Filter Results
Related Organization
- Biological and Environmental Systems Science Directorate (23)
- Computing and Computational Sciences Directorate (35)
- Energy Science and Technology Directorate (217)
- Fusion and Fission Energy and Science Directorate (21)
- Information Technology Services Directorate (2)
- Isotope Science and Enrichment Directorate (6)
- National Security Sciences Directorate (17)
- Neutron Sciences Directorate (11)
- Physical Sciences Directorate
(128)
- User Facilities (27)
Researcher
- Corson Cramer
- Steve Bullock
- Amit Shyam
- Alex Plotkowski
- Greg Larsen
- James Klett
- Ryan Dehoff
- Trevor Aguirre
- James A Haynes
- Sumit Bahl
- Vincent Paquit
- Vlastimil Kunc
- Adam Stevens
- Ahmed Hassen
- Akash Jag Prasad
- Alice Perrin
- Andres Marquez Rossy
- Beth L Armstrong
- Brian Post
- Calen Kimmell
- Canhai Lai
- Charlie Cook
- Christopher Fancher
- Christopher Hershey
- Christopher Ledford
- Chris Tyler
- Clay Leach
- Costas Tsouris
- Craig Blue
- Daniel Rasmussen
- David J Mitchell
- Dean T Pierce
- Dustin Gilmer
- Gerry Knapp
- Gordon Robertson
- James Haley
- James Parks II
- Jaydeep Karandikar
- Jay Reynolds
- Jeff Brookins
- John Lindahl
- Jordan Wright
- Jovid Rakhmonov
- Michael Kirka
- Nadim Hmeidat
- Nicholas Richter
- Peeyush Nandwana
- Peter Wang
- Rangasayee Kannan
- Roger G Miller
- Sana Elyas
- Sarah Graham
- Steven Guzorek
- Sudarsanam Babu
- Sunyong Kwon
- Tomonori Saito
- Tony Beard
- Vladimir Orlyanchik
- William Peter
- Ying Yang
- Yukinori Yamamoto
- Zackary Snow
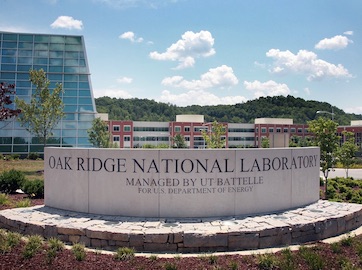
Currently available cast Al alloys are not suitable for various high-performance conductor applications, such as rotor, inverter, windings, busbar, heat exchangers/sinks, etc.
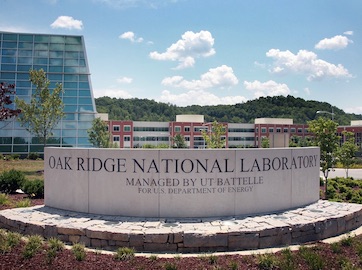
The invented alloys are a new family of Al-Mg alloys. This new family of Al-based alloys demonstrate an excellent ductility (10 ± 2 % elongation) despite the high content of impurities commonly observed in recycled aluminum.
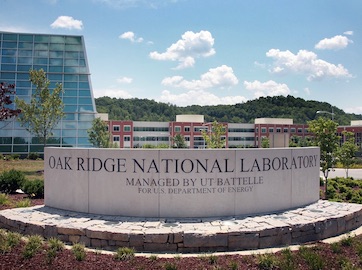
The technologies provide additively manufactured thermal protection system.
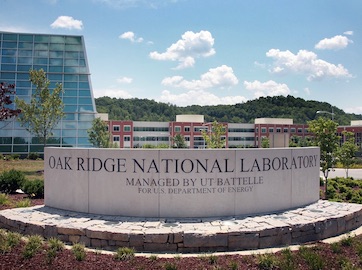
System and method for part porosity monitoring of additively manufactured components using machining
In additive manufacturing, choice of process parameters for a given material and geometry can result in porosities in the build volume, which can result in scrap.
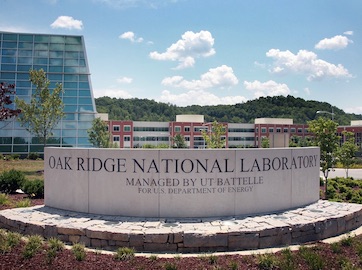
The lack of real-time insights into how materials evolve during laser powder bed fusion has limited the adoption by inhibiting part qualification. The developed approach provides key data needed to fabricate born qualified parts.
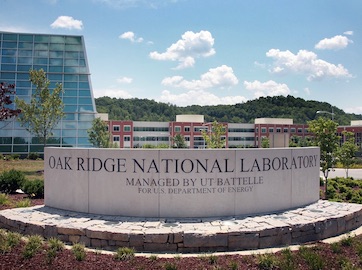
This invention focuses on improving the ceramic yield of preceramic polymers by tuning the crosslinking process that occurs during vat photopolymerization (VP).
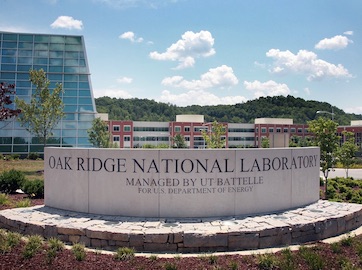
Using all polymer formulations, the PIP densification is improved almost 70% over traditional preceramic polymers and PIP material leading to cost and times saving for densifying ceramic composites made from powder or fibers.
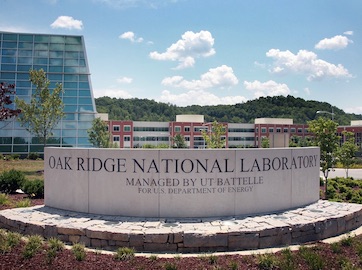
Sensing of additive manufacturing processes promises to facilitate detailed quality inspection at scales that have seldom been seen in traditional manufacturing processes.
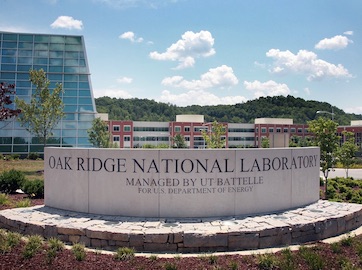
The technologies provide a system and method of needling of veiled AS4 fabric tape.