Filter Results
Related Organization
- Biological and Environmental Systems Science Directorate (23)
- Computing and Computational Sciences Directorate (35)
- Energy Science and Technology Directorate (217)
- Fusion and Fission Energy and Science Directorate (21)
- Information Technology Services Directorate (2)
- Isotope Science and Enrichment Directorate (6)
- National Security Sciences Directorate (17)
- Neutron Sciences Directorate (11)
- Physical Sciences Directorate (128)
- User Facilities
(27)
Researcher
- Brian Post
- Peter Wang
- Andrzej Nycz
- Blane Fillingim
- Chris Masuo
- Sudarsanam Babu
- Thomas Feldhausen
- Ahmed Hassen
- J.R. R Matheson
- Joshua Vaughan
- Lauren Heinrich
- Peeyush Nandwana
- Yousub Lee
- Adam Stevens
- Alex Roschli
- Amit Shyam
- Brian Gibson
- Cameron Adkins
- Christopher Fancher
- Christopher Rouleau
- Chris Tyler
- Costas Tsouris
- Craig Blue
- David Olvera Trejo
- Diana E Hun
- Easwaran Krishnan
- Gordon Robertson
- Gs Jung
- Gyoung Gug Jang
- Ilia N Ivanov
- Isha Bhandari
- Ivan Vlassiouk
- James Manley
- Jamieson Brechtl
- Jay Reynolds
- Jeff Brookins
- Jesse Heineman
- Joe Rendall
- John Lindahl
- John Potter
- Jong K Keum
- Karen Cortes Guzman
- Kashif Nawaz
- Kuma Sumathipala
- Liam White
- Luke Meyer
- Mengjia Tang
- Michael Borish
- Mina Yoon
- Muneeshwaran Murugan
- Radu Custelcean
- Rangasayee Kannan
- Ritin Mathews
- Roger G Miller
- Ryan Dehoff
- Sarah Graham
- Scott Smith
- Steven Guzorek
- Tomonori Saito
- Vlastimil Kunc
- William Carter
- William Peter
- Yukinori Yamamoto
- Zoriana Demchuk
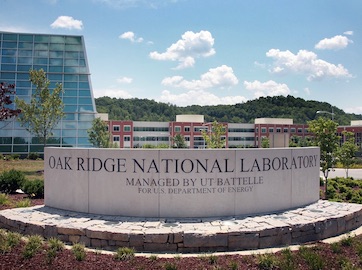
This manufacturing method uses multifunctional materials distributed volumetrically to generate a stiffness-based architecture, where continuous surfaces can be created from flat, rapidly produced geometries.
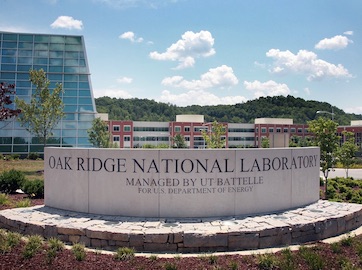
The lack of real-time insights into how materials evolve during laser powder bed fusion has limited the adoption by inhibiting part qualification. The developed approach provides key data needed to fabricate born qualified parts.
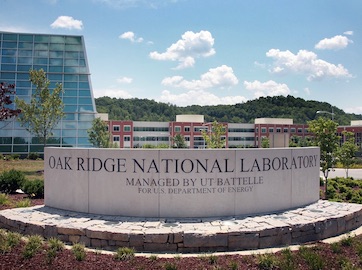
Estimates based on the U.S. Department of Energy (DOE) test procedure for water heaters indicate that the equivalent of 350 billion kWh worth of hot water is discarded annually through drains, and a large portion of this energy is, in fact, recoverable.
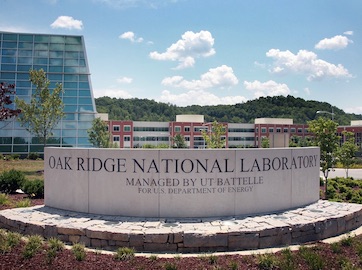
The incorporation of low embodied carbon building materials in the enclosure is increasing the fuel load for fire, increasing the demand for fire/flame retardants.
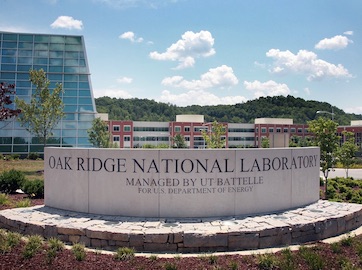
A valve solution that prevents cross contamination while allowing for blocking multiple channels at once using only one actuator.
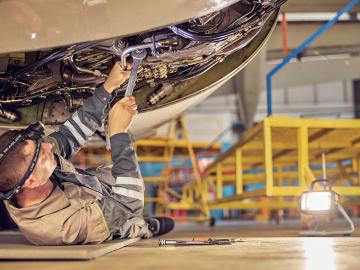
Materials produced via additive manufacturing, or 3D printing, can experience significant residual stress, distortion and cracking, negatively impacting the manufacturing process.
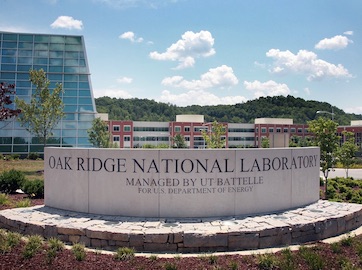
This work seeks to alter the interface condition through thermal history modification, deposition energy density, and interface surface preparation to prevent interface cracking.
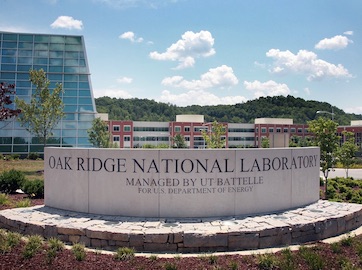
Additive manufacturing (AM) enables the incremental buildup of monolithic components with a variety of materials, and material deposition locations.
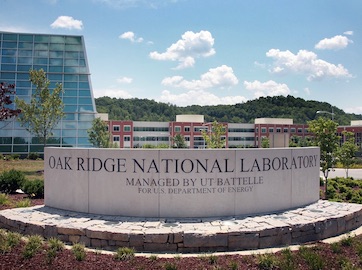
This technology is a laser-based heating unit that offers rapid heating profiles on a research scale with minimal incidental heating of materials processing environments.
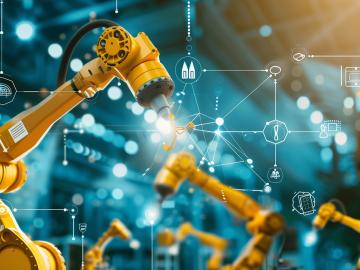
In additive printing that utilizes multiple robotic agents to build, each agent, or “arm”, is currently limited to a prescribed path determined by the user.