Filter Results
Related Organization
- Biological and Environmental Systems Science Directorate (23)
- Computing and Computational Sciences Directorate (35)
- Energy Science and Technology Directorate (217)
- Fusion and Fission Energy and Science Directorate (21)
- Information Technology Services Directorate (2)
- Isotope Science and Enrichment Directorate (6)
- National Security Sciences Directorate (17)
- Neutron Sciences Directorate (11)
- Physical Sciences Directorate (128)
- User Facilities (27)
Researcher
- Ahmed Hassen
- Vlastimil Kunc
- Soydan Ozcan
- Steven Guzorek
- Ali Passian
- Meghan Lamm
- Vipin Kumar
- Brian Post
- Halil Tekinalp
- Uday Vaidya
- Umesh N MARATHE
- David Nuttall
- Katie Copenhaver
- Alex Roschli
- Beth L Armstrong
- Dan Coughlin
- Georges Chahine
- Jim Tobin
- Matt Korey
- Pum Kim
- Segun Isaac Talabi
- Tyler Smith
- Adam Stevens
- Adwoa Owusu
- Akash Phadatare
- Amber Hubbard
- Ben Lamm
- Brittany Rodriguez
- Cait Clarkson
- Claire Marvinney
- Craig Blue
- Erin Webb
- Evin Carter
- Gabriel Veith
- Harper Jordan
- Jeremy Malmstead
- Jesse Heineman
- Joel Asiamah
- Joel Dawson
- John Lindahl
- Josh Crabtree
- Julian Charron
- Khryslyn G Araño
- Kim Sitzlar
- Kitty K Mccracken
- Komal Chawla
- Marm Dixit
- Merlin Theodore
- Nadim Hmeidat
- Nance Ericson
- Oluwafemi Oyedeji
- Paritosh Mhatre
- Ryan Ogle
- Sana Elyas
- Sanjita Wasti
- Shajjad Chowdhury
- Srikanth Yoginath
- Steve Bullock
- Subhabrata Saha
- Sudarsanam Babu
- Thomas Feldhausen
- Tolga Aytug
- Varisara Tansakul
- Xianhui Zhao
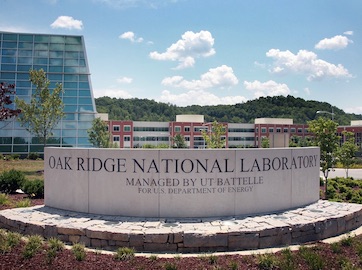
Wind turbine blades face a harsh environment in which erosion of the leading edge is a major factor for in-use maintenance. Current industrial practices to address this leading edge erosion are replacement of reinforcing materials upon significant damage infliction.
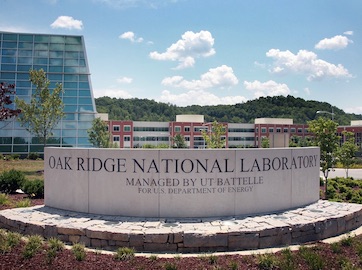
This manufacturing method uses multifunctional materials distributed volumetrically to generate a stiffness-based architecture, where continuous surfaces can be created from flat, rapidly produced geometries.
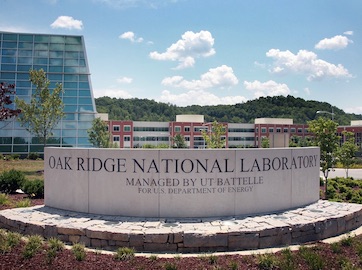
Through utilizing a two function splice we can increase the splice strength for opposing tows.
Contact:
To learn more about this technology, email partnerships@ornl.gov or call 865-574-1051.
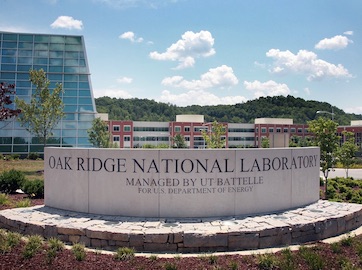
We proposed and developed a carbon nanofiber (CNF) suspension-based sizing agent, that resulted in improved interfacial, and mechanical properties. The CNF dispersed sizing agent can be applied in a relatively simpler way (by passing the continuous tow through it).
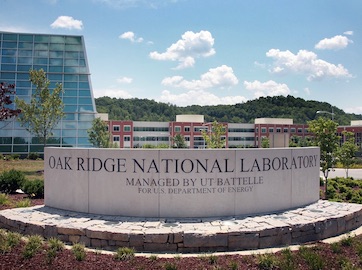
The technologies polymer cellulose nanocomposite mats and process for making same.
Contact
To learn more about this technology, email partnerships@ornl.gov or call 865-574-1051.