Filter Results
Related Organization
- Biological and Environmental Systems Science Directorate (29)
- Computing and Computational Sciences Directorate (39)
- Energy Science and Technology Directorate (229)
- Fusion and Fission Energy and Science Directorate
(24)
- Information Technology Services Directorate (3)
- Isotope Science and Enrichment Directorate (7)
- National Security Sciences Directorate (20)
- Neutron Sciences Directorate (11)
- Physical Sciences Directorate (138)
- User Facilities (28)
Researcher
- Andrzej Nycz
- Chris Masuo
- Peter Wang
- Alex Walters
- Brian Post
- Hongbin Sun
- Blane Fillingim
- Brian Gibson
- Joshua Vaughan
- Lauren Heinrich
- Luke Meyer
- Peeyush Nandwana
- Prashant Jain
- Sudarsanam Babu
- Thomas Feldhausen
- Udaya C Kalluri
- William Carter
- Yousub Lee
- Akash Jag Prasad
- Alexander I Wiechert
- Amit Shyam
- Calen Kimmell
- Chelo Chavez
- Christopher Fancher
- Chris Tyler
- Clay Leach
- Costas Tsouris
- Debangshu Mukherjee
- Gordon Robertson
- Gs Jung
- Gyoung Gug Jang
- Ian Greenquist
- Ilias Belharouak
- J.R. R Matheson
- Jaydeep Karandikar
- Jay Reynolds
- Jeff Brookins
- Jesse Heineman
- John Potter
- Md Inzamam Ul Haque
- Nate See
- Nithin Panicker
- Olga S Ovchinnikova
- Pradeep Ramuhalli
- Praveen Cheekatamarla
- Radu Custelcean
- Ramanan Sankaran
- Riley Wallace
- Ritin Mathews
- Ruhul Amin
- Thien D. Nguyen
- Vimal Ramanuj
- Vincent Paquit
- Vishaldeep Sharma
- Vittorio Badalassi
- Vladimir Orlyanchik
- Wenjun Ge
- Xiaohan Yang
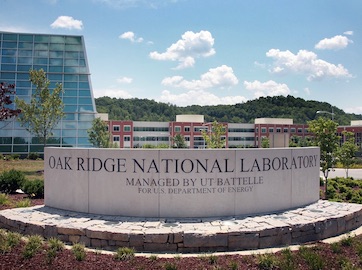
In nuclear and industrial facilities, fine particles, including radioactive residues—can accumulate on the interior surfaces of ventilation ducts and equipment, posing serious safety and operational risks.
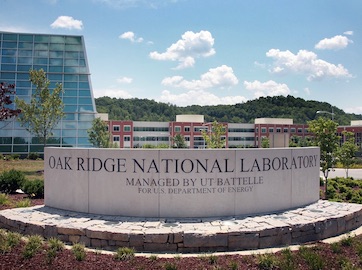
System and method for part porosity monitoring of additively manufactured components using machining
In additive manufacturing, choice of process parameters for a given material and geometry can result in porosities in the build volume, which can result in scrap.
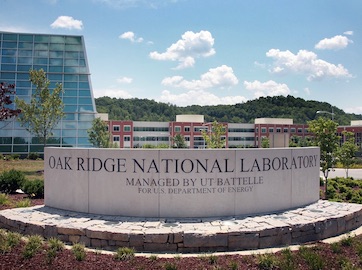
The invention presented here addresses key challenges associated with counterfeit refrigerants by ensuring safety, maintaining system performance, supporting environmental compliance, and mitigating health and legal risks.
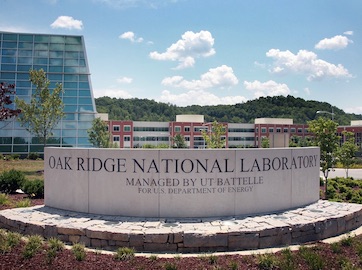
Among the methods for point source carbon capture, the absorption of CO2 using aqueous amines (namely MEA) from the post-combustion gas stream is currently considered the most promising.
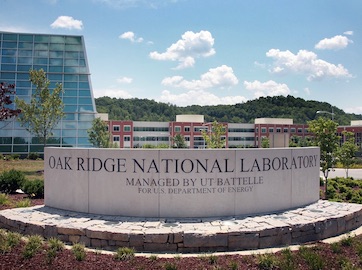
The lack of real-time insights into how materials evolve during laser powder bed fusion has limited the adoption by inhibiting part qualification. The developed approach provides key data needed to fabricate born qualified parts.
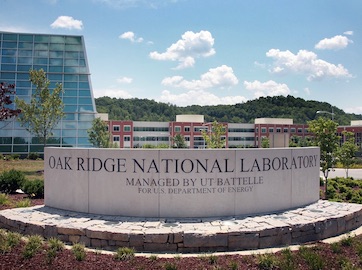
A novel approach is presented herein to improve time to onset of natural convection stemming from fuel element porosity during a failure mode of a nuclear reactor.
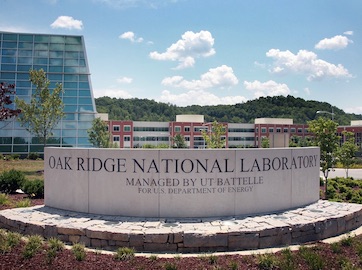
We present the design, assembly and demonstration of functionality for a new custom integrated robotics-based automated soil sampling technology as part of a larger vision for future edge computing- and AI- enabled bioenergy field monitoring and management technologies called
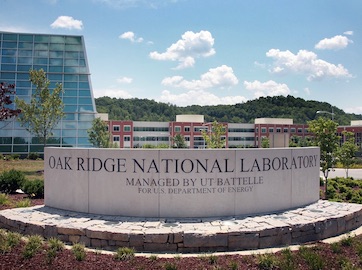
Creating a framework (method) for bots (agents) to autonomously, in real time, dynamically divide and execute a complex manufacturing (or any suitable) task in a collaborative, parallel-sequential way without required human interaction.
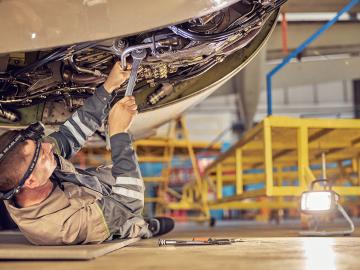
Materials produced via additive manufacturing, or 3D printing, can experience significant residual stress, distortion and cracking, negatively impacting the manufacturing process.
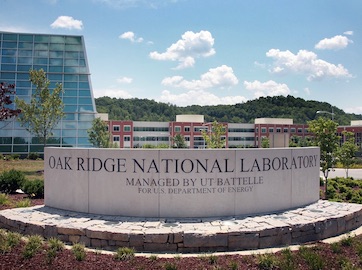
This work seeks to alter the interface condition through thermal history modification, deposition energy density, and interface surface preparation to prevent interface cracking.