Filter Results
Related Organization
- Biological and Environmental Systems Science Directorate (23)
- Computing and Computational Sciences Directorate (35)
- Energy Science and Technology Directorate (217)
- Fusion and Fission Energy and Science Directorate (21)
- Information Technology Services Directorate (2)
- Isotope Science and Enrichment Directorate (6)
- National Security Sciences Directorate (17)
- Neutron Sciences Directorate (11)
- Physical Sciences Directorate
(128)
- User Facilities (27)
Researcher
- Amit Shyam
- Alex Plotkowski
- William Carter
- Alex Roschli
- Andrzej Nycz
- Brian Post
- Chris Masuo
- James A Haynes
- Luke Meyer
- Peter Wang
- Ryan Dehoff
- Sumit Bahl
- Ying Yang
- Adam Stevens
- Alex Walters
- Alice Perrin
- Amy Elliott
- Andres Marquez Rossy
- Ben Lamm
- Beth L Armstrong
- Bruce A Pint
- Cameron Adkins
- Christopher Fancher
- Dean T Pierce
- Erin Webb
- Evin Carter
- Gerry Knapp
- Gordon Robertson
- Isha Bhandari
- Jay Reynolds
- Jeff Brookins
- Jeremy Malmstead
- Joshua Vaughan
- Jovid Rakhmonov
- Kitty K Mccracken
- Liam White
- Meghan Lamm
- Michael Borish
- Nicholas Richter
- Oluwafemi Oyedeji
- Peeyush Nandwana
- Rangasayee Kannan
- Roger G Miller
- Sarah Graham
- Shajjad Chowdhury
- Soydan Ozcan
- Steven J Zinkle
- Sudarsanam Babu
- Sunyong Kwon
- Tim Graening Seibert
- Tolga Aytug
- Tyler Smith
- Weicheng Zhong
- Wei Tang
- William Peter
- Xiang Chen
- Xianhui Zhao
- Yanli Wang
- Yukinori Yamamoto
- Yutai Kato
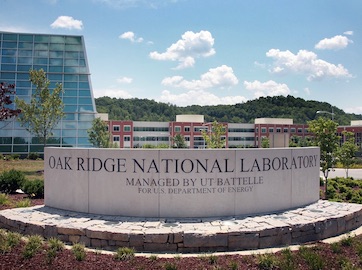
Currently available cast Al alloys are not suitable for various high-performance conductor applications, such as rotor, inverter, windings, busbar, heat exchangers/sinks, etc.
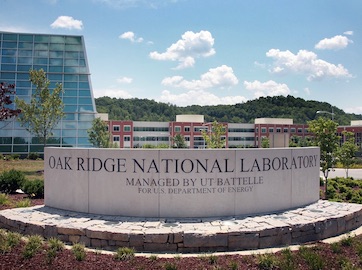
The invented alloys are a new family of Al-Mg alloys. This new family of Al-based alloys demonstrate an excellent ductility (10 ± 2 % elongation) despite the high content of impurities commonly observed in recycled aluminum.
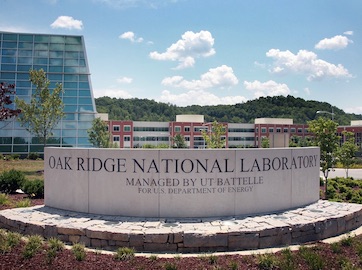
The lack of real-time insights into how materials evolve during laser powder bed fusion has limited the adoption by inhibiting part qualification. The developed approach provides key data needed to fabricate born qualified parts.
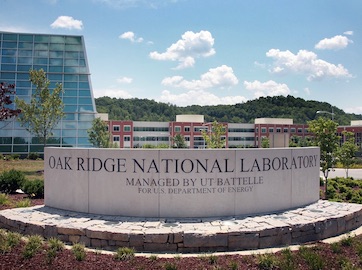
The use of biomass fiber reinforcement for polymer composite applications, like those in buildings or automotive, has expanded rapidly due to the low cost, high stiffness, and inherent renewability of these materials. Biomass are commonly disposed of as waste.
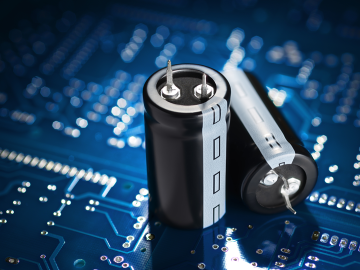
New demands in electric vehicles have resulted in design changes for the power electronic components such as the capacitor to incur lower volume, higher operating temperatures, and dielectric properties (high dielectric permittivity and high electrical breakdown strengths).