Filter Results
Related Organization
- Biological and Environmental Systems Science Directorate (23)
- Computing and Computational Sciences Directorate (35)
- Energy Science and Technology Directorate (217)
- Fusion and Fission Energy and Science Directorate
(21)
- Information Technology Services Directorate (2)
- Isotope Science and Enrichment Directorate (6)
- National Security Sciences Directorate (17)
- Neutron Sciences Directorate (11)
- Physical Sciences Directorate (128)
- User Facilities (27)
Researcher
- Brian Post
- Sudarsanam Babu
- William Carter
- Alex Roschli
- Andrzej Nycz
- Blane Fillingim
- Chris Masuo
- Lauren Heinrich
- Luke Meyer
- Peeyush Nandwana
- Thomas Feldhausen
- Yousub Lee
- Adam Stevens
- Alex Walters
- Amy Elliott
- Cameron Adkins
- Christopher Hobbs
- Eddie Lopez Honorato
- Erin Webb
- Evin Carter
- Isha Bhandari
- Jeremy Malmstead
- Joshua Vaughan
- Kitty K Mccracken
- Liam White
- Matt Kurley III
- Michael Borish
- Oluwafemi Oyedeji
- Peter Wang
- Ramanan Sankaran
- Rangasayee Kannan
- Rodney D Hunt
- Roger G Miller
- Ryan Dehoff
- Ryan Heldt
- Sarah Graham
- Soydan Ozcan
- Tyler Gerczak
- Tyler Smith
- Vimal Ramanuj
- Wenjun Ge
- William Peter
- Xianhui Zhao
- Yukinori Yamamoto
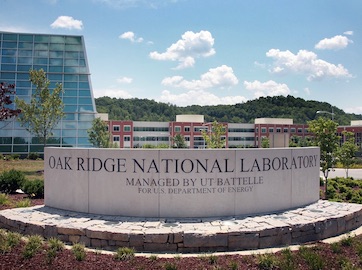
Sintering additives to improve densification and microstructure control of UN provides a facile approach to producing high quality nuclear fuels.
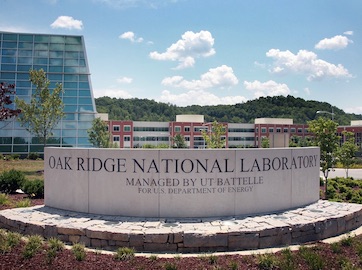
The use of biomass fiber reinforcement for polymer composite applications, like those in buildings or automotive, has expanded rapidly due to the low cost, high stiffness, and inherent renewability of these materials. Biomass are commonly disposed of as waste.
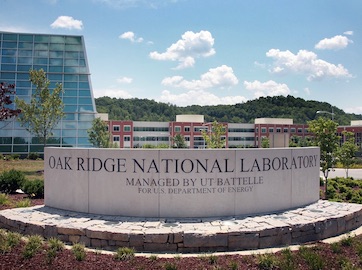
This work seeks to alter the interface condition through thermal history modification, deposition energy density, and interface surface preparation to prevent interface cracking.
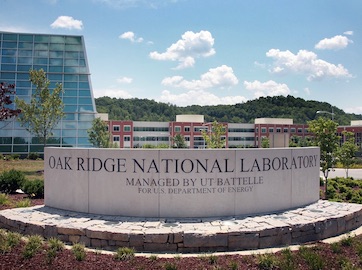
Additive manufacturing (AM) enables the incremental buildup of monolithic components with a variety of materials, and material deposition locations.
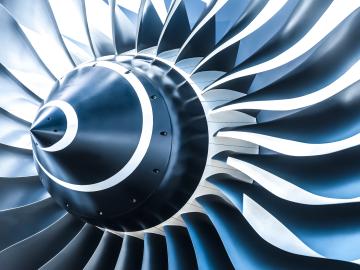
Ceramic matrix composites are used in several industries, such as aerospace, for lightweight, high quality and high strength materials. But producing them is time consuming and often low quality.
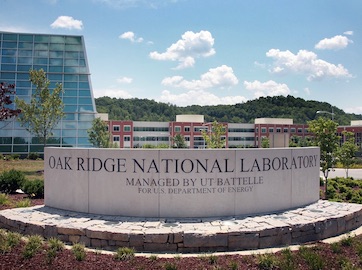
The use of Fluidized Bed Chemical Vapor Deposition to coat particles or fibers is inherently slow and capital intensive, as it requires constant modifications to the equipment to account for changes in the characteristics of the substrates to be coated.