Filter Results
Related Organization
- Biological and Environmental Systems Science Directorate (29)
- Computing and Computational Sciences Directorate (39)
- Energy Science and Technology Directorate (229)
- Fusion and Fission Energy and Science Directorate (24)
- Information Technology Services Directorate (3)
- Isotope Science and Enrichment Directorate (7)
- National Security Sciences Directorate (20)
- Neutron Sciences Directorate (11)
- Physical Sciences Directorate (138)
- User Facilities (28)
Researcher
- Ahmed Hassen
- Vlastimil Kunc
- Chris Tyler
- Soydan Ozcan
- Steven Guzorek
- Vipin Kumar
- Brian Post
- Halil Tekinalp
- Justin West
- Meghan Lamm
- David Nuttall
- Ritin Mathews
- Uday Vaidya
- Umesh N MARATHE
- Dan Coughlin
- Katie Copenhaver
- Nadim Hmeidat
- Steve Bullock
- Tyler Smith
- Alex Roschli
- Beth L Armstrong
- Brittany Rodriguez
- David Olvera Trejo
- Georges Chahine
- J.R. R Matheson
- Jaydeep Karandikar
- Jesse Heineman
- Jim Tobin
- Matt Korey
- Pum Kim
- Sanjita Wasti
- Scott Smith
- Segun Isaac Talabi
- Subhabrata Saha
- Xianhui Zhao
- Adam Stevens
- Adwoa Owusu
- Akash Jag Prasad
- Akash Phadatare
- Amber Hubbard
- Ben Lamm
- Brian Gibson
- Cait Clarkson
- Calen Kimmell
- Craig Blue
- Emma Betters
- Erin Webb
- Evin Carter
- Gabriel Veith
- Greg Corson
- Jeremy Malmstead
- John Lindahl
- John Potter
- Josh B Harbin
- Josh Crabtree
- Julian Charron
- Khryslyn G Araño
- Kim Sitzlar
- Kitty K Mccracken
- Komal Chawla
- Marm Dixit
- Merlin Theodore
- Oluwafemi Oyedeji
- Paritosh Mhatre
- Ryan Ogle
- Sana Elyas
- Shajjad Chowdhury
- Sudarsanam Babu
- Thomas Feldhausen
- Tolga Aytug
- Tony L Schmitz
- Vladimir Orlyanchik
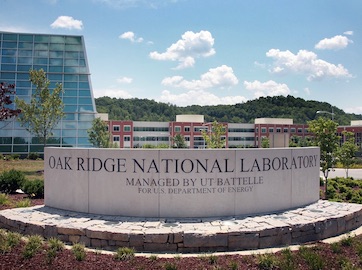
The technology will offer supportless DIW of complex structures using vinyl ester resin, facilitated by multidirectional 6 axis printing.
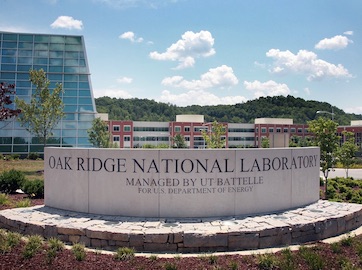
We have developed a novel extrusion-based 3D printing technique that can achieve a resolution of 0.51 mm layer thickness, and catalyst loading of 44% and 90.5% before and after drying, respectively.
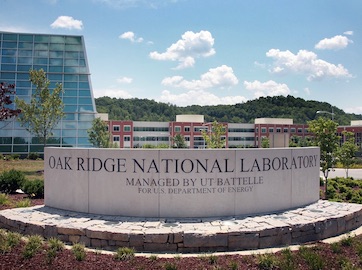
Wind turbine blades face a harsh environment in which erosion of the leading edge is a major factor for in-use maintenance. Current industrial practices to address this leading edge erosion are replacement of reinforcing materials upon significant damage infliction.
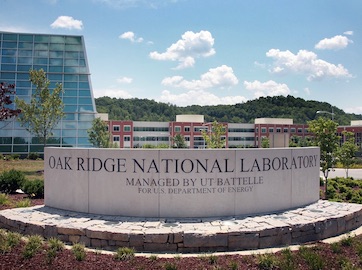
System and method for part porosity monitoring of additively manufactured components using machining
In additive manufacturing, choice of process parameters for a given material and geometry can result in porosities in the build volume, which can result in scrap.
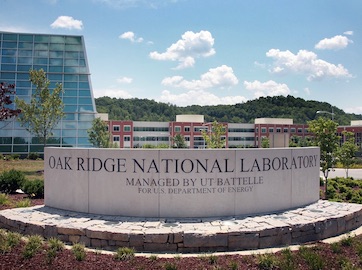
This manufacturing method uses multifunctional materials distributed volumetrically to generate a stiffness-based architecture, where continuous surfaces can be created from flat, rapidly produced geometries.
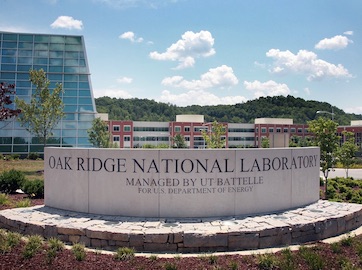
Through utilizing a two function splice we can increase the splice strength for opposing tows.
Contact:
To learn more about this technology, email partnerships@ornl.gov or call 865-574-1051.
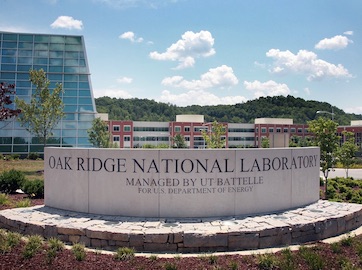
We proposed and developed a carbon nanofiber (CNF) suspension-based sizing agent, that resulted in improved interfacial, and mechanical properties. The CNF dispersed sizing agent can be applied in a relatively simpler way (by passing the continuous tow through it).
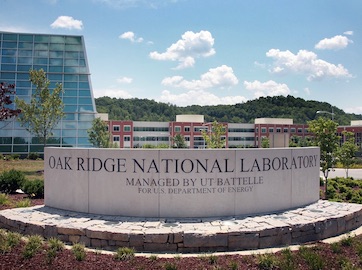
Reflective and emissive surfaces are designed with heat retention as opposed to the current state of the art oven and furnaces which use non-reflective surfaces. Heat is absorbed and transferred to the exterior of the heated appliances.
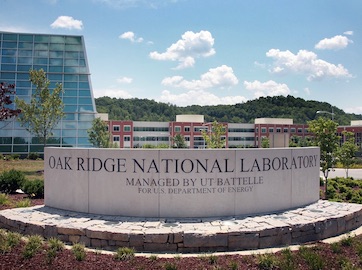
The technologies polymer cellulose nanocomposite mats and process for making same.
Contact
To learn more about this technology, email partnerships@ornl.gov or call 865-574-1051.