Filter Results
Related Organization
- Biological and Environmental Systems Science Directorate
(29)
- Computing and Computational Sciences Directorate (39)
- Energy Science and Technology Directorate (229)
- Fusion and Fission Energy and Science Directorate (24)
- Information Technology Services Directorate (3)
- Isotope Science and Enrichment Directorate (7)
- National Security Sciences Directorate (20)
- Neutron Sciences Directorate (11)
- Physical Sciences Directorate
(138)
- User Facilities (28)
Researcher
- Ryan Dehoff
- Michael Kirka
- Soydan Ozcan
- Vincent Paquit
- Xianhui Zhao
- Ying Yang
- Adam Stevens
- Ahmed Hassen
- Alex Plotkowski
- Alex Roschli
- Alice Perrin
- Amir K Ziabari
- Amit Shyam
- Andres Marquez Rossy
- Ben Lamm
- Beth L Armstrong
- Blane Fillingim
- Brian Post
- Bruce A Pint
- Christopher Ledford
- Clay Leach
- David Nuttall
- Erin Webb
- Evin Carter
- Halil Tekinalp
- James Haley
- Jeremy Malmstead
- Kitty K Mccracken
- Meghan Lamm
- Oluwafemi Oyedeji
- Patxi Fernandez-Zelaia
- Peeyush Nandwana
- Philip Bingham
- Rangasayee Kannan
- Roger G Miller
- Sanjita Wasti
- Sarah Graham
- Shajjad Chowdhury
- Steven J Zinkle
- Sudarsanam Babu
- Tim Graening Seibert
- Tolga Aytug
- Tyler Smith
- Venkatakrishnan Singanallur Vaidyanathan
- Vipin Kumar
- Vlastimil Kunc
- Weicheng Zhong
- Wei Tang
- William Peter
- Xiang Chen
- Yan-Ru Lin
- Yanli Wang
- Yukinori Yamamoto
- Yutai Kato
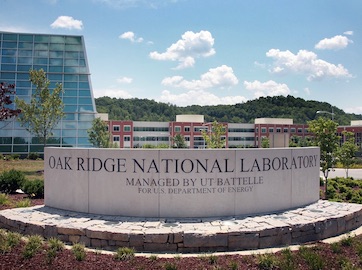
We have developed a novel extrusion-based 3D printing technique that can achieve a resolution of 0.51 mm layer thickness, and catalyst loading of 44% and 90.5% before and after drying, respectively.
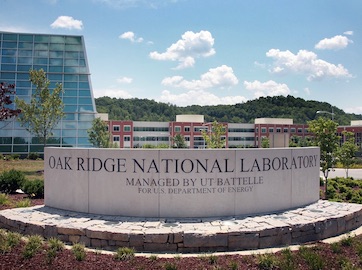
The use of biomass fiber reinforcement for polymer composite applications, like those in buildings or automotive, has expanded rapidly due to the low cost, high stiffness, and inherent renewability of these materials. Biomass are commonly disposed of as waste.
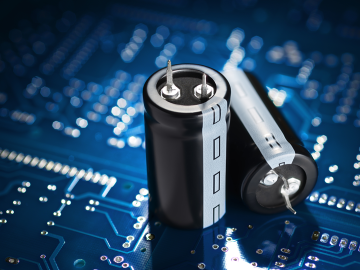
New demands in electric vehicles have resulted in design changes for the power electronic components such as the capacitor to incur lower volume, higher operating temperatures, and dielectric properties (high dielectric permittivity and high electrical breakdown strengths).

High strength, oxidation resistant refractory alloys are difficult to fabricate for commercial use in extreme environments.
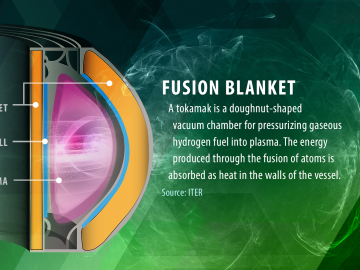
The first wall and blanket of a fusion energy reactor must maintain structural integrity and performance over long operational periods under neutron irradiation and minimize long-lived radioactive waste.

In manufacturing parts for industry using traditional molds and dies, about 70 percent to 80 percent of the time it takes to create a part is a result of a relatively slow cooling process.
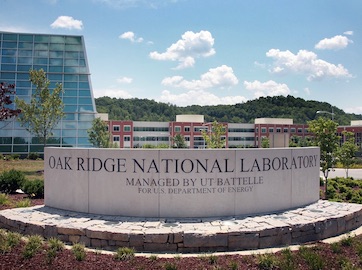
This technology combines 3D printing and compression molding to produce high-strength, low-porosity composite articles.
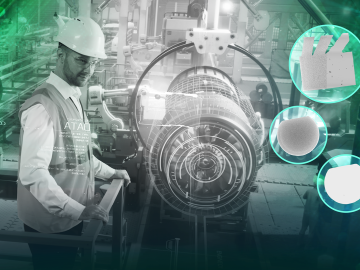
Simurgh revolutionizes industrial CT imaging with AI, enhancing speed and accuracy in nondestructive testing for complex parts, reducing costs.
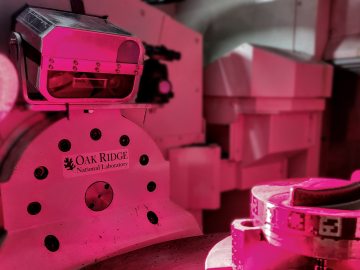
An innovative low-cost system for in-situ monitoring of strain and temperature during directed energy deposition.