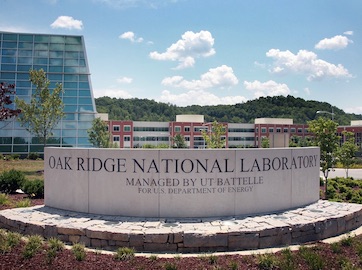
This manufacturing method uses multifunctional materials distributed volumetrically to generate a stiffness-based architecture, where continuous surfaces can be created from flat, rapidly produced geometries.
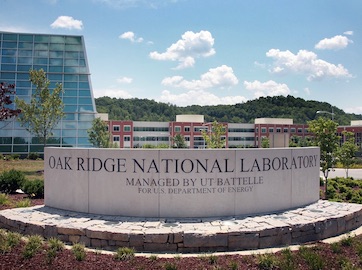
Among the methods for point source carbon capture, the absorption of CO2 using aqueous amines (namely MEA) from the post-combustion gas stream is currently considered the most promising.
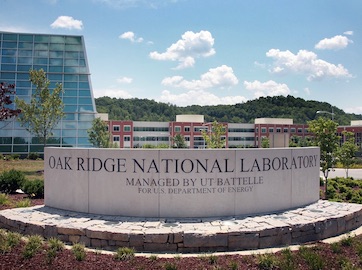
The lack of real-time insights into how materials evolve during laser powder bed fusion has limited the adoption by inhibiting part qualification. The developed approach provides key data needed to fabricate born qualified parts.
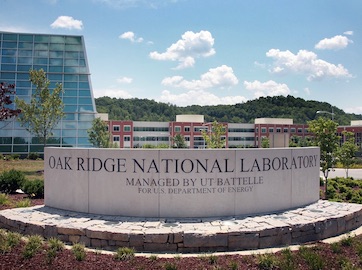
The increasing demand for high-purity lanthanides, essential for advanced technologies such as electronics, renewable energy, and medical applications, presents a significant challenge due to their similar chemical properties.
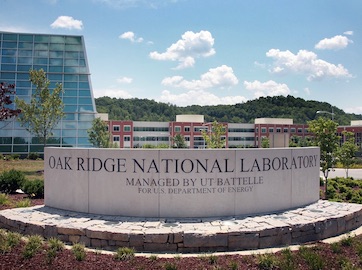
Distortion generated during additive manufacturing of metallic components affect the build as well as the baseplate geometries. These distortions are significant enough to disqualify components for functional purposes.
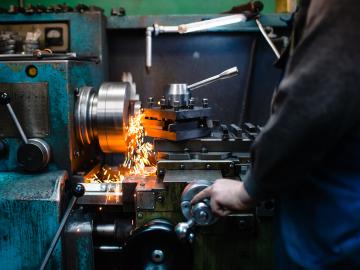
For additive manufacturing of large-scale parts, significant distortion can result from residual stresses during deposition and cooling. This can result in part scraps if the final part geometry is not contained in the additively manufactured preform.