Filter Results
Related Organization
- Biological and Environmental Systems Science Directorate (23)
- Computing and Computational Sciences Directorate (35)
- Energy Science and Technology Directorate (217)
- Fusion and Fission Energy and Science Directorate (21)
- Information Technology Services Directorate (2)
- Isotope Science and Enrichment Directorate (6)
- National Security Sciences Directorate (17)
- Neutron Sciences Directorate (11)
- Physical Sciences Directorate
(128)
- User Facilities (27)
Researcher
- Ryan Dehoff
- Adam Willoughby
- Michael Kirka
- Rishi Pillai
- Vincent Paquit
- Adam Stevens
- Ahmed Hassen
- Alex Plotkowski
- Alice Perrin
- Amir K Ziabari
- Amit Shyam
- Andres Marquez Rossy
- Andrew F May
- Ben Garrison
- Blane Fillingim
- Brad Johnson
- Brandon Johnston
- Brian Post
- Bruce A Pint
- Charles Hawkins
- Charlie Cook
- Christopher Hershey
- Christopher Ledford
- Clay Leach
- Craig Blue
- Daniel Rasmussen
- David Nuttall
- Hsin Wang
- James Haley
- James Klett
- Jiheon Jun
- John Lindahl
- Marie Romedenne
- Mike Zach
- Nedim Cinbiz
- Patxi Fernandez-Zelaia
- Peeyush Nandwana
- Philip Bingham
- Priyanshi Agrawal
- Rangasayee Kannan
- Roger G Miller
- Sarah Graham
- Singanallur Venkatakrishnan
- Sudarsanam Babu
- Tony Beard
- Vipin Kumar
- Vlastimil Kunc
- William Peter
- Yan-Ru Lin
- Ying Yang
- Yong Chae Lim
- Yukinori Yamamoto
- Zhili Feng
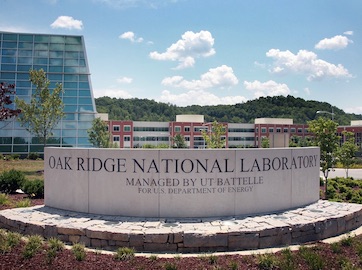
A novel method that prevents detachment of an optical fiber from a metal/alloy tube and allows strain measurement up to higher temperatures, about 800 C has been developed. Standard commercial adhesives typically only survive up to about 400 C.
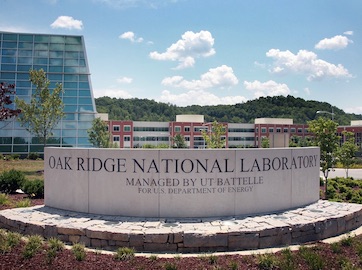
Test facilities to evaluate materials compatibility in hydrogen are abundant for high pressure and low temperature (<100C).
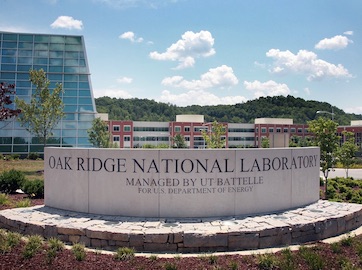
The technologies provide a system and method of needling of veiled AS4 fabric tape.
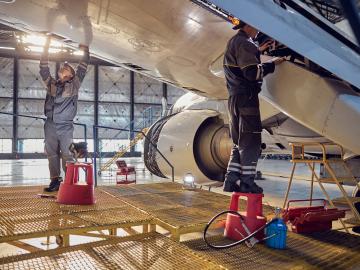
High strength, oxidation resistant refractory alloys are difficult to fabricate for commercial use in extreme environments.
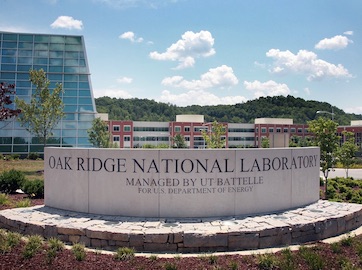
ORNL will develop an advanced high-performing RTG using a novel radioisotope heat source.
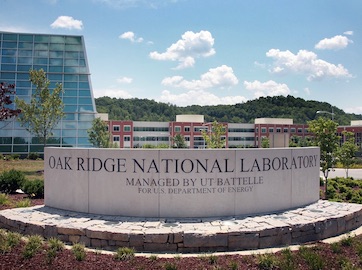
The technologies provide a coating method to produce corrosion resistant and electrically conductive coating layer on metallic bipolar plates for hydrogen fuel cell and hydrogen electrolyzer applications.
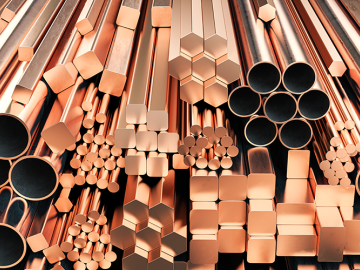
In manufacturing parts for industry using traditional molds and dies, about 70 percent to 80 percent of the time it takes to create a part is a result of a relatively slow cooling process.
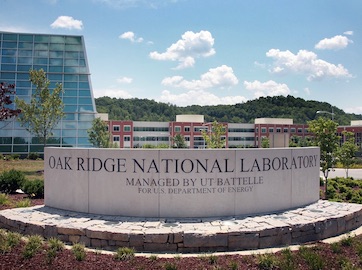
The technology provides a transformational approach to digitally manufacture structural alloys with co- optimized strength and environmental resistance
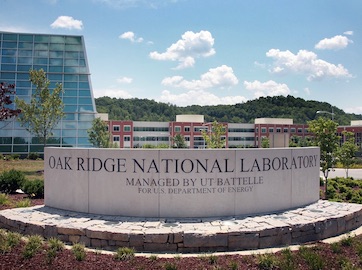
This technology combines 3D printing and compression molding to produce high-strength, low-porosity composite articles.