Filter Results
Related Organization
- Biological and Environmental Systems Science Directorate (23)
- Computing and Computational Sciences Directorate (35)
- Energy Science and Technology Directorate (217)
- Fusion and Fission Energy and Science Directorate
(21)
- Information Technology Services Directorate (2)
- Isotope Science and Enrichment Directorate (6)
- National Security Sciences Directorate (17)
- Neutron Sciences Directorate (11)
- Physical Sciences Directorate (128)
- User Facilities (27)
Researcher
- Brian Post
- Chris Tyler
- Justin West
- Peter Wang
- Ritin Mathews
- Andrzej Nycz
- Blane Fillingim
- Chris Masuo
- Peeyush Nandwana
- Sudarsanam Babu
- Thomas Feldhausen
- Adam Stevens
- Ahmed Hassen
- David Olvera Trejo
- J.R. R Matheson
- Jaydeep Karandikar
- Joshua Vaughan
- Lauren Heinrich
- Michael Kirka
- Rangasayee Kannan
- Ryan Dehoff
- Scott Smith
- William Carter
- Yousub Lee
- Akash Jag Prasad
- Alex Roschli
- Amir K Ziabari
- Amit Shyam
- Amy Elliott
- Beth L Armstrong
- Brian Gibson
- Calen Kimmell
- Callie Goetz
- Cameron Adkins
- Christopher Fancher
- Christopher Hobbs
- Christopher Ledford
- Corson Cramer
- Craig Blue
- Eddie Lopez Honorato
- Emma Betters
- Fred List III
- Gordon Robertson
- Greg Corson
- Isha Bhandari
- James Klett
- Jay Reynolds
- Jeff Brookins
- Jesse Heineman
- John Lindahl
- John Potter
- Josh B Harbin
- Keith Carver
- Liam White
- Luke Meyer
- Matt Kurley III
- Michael Borish
- Philip Bingham
- Richard Howard
- Rodney D Hunt
- Roger G Miller
- Ryan Heldt
- Sarah Graham
- Singanallur Venkatakrishnan
- Steve Bullock
- Steven Guzorek
- Thomas Butcher
- Tony L Schmitz
- Trevor Aguirre
- Tyler Gerczak
- Vincent Paquit
- Vladimir Orlyanchik
- Vlastimil Kunc
- William Peter
- Yukinori Yamamoto
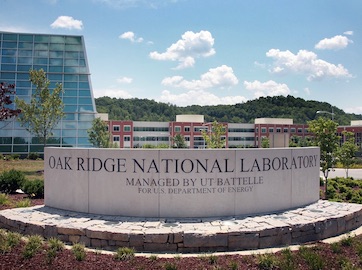
The use of Fluidized Bed Chemical Vapor Deposition to coat particles or fibers is inherently slow and capital intensive, as it requires constant modifications to the equipment to account for changes in the characteristics of the substrates to be coated.
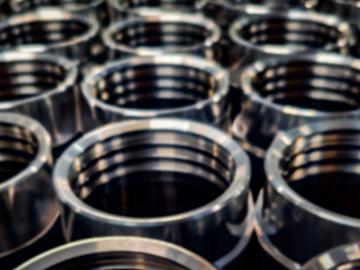
Complex protective casings and housings are necessary for many applications, including combustion chambers of gas turbines used in aerospace engines. Manufacturing these components from forging and/or casting as a whole is challenging, costly, and time-consuming.
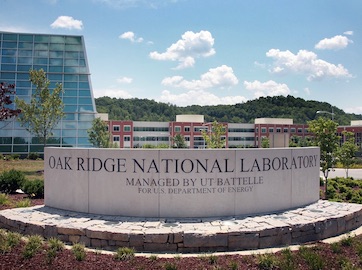
Compliance in a part, work holding, or base plate is beneficial for certain processes, but detrimental for machining and material removal.
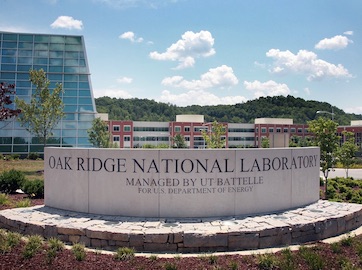
In additive manufacturing large stresses are induced in the build plate and part interface. A result of theses stresses are deformations in the build plate and final component.
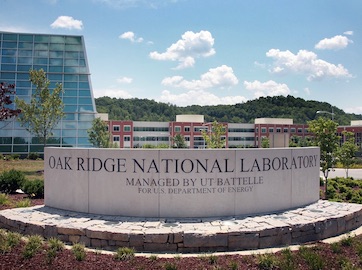
In wire-arc additive manufacturing and hot-wire laser additive manufacturing, wire is fed into a melt pool and melted through the arc or laser process.
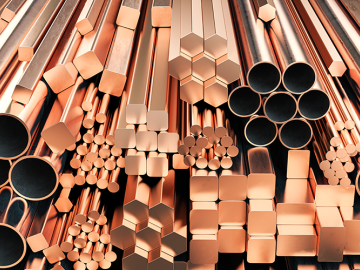
In manufacturing parts for industry using traditional molds and dies, about 70 percent to 80 percent of the time it takes to create a part is a result of a relatively slow cooling process.
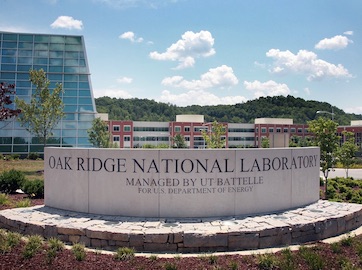
This technology aims to provide and integrated and oxidation resistant cladding or coating onto carbon-based composites in seconds.