Filter Results
Related Organization
- Biological and Environmental Systems Science Directorate (23)
- Computing and Computational Sciences Directorate (35)
- Energy Science and Technology Directorate (217)
- Fusion and Fission Energy and Science Directorate (21)
- Information Technology Services Directorate (2)
- Isotope Science and Enrichment Directorate (6)
- National Security Sciences Directorate (17)
- Neutron Sciences Directorate (11)
- Physical Sciences Directorate (128)
- User Facilities (27)
Researcher
- Chris Tyler
- Justin West
- Ritin Mathews
- Alex Plotkowski
- Amit Shyam
- Isabelle Snyder
- David Olvera Trejo
- Emilio Piesciorovsky
- J.R. R Matheson
- James A Haynes
- Jaydeep Karandikar
- Scott Smith
- Sumit Bahl
- Aaron Werth
- Aaron Wilson
- Adam Siekmann
- Akash Jag Prasad
- Alice Perrin
- Ali Riza Ekti
- Andres Marquez Rossy
- Brian Gibson
- Brian Post
- Calen Kimmell
- Elizabeth Piersall
- Emma Betters
- Eve Tsybina
- Gary Hahn
- Gerry Knapp
- Greg Corson
- Jesse Heineman
- John Potter
- Josh B Harbin
- Jovid Rakhmonov
- Nicholas Richter
- Nils Stenvig
- Ozgur Alaca
- Peeyush Nandwana
- Raymond Borges Hink
- Ryan Dehoff
- Subho Mukherjee
- Sunyong Kwon
- Tony L Schmitz
- Viswadeep Lebakula
- Vivek Sujan
- Vladimir Orlyanchik
- Yarom Polsky
- Ying Yang
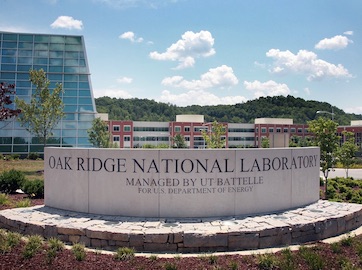
Currently available cast Al alloys are not suitable for various high-performance conductor applications, such as rotor, inverter, windings, busbar, heat exchangers/sinks, etc.
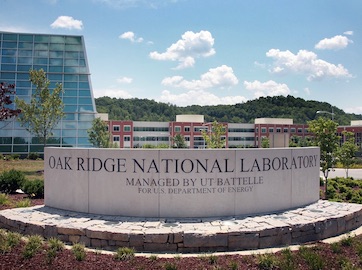
The invented alloys are a new family of Al-Mg alloys. This new family of Al-based alloys demonstrate an excellent ductility (10 ± 2 % elongation) despite the high content of impurities commonly observed in recycled aluminum.
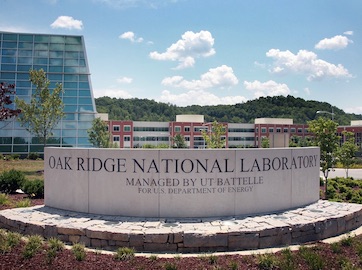
System and method for part porosity monitoring of additively manufactured components using machining
In additive manufacturing, choice of process parameters for a given material and geometry can result in porosities in the build volume, which can result in scrap.
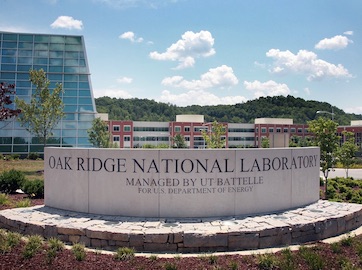
Distortion generated during additive manufacturing of metallic components affect the build as well as the baseplate geometries. These distortions are significant enough to disqualify components for functional purposes.
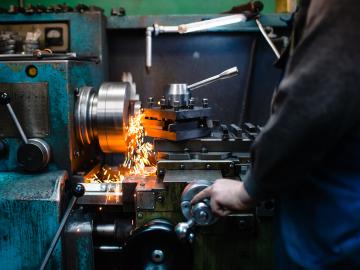
For additive manufacturing of large-scale parts, significant distortion can result from residual stresses during deposition and cooling. This can result in part scraps if the final part geometry is not contained in the additively manufactured preform.
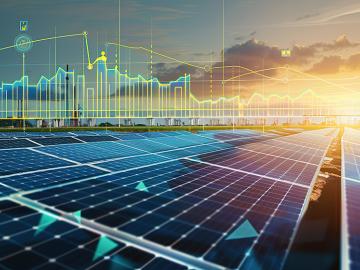
Faults in the power grid cause many problems that can result in catastrophic failures. Real-time fault detection in the power grid system is crucial to sustain the power systems' reliability, stability, and quality.
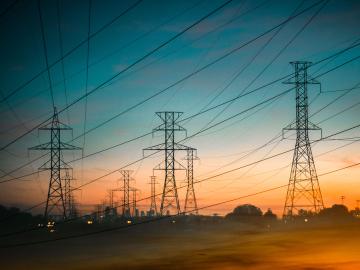
Water heaters and heating, ventilation, and air conditioning (HVAC) systems collectively consume about 58% of home energy use.
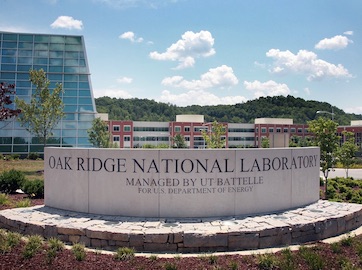
In additive manufacturing large stresses are induced in the build plate and part interface. A result of these stresses are deformations in the build plate and final component.
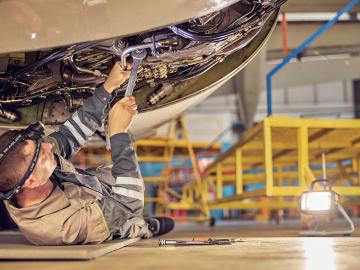
Materials produced via additive manufacturing, or 3D printing, can experience significant residual stress, distortion and cracking, negatively impacting the manufacturing process.