Filter Results
Related Organization
- Biological and Environmental Systems Science Directorate (23)
- Computing and Computational Sciences Directorate (35)
- Energy Science and Technology Directorate (217)
- Fusion and Fission Energy and Science Directorate (21)
- Information Technology Services Directorate (2)
- Isotope Science and Enrichment Directorate (6)
- National Security Sciences Directorate (17)
- Neutron Sciences Directorate (11)
- Physical Sciences Directorate (128)
- User Facilities (27)
Researcher
- Brian Post
- Chris Tyler
- Andrzej Nycz
- Justin West
- Peter Wang
- Chris Masuo
- Ritin Mathews
- Blane Fillingim
- Sudarsanam Babu
- Thomas Feldhausen
- Ahmed Hassen
- David Olvera Trejo
- J.R. R Matheson
- Jaydeep Karandikar
- Joshua Vaughan
- Kuntal De
- Lauren Heinrich
- Peeyush Nandwana
- Scott Smith
- Udaya C Kalluri
- Yousub Lee
- Adam Stevens
- Akash Jag Prasad
- Alex Roschli
- Alex Walters
- Amit Shyam
- Biruk A Feyissa
- Brian Gibson
- Calen Kimmell
- Cameron Adkins
- Christopher Fancher
- Clay Leach
- Craig Blue
- Debjani Pal
- Emma Betters
- Gordon Robertson
- Greg Corson
- Isha Bhandari
- Jay Reynolds
- Jeff Brookins
- Jesse Heineman
- John Lindahl
- John Potter
- Josh B Harbin
- Liam White
- Luke Meyer
- Michael Borish
- Rangasayee Kannan
- Roger G Miller
- Ryan Dehoff
- Sarah Graham
- Steven Guzorek
- Tony L Schmitz
- Vincent Paquit
- Vladimir Orlyanchik
- Vlastimil Kunc
- William Carter
- William Peter
- Xiaohan Yang
- Yukinori Yamamoto
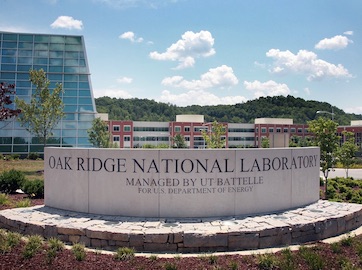
System and method for part porosity monitoring of additively manufactured components using machining
In additive manufacturing, choice of process parameters for a given material and geometry can result in porosities in the build volume, which can result in scrap.
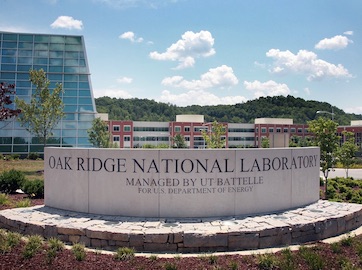
This manufacturing method uses multifunctional materials distributed volumetrically to generate a stiffness-based architecture, where continuous surfaces can be created from flat, rapidly produced geometries.
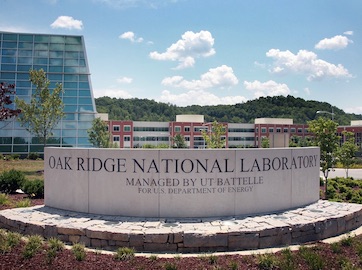
The lack of real-time insights into how materials evolve during laser powder bed fusion has limited the adoption by inhibiting part qualification. The developed approach provides key data needed to fabricate born qualified parts.
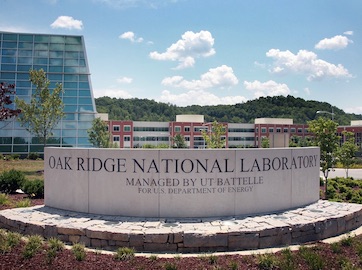
Distortion generated during additive manufacturing of metallic components affect the build as well as the baseplate geometries. These distortions are significant enough to disqualify components for functional purposes.
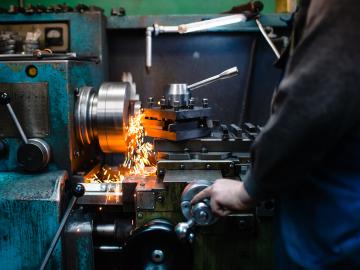
For additive manufacturing of large-scale parts, significant distortion can result from residual stresses during deposition and cooling. This can result in part scraps if the final part geometry is not contained in the additively manufactured preform.
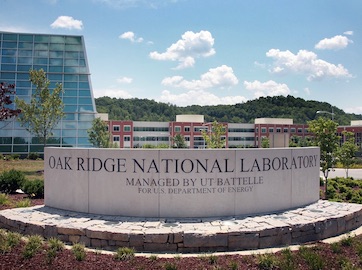
We present the design, assembly and demonstration of functionality for a new custom integrated robotics-based automated soil sampling technology as part of a larger vision for future edge computing- and AI- enabled bioenergy field monitoring and management technologies called
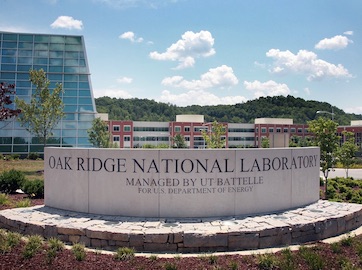
In additive manufacturing large stresses are induced in the build plate and part interface. A result of these stresses are deformations in the build plate and final component.
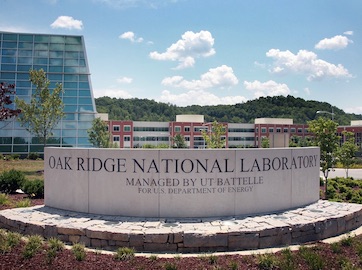
A valve solution that prevents cross contamination while allowing for blocking multiple channels at once using only one actuator.
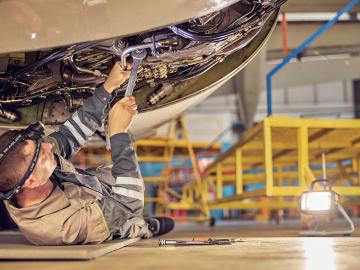
Materials produced via additive manufacturing, or 3D printing, can experience significant residual stress, distortion and cracking, negatively impacting the manufacturing process.