Filter Results
Related Organization
- Biological and Environmental Systems Science Directorate (23)
- Computing and Computational Sciences Directorate (35)
- Energy Science and Technology Directorate (217)
- Fusion and Fission Energy and Science Directorate (21)
- Information Technology Services Directorate (2)
- Isotope Science and Enrichment Directorate (6)
- National Security Sciences Directorate (17)
- Neutron Sciences Directorate (11)
- Physical Sciences Directorate (128)
- User Facilities (27)
Researcher
- Ryan Dehoff
- Vlastimil Kunc
- William Carter
- Ahmed Hassen
- Alex Roschli
- Andrzej Nycz
- Brian Post
- Chris Masuo
- Luke Meyer
- Michael Kirka
- Vincent Paquit
- Vipin Kumar
- Adam Stevens
- Alex Plotkowski
- Alex Walters
- Alice Perrin
- Amir K Ziabari
- Amit Shyam
- Amy Elliott
- Andres Marquez Rossy
- Blane Fillingim
- Cameron Adkins
- Christopher Ledford
- Clay Leach
- Dan Coughlin
- David Nuttall
- Erin Webb
- Evin Carter
- Isha Bhandari
- James Haley
- Jeremy Malmstead
- Jim Tobin
- Josh Crabtree
- Joshua Vaughan
- Kim Sitzlar
- Kitty K Mccracken
- Liam White
- Merlin Theodore
- Michael Borish
- Oluwafemi Oyedeji
- Patxi Fernandez-Zelaia
- Peeyush Nandwana
- Peter Wang
- Philip Bingham
- Rangasayee Kannan
- Roger G Miller
- Sarah Graham
- Singanallur Venkatakrishnan
- Soydan Ozcan
- Steven Guzorek
- Subhabrata Saha
- Sudarsanam Babu
- Tyler Smith
- William Peter
- Xianhui Zhao
- Yan-Ru Lin
- Ying Yang
- Yukinori Yamamoto
1 - 10 of 15 Results
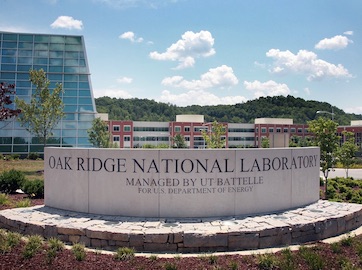
The use of biomass fiber reinforcement for polymer composite applications, like those in buildings or automotive, has expanded rapidly due to the low cost, high stiffness, and inherent renewability of these materials. Biomass are commonly disposed of as waste.
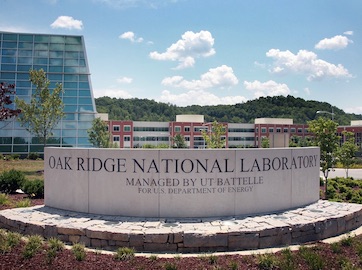
Through the use of splicing methods, joining two different fiber types in the tow stage of the process enables great benefits to the strength of the material change.
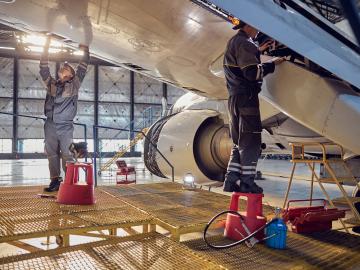
High strength, oxidation resistant refractory alloys are difficult to fabricate for commercial use in extreme environments.
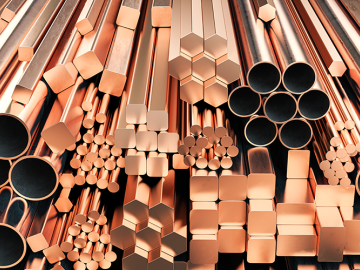
In manufacturing parts for industry using traditional molds and dies, about 70 percent to 80 percent of the time it takes to create a part is a result of a relatively slow cooling process.